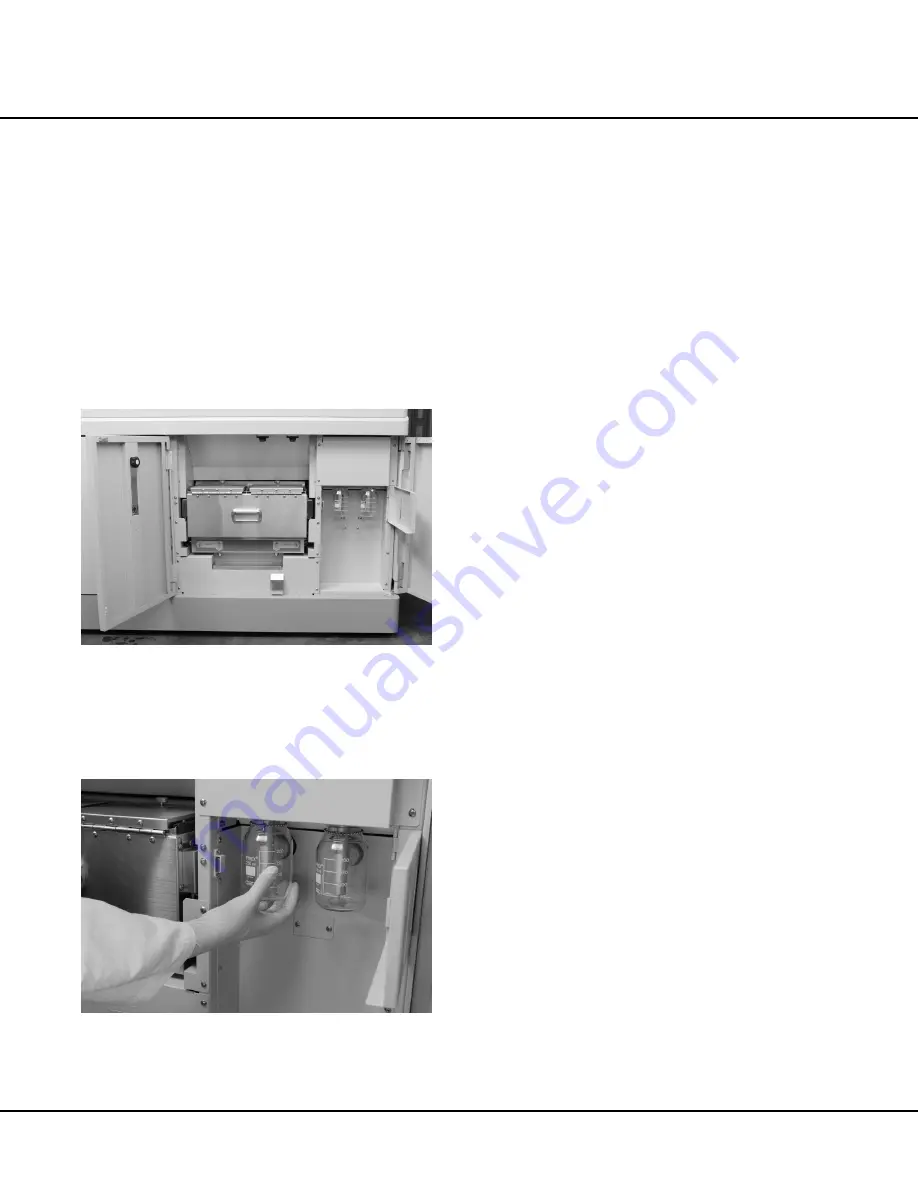
Revised 10/02/2012
7.3
Overflow Bottle Cleaning
The overflow bottles associated with Retort #3 and #4
serve as overflow receptacles in the event excess reagent
(paraffin) is pumped into the associated retort. The
overflow bottles should be cleaned as needed to remove
any accumulated paraffin.
WARNING: THE OVERFLOW BOTTLES MAY CONTAIN
BIOHAZARDOUS WASTE. DISPOSE OF CONTENTS IN
ACCORDANCE WITH LOCAL REGULATIONS.
To clean the overflow bottles:
1.
Open the Overflow Bottles Access Door (Figure 7-A).
Figure 7-A
2.
Loosen each overflow bottle by turning to the left, and
remove the overflow bottles from the overflow bottle
cabinet (Figure 7-B).
Figure 7-B
3.
Discard accumulated paraffin in the overflow bottles
in accordance with local regulations for biohazardous
waste.
4.
Clean any paraffin residue in overflow bottles using
hot, soapy water, then rinse and wipe dry.
NOTE: The overflow bottles are labeled “#3” and “#4” to
ensure reinstallation in the correct locations in the
overflow bottle cabinet.
5.
Reinstall the overflow bottles in the overflow bottle
cabinet. Be sure to match the labels on the overflow
bottles with the labels on the overflow bottle cabinet
to ensure installation in the proper locations.
6.
Tighten each overflow bottle by turning to the right.
7.
Close the Overflow Bottle Access Door.
Pre-Processing Solution
Replacement
Onboard Pre-Processing Solution must be replaced on
condition (after a specified number of hours) to ensure
proper preprocessing. The instrument con be configured
to count the number of hours the solution has been in the
instrument to aid in determining when to replace the Pre-
Processing Solution (See “System Operation”, page 4.5).
NOTE: Depending on the types of tissues processed the
Pre-Processing Solution should be replaced every 3
hours.
To replace the Pre-Processing Solution:
WARNING: THE PREPROCESSING CONTAINER MAY
CONTAIN BIOHAZARDOUS WASTE. DISPOSE OF
THE CONTENTS IN ACCORDENCE WITH LOCAL
REGULATIONS.
1.
Open the Loading Station Door.
2.
Remove the Loading Station Container.
3.
Discard the Pre-Processing Solution per local
regulations.
4.
Wipe the inside of the loading station container with
gauze.
5.
Fill the Loading Station Container with 1.2L of Pre-
Processing Solution.
6.
Place the Loading Station Container inside the
instrument.
7.
Close the Loading Station Door.
Summary of Contents for Tissue-Tek Xpress x120
Page 1: ...Operating Operating Manual Manual Rapid Tissue Processor Tissue Tek Xpress x120 ...
Page 3: ......
Page 20: ...INTRODUCTION 1 14 Revised 10 02 2012 ...
Page 24: ...INSTALLATION 2 4 Revised 10 02 2012 ...
Page 54: ...RECOVERY PROCESS 5 4 Revised 10 02 2012 ...
Page 82: ...A 8 Revised 10 02 2012 ...