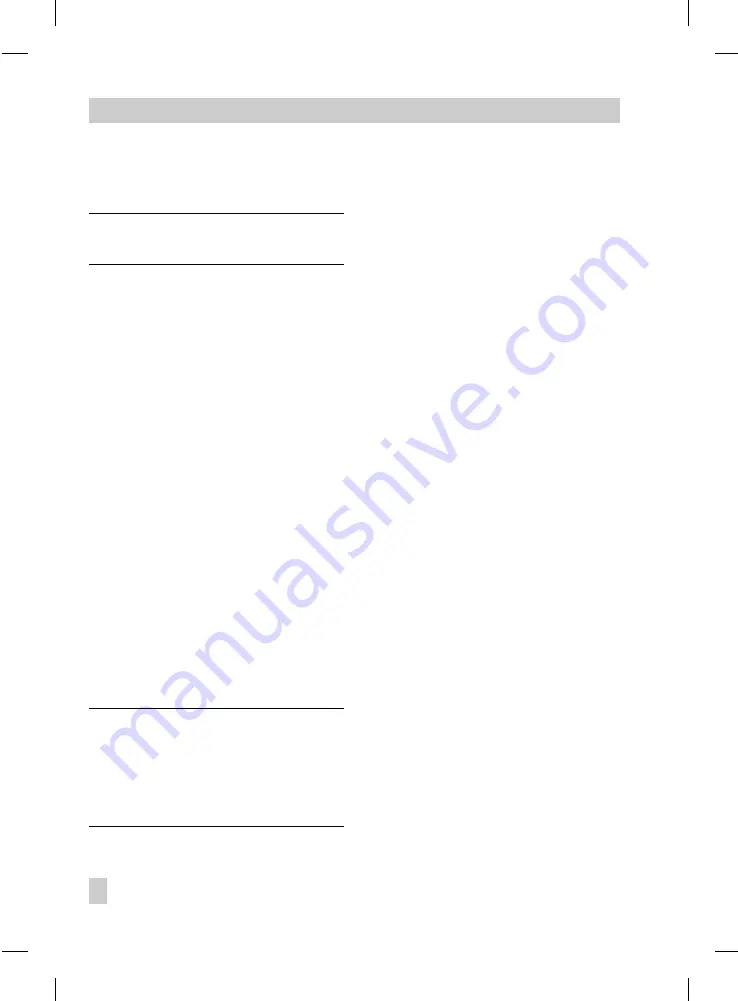
2.2 Attachment according to
IEC 60534-6
For selection of the required mounting
parts, refer to Tables 4 and 5 on page 19.
For positioner attachment according to
NAMUR as shown in Fig. 4, an adapter
housing is required. The valve travel is trans-
mitted via the lever (18) and the shaft (25)
to the bracket (28) of the adapter housing
and then to the pin (27) located at the posi-
tioner lever.
To attach the positioner, the mounting parts
listed in Table 4 are required. Which lever is
to be used depends on the rated valve travel.
The positioner must be attached with the
arrow
on the black case cover pointing
away
from the
diaphragm actuator
to-
wards the valve.
Exception:
Control valves in which the plug
only closes the seat area when the actuator
stem retracts. In this case, the arrow has to
point towards the diaphragm actuator.
If the adapter housing cannot be mounted
between
the actuator and the valve (e.g. ac-
tuators by other manufacturers), the
arrow
on the case cover must point
towards
the
control valve.
2.2.1 Mounting sequence
Note!
Before you mount the parts, apply a signal
pressure to the actuator so that the valve is
set to 50 % of its travel. This will ensure the
exact alignment of the lever (18) and the
bracket (28).
Control valve with casted yoke
1. Use countersunk screw to attach the
plate (20) to the coupling which con-
nects the plug and actuator stems. With
2100 and 2800 cm
2
actuators, use ad-
ditional mounting bracket (32).
2. Remove rubber plug from the adapter
housing and fasten the housing to the
NAMUR rib using the hexagon head
screw.
Control valve with rod-type yoke
1. Screw plate (20) to the follower clamp
of the plug stem.
2. Screw studs (29) into the adapter
housing.
3. Place the housing with the plate (30) on
either the right or the left side of the
valve rod and screw the housing tight
using nuts (31). Be sure to align the
housing in such a way that the lever to
be mounted subsequently is in a hori-
zontal position.
4. Move the clamp (21) to surround the
pin (19). Screw pin into the center row
of bores in the plate (20) and lock it
such that it will be located above the
correct lever marking (1 to 2) for the as-
signed travel (see Table 5).
Intermediate values must be calculated.
5. Measure the distance between the cen-
ter of the shaft (25) and the center of
the pin (19). You will be prompted for
this value later during the configuration
of the positioner.
16
EB 8382-2 EN
Attaching the positioner
Summary of Contents for 4785
Page 73: ...EB 8382 2 EN 73...
Page 74: ...74 EB 8382 2 EN...
Page 75: ...EB 8382 2 EN 75...
Page 76: ...76 EB 8382 2 EN...
Page 77: ...EB 8382 2 EN 77...