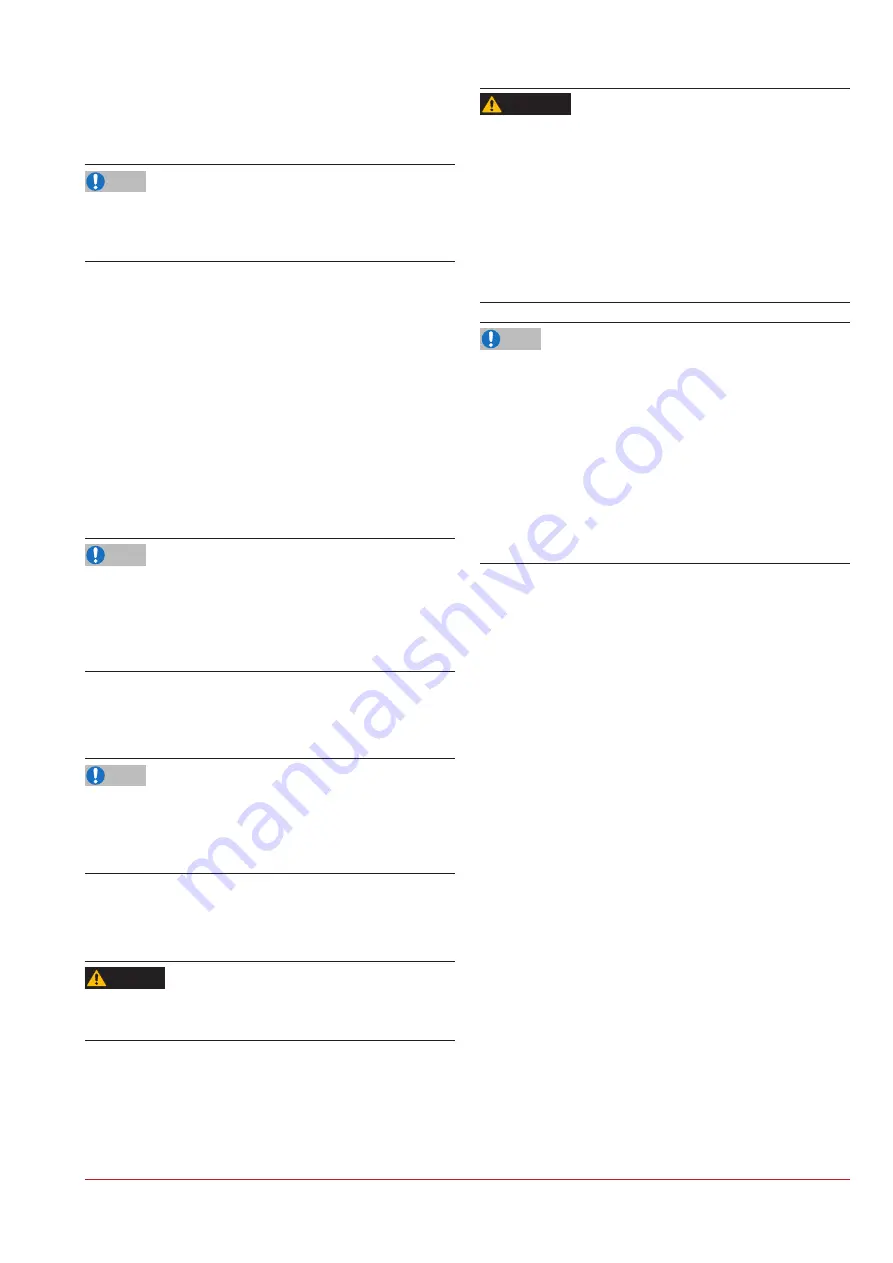
4-1
EB 01b_EN
February 2022 edition
Subject to technical changes
Shipment and on-site transport
4
Shipment and on-site transport
The work described in this chapter may only be performed by
specialist personnel quali
fi
ed to perform the corresponding task.
Damage to the valve due to improper transport and storage!
Ö
Valves with lining must be handled, transported and stored
with care.
4.1 Accepting
delivery
Perform the following steps after receiving the goods:
Ö
Check the scope of supply. Compare the delivered goods
with the delivery note.
