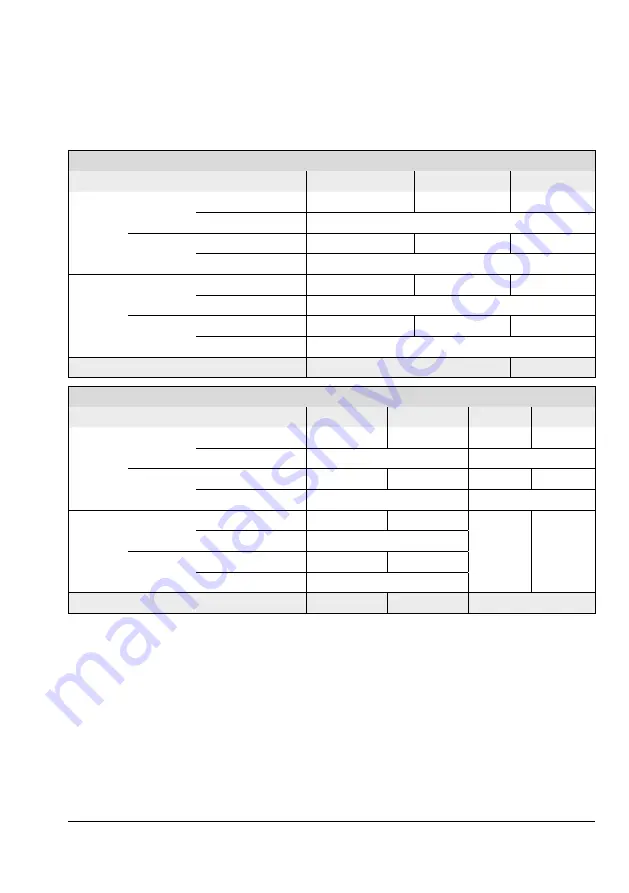
EB 2626-1 EN
3-7
Design and principle of operation
Table 3-3:
K
VS
coefficients and xFZ values · Terms for noise level calculation according to
VDMA 24422 (edition 1.89)
Body with screwed ends
Connection size
G ½ · ½ NPT
G ¾ · ¾ NPT
G 1 · 1 NPT
K
VS
Type 44-1 B
Standard version
3.2
1)
4.0
1)
5.0
1)
Special version
0.25
3) 4)
· 1.0
1) 3) 4)
· 2.5
3) 4)
Type 44-0 B
Standard version
1.6
2) 3)
· 3.2
4)
2.0
2) 3)
· 4.0
4)
2.5
2) 3)
· 5.0
4)
Special version
1.0
2) 3)
C
V
Type 44-1 B
Standard version
4.0
1)
5.0
1)
6.0
1)
Special version
0.3
3) 4)
· 1.2
1) 3) 4)
· 3.0
3) 4)
Type 44-0 B
Standard version
1.9
2) 3)
· 4.0
4)
2.4
2) 3)
· 5.0
4)
2.9
2) 3)
· 6.0
4)
Special version
1.2
2) 3)
x
Fz
values
0.60
0.55
Flanged body
Valve size
DN 15/NPS ½
DN 25/NPS 1
DN 40
DN 50
K
VS
Type 44-1 B
Standard version
3.2
1)
5.0
1)
16.0
20.0
Special version
0.25
3) 4)
· 1.0
1) 3) 4)
· 2.5
3) 4)
8.0
2) 3)
Type 44-0 B
Standard version
1.6
2) 3)
· 3.2
4)
2.5
2) 3)
· 5.0
4)
16.0
4)
20.0
4)
Special version
1.0
2) 3)
8.0
2) 3)
C
V
Type 44-1 B
Standard version
4.0
1)
6.0
1)
–
–
Special version
0.3
3) 4)
· 1.2
1) 3) 4)
· 3.0
3) 4)
Type 44-0 B
Standard version
1.9
2) 3)
· 4.0
4)
2.9
2) 3)
· 6.0
4)
Special version
1.2
2) 3)
x
Fz
values
0.60
0.55
0.40
1)
Also available as special version for regulators with stainless steel body and FFKM soft seal
2)
Metal seal
3)
Unbalanced
4)
Soft seal. Seal material: EPDM or FKM. Additionally Type 44-6 B: PTFE gasket material
Summary of Contents for 44-0 B
Page 12: ...1 8 EB 2626 1 EN Safety instructions and measures...
Page 24: ...3 10 EB 2626 1 EN Design and principle of operation...
Page 36: ...7 2 EB 2626 1 EN Operation...
Page 40: ...8 4 EB 2626 1 EN Malfunctions...
Page 50: ...11 2 EB 2626 1 EN Removal...
Page 52: ...12 2 EB 2626 1 EN Repairs...
Page 54: ...13 2 EB 2626 1 EN Disposal...
Page 56: ...14 2 EB 2626 1 EN Certificates 1...
Page 57: ...EB 2626 1 EN 14 3 Certificates...
Page 58: ...14 4 EB 2626 1 EN Certificates 2 3...
Page 62: ...15 4 EB 2626 1 EN Annex...
Page 63: ......
Page 64: ......
Page 65: ......