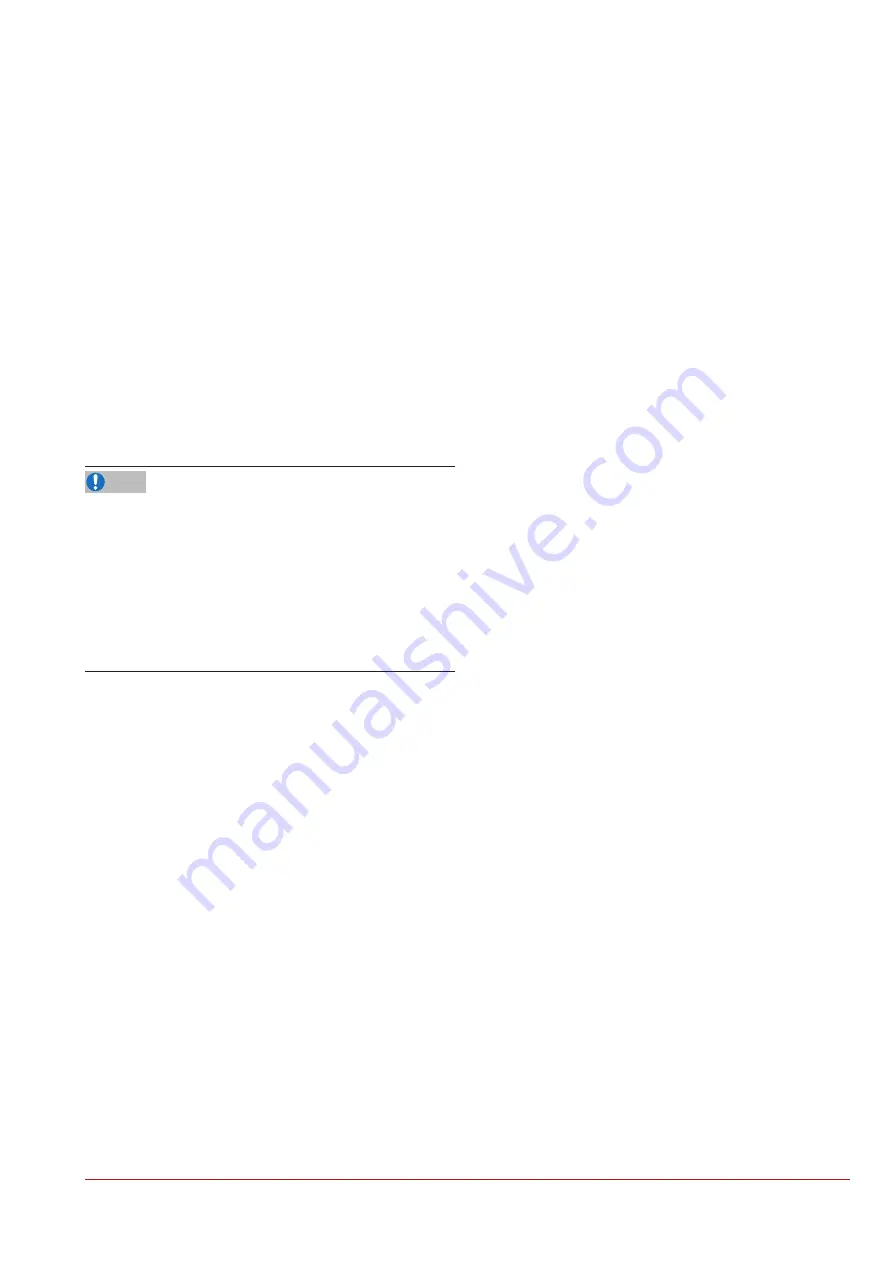
3-1
EB 01b_EN
February 2022 edition
Subject to technical changes
Design and principle of operation
3
Design and principle of operation
Function and principle of operation
The medium
fl
ows through the valve in the closing direction.
The position of the plug determines the cross-sectional area be-
tween the plug (4) and the seat (3), see Figure 3-1 and Fig-
ure 3-3.
The plug is connected via the stem (12) to the actuator stem.
The PTFE bellows (5) seals the area between the valve body (1)
and the stem (12).
The PTFE V-ring packing (15) is used as additional stem sealing.
