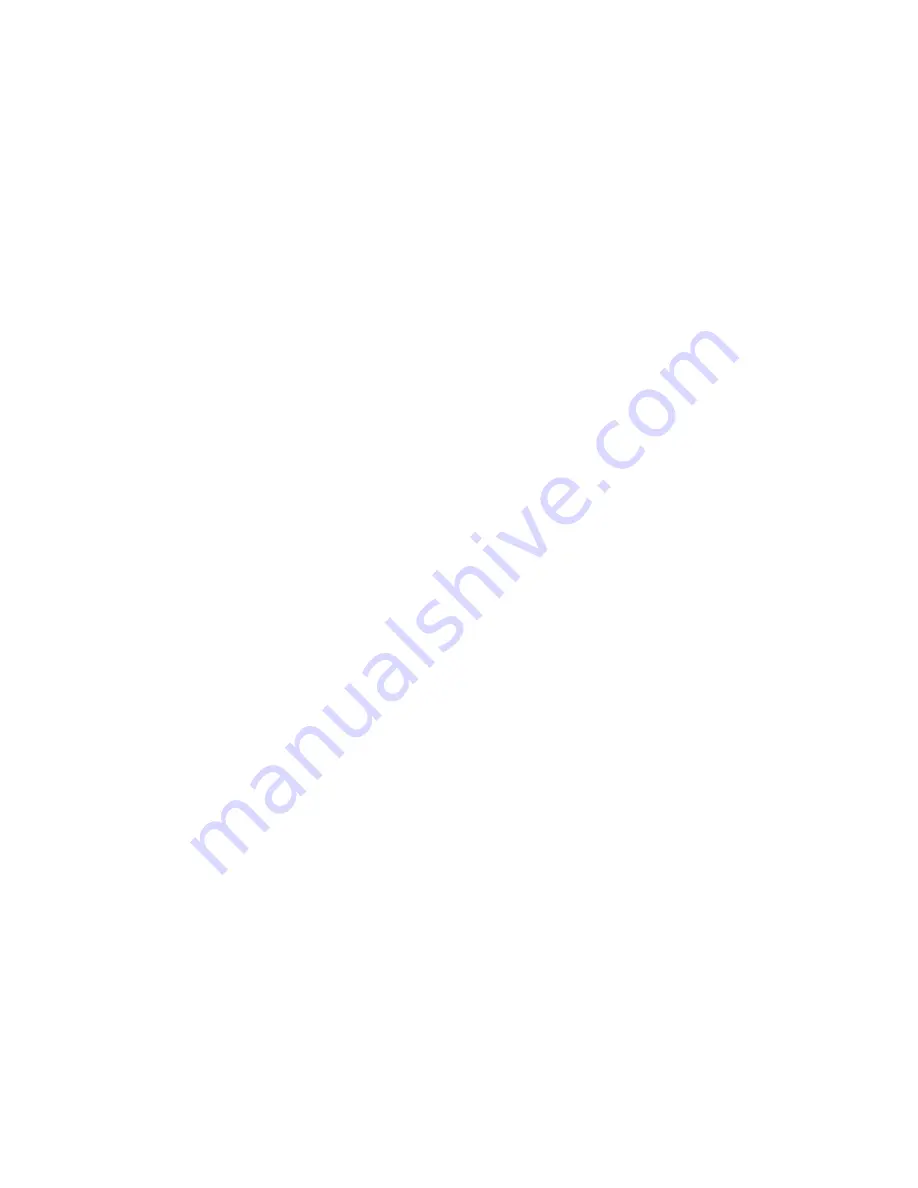
Page C - 1
APPENDIX C: DETERMINING PROPER SPAN GAIN (F2)
C.1
SPAN GAIN OVERVIEW
The Span Gain parameter found in F2 of the Setup Menu is directly related to the ADC
(Analog to Digital Converter) integration time. This means that the lower the setting, the
higher the number of measurements per second. A span gain setting of
25
produces about
25 to 30 measurements per second, while a span gain of
200
produces only about 3 or 4
measurements per second.
There is really no wrong setting for span gain – except in two cases. Using a low setting for
a high resolution, low output system could yield instability. Using a high setting in a high
output system could yield non-linearity.
C.2
SETTING THE INITIAL VALUE FOR SPAN GAIN
1. Determine the number of desired external graduations and choose the corresponding
value listed in Table C-1 under the number closest to your full-scale input range in
millivolts.
2. Enter the Setup Menu and save this number for the Span Gain parameter in F2.
3. Perform a system calibration. If the calibration proves unsuccessful, or you wish to view
the internal counts, proceed to the next set of instructions.
C.3
VIEWING THE INTERNAL COUNTS
1. Enter the zero calibration menu (F16) and follow steps 1 to 3,
but do not save the zero
point.
2. After pressing
ZERO
to zero the offset, place the test weight(s) on the platform. The
displayed count is the internal count. If the count remains on zero, check your load cell
connections.
3. At full scale, the displayed count should be a minimum of 2 times the desired external
graduations. However, for maximum stability, a ratio of 6:1 or higher is recommended.
4. If the displayed count is large enough, remove the test weight(s), re-zero the indicator if
necessary, and proceed with the calibration. If the displayed number is
not
large
enough, increase the Span Gain to the next highest choice in the Setup Menu and re-
calibrate.