Ö
Check the supply for transport damage. Report transport
damage to PFEIFFER and the transport company (see the de-
livery note).
4.2 Unpacking the valve
Damage to the plastic lining!
Protect the lined valve surfaces in particular prior to/during in-
stallation.
Ö
Transport the valve in its original packaging to the installation
site and unpack it only there.
Perform the following steps before lifting and installing the valve:
Ö
Unpack the valve.
Ö
Dispose of the packaging properly.
Damage to the valve due to the ingress of foreign matter!
The protective caps on the valve inlet and outlet prevent foreign
matter from entering the valve and damaging it. Only remove the
protective caps prior to installation in the pipe.
4.3 Transporting and lifting the valve
Danger due to falling of suspended loads!
Do not stand under suspended loads.
NOTE
NOTE
NOTE
DANGER
Overturning of the lifting equipment and damage to the load
lifting equipment by exceeding the lifting capacity!
Ö
Only used approved lifting equipment and load lifting equip-
ment whose lifting capacity corresponds at least to the weight
of the valve including the actuator.
Ö
Take the weights from the respective data sheet.
Danger of injury due to the tipping of the valve!
Ö
Observe the centre of gravity of the valve.
Ö
Secure the valve against tipping and twisting.
Damage to the valve due to improper fastening of the sling!
The welded-on lifting eyes on SAMSON actuators are used only
for actuator assembling and disassembling as well as for lifting
the actuator without the valve. This lifting eye is not intended for
lifting the complete valve.
Ö
When lifting the valve, make sure that the entire load is car-
ried by the sling that is fastened to the valve body.
Ö
Do not fasten the load-bearing sling to the actuator, hand
wheel or other components.
Ö
Do not use the control air lines, accessories or other compo-
nents with safety functions for suspension or damage them.
4.3.1 Transporting
The valve can be transported using lifting equipment such as a
crane or a forklift.
Ö
Leave the valve on the pallet or in the transport container for
transport.
Ö
Valves that weigh more than approx. 10 kg should be trans-
ported on a pallet (or supported similarly) (also to the instal-
lation site). The packaging should protect the scratch-sensitive
plastic lining of the valve against damage.
Ö
Comply with the transport conditions.
Transport conditions
Ö
Protect the valve against external in
fl
uences, such as impacts.
Ö
Do not damage the corrosion protection (paint, surface coat-
ing). Repair damage immediately.
Ö
Protect the valve against moisture and dirt.
4.3.2 Lifting
When installing the valve in the pipe, heavier valves can be lift-
ing using lifting equipment such as a crane or forklift.
WARNING
NOTE
Summary of Contents for EB 01b
Page 28: ...5 6 EB 01b_EN February 2022 edition Subject to technical changes Installation...
Page 30: ...6 2 EB 01b_EN February 2022 edition Subject to technical changes Start up...
Page 32: ...7 2 EB 01b_EN February 2022 edition Subject to technical changes Operation...
Page 36: ...8 4 EB 01b_EN February 2022 edition Subject to technical changes Malfunction...
Page 40: ...10 2 EB 01b_EN February 2022 edition Subject to technical changes Decommissioning...
Page 42: ...11 2 EB 01b_EN February 2022 edition Subject to technical changes Removal...
Page 48: ...13 2 EB 01b_EN February 2022 edition Subject to technical changes Disposal...
Page 50: ...14 2 EB 01b_EN February 2022 edition Subject to technical changes Certificates...
Page 51: ...14 3 EB 01b_EN February 2022 edition Subject to technical changes Certificates...
Page 52: ...14 4 EB 01b_EN February 2022 edition Subject to technical changes Certificates...
Page 53: ...14 5 EB 01b_EN February 2022 edition Subject to technical changes Certificates...
Page 54: ...14 6 EB 01b_EN February 2022 edition Subject to technical changes Certificates...
Page 61: ...EB 01b_EN February 2022 edition Subject to technical changes...
Page 62: ...EB 01b_EN February 2022 edition Subject to technical changes...
Page 63: ...EB 01b_EN February 2022 edition Subject to technical changes...