They permit, in connection with the test connection (13), checking
the bellows (5) e.g. by connecting a suction line or inert gas line.
The plug (4) is easy to replace thanks to the groove-spring con-
nection with the PTFE bellows connection in the form of a PTFE
cord (6).
The PTFE seat (3) screwed into the valve body (1) using a thread
suitable for plastic.
Damage to the valve due to cavitation!
The valve can damaged due to cavitation.
Ö
At the onset of cavitation, differential pressures above 3 bar
and a differential pressure ratio of p2 <
∆
p, PFEIFFER recom-
mends using a guided plug!
Ö
It is also recommended to use
fi
ttings made of ceramic or re-
sistant special metals.
Lined valves are not suitable for operation with cavitation. Con-
tact PFEIFFER in the case of questions.
Fail-safe positions
Depending on the mounting of the pneumatic actuator, the valve
has two fail-safe positions that are activated when the pressure is
released as well when the supply air fails:
−
Valve with fail-close actuator:
Upon air failure, the valve is closed. The valve opens when
the signal pressure increases, acting against the force of the
springs.
−
Valve with fail-open actuator:
Upon air failure, the valve is opened. The valve closes when
the signal pressure increases, acting against the force of the
springs.
Changing the fail-safe position
The fail-safe position of the actuator can be reversed if required,
for this purpose see the installation and operating instructions for
the respective pneumatic actuator.
NOTE
Operating elements and functions
The BR 01b valve can be selected in the following versions:
−
With a pneumatic SAMSON actuator.
−
With a manual SAMSON actuator.
−
With actuators from other manufacturers.
3.1 Variations
−
Lining with special compounds, e. g. PFA conductive.
−
Flange with groove
−
Select the BR 01a valve for special requirements.
3.2 Additional
fi
ttings
Strainer
PFEIFFER recommends installing a strainer in front of the valve
body. A strainer prevents the solid content in the medium from
damaging the valve.
Bypass and shut-off valve
PFEIFFER recommends installing a shut-off valve in front of the
strainer as well as behind the valve and to create a bypass. By
means of the bypass, the entire plant does not have to be decom-
missioned during maintenance and repair work on the valve.
Insulation
The valves can be insulated to reduce the passage of heat ener-
gy.
Observe the notes in Chapter “ 5 Assembly”.
Test connection
In the version with bellows sealing, a test connection (e.g. G¼“)
can be used on the upper
fl
ange to check the tightness of the bel-
lows.
Grip protection
In the case of conditions of use that require a high level of safety
(e. g. if the valve is freely accessible to untrained specialist per-
sonnel), PFEIFFER offers a safety guard to prevent the risk of
crushing due to moving parts (actuator stem and stem).
The risk assessment of the plant by the operator will indicate if
the installation of this protective device is required for the safe
operation of the valve in the plant.
Summary of Contents for EB 01b
Page 28: ...5 6 EB 01b_EN February 2022 edition Subject to technical changes Installation...
Page 30: ...6 2 EB 01b_EN February 2022 edition Subject to technical changes Start up...
Page 32: ...7 2 EB 01b_EN February 2022 edition Subject to technical changes Operation...
Page 36: ...8 4 EB 01b_EN February 2022 edition Subject to technical changes Malfunction...
Page 40: ...10 2 EB 01b_EN February 2022 edition Subject to technical changes Decommissioning...
Page 42: ...11 2 EB 01b_EN February 2022 edition Subject to technical changes Removal...
Page 48: ...13 2 EB 01b_EN February 2022 edition Subject to technical changes Disposal...
Page 50: ...14 2 EB 01b_EN February 2022 edition Subject to technical changes Certificates...
Page 51: ...14 3 EB 01b_EN February 2022 edition Subject to technical changes Certificates...
Page 52: ...14 4 EB 01b_EN February 2022 edition Subject to technical changes Certificates...
Page 53: ...14 5 EB 01b_EN February 2022 edition Subject to technical changes Certificates...
Page 54: ...14 6 EB 01b_EN February 2022 edition Subject to technical changes Certificates...
Page 61: ...EB 01b_EN February 2022 edition Subject to technical changes...
Page 62: ...EB 01b_EN February 2022 edition Subject to technical changes...
Page 63: ...EB 01b_EN February 2022 edition Subject to technical changes...