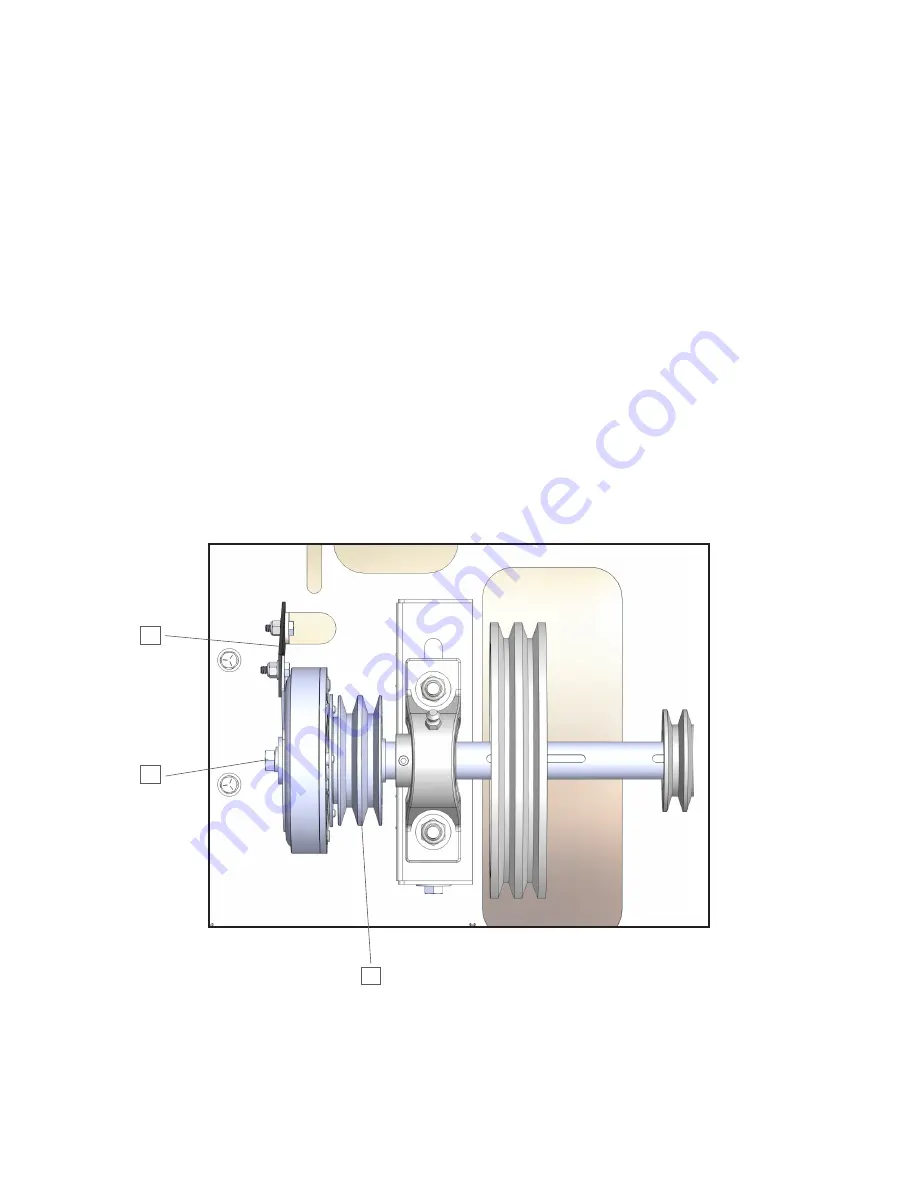
28
ELECTRO-MAGNETIC CLUTCH
The electro-magnetic clutch has no scheduled wear replacement parts and can only be replaced whenever
field failures may occur. Refer to the following drawing and detailed instructions for removing the clutch from
the shaft.
1.
Disconnect wiring at clutch connector.
2.
Remove torque arm attach bolt from clutch arm.
3.
Remove drive belts from pulley. The pulley is part of the clutch assembly.
4.
Remove the attach bolt, washer, & lock washer.
5.
Slide clutch off clutch shaft. The use of a pry bar or similar device may be necessary to start clutch off shaft,
wedge between bearing housing and clutch hub. Make sure that bearing shaft seal or clutch bearing seal
does not get damaged.
6.
Inspect clutch drive key, replace as required.
Note: Upon reassembly, make sure to add two drops of blue Loctite to threads of attach bolt. Be careful not
to get Loctite on clutch shaft.
2
4
3
Summary of Contents for CertainTeed Volu-Matic 100
Page 12: ...12 Operation...
Page 20: ...20 Troubleshooting...
Page 23: ...23...
Page 24: ...24 Preventive Maintenance...
Page 30: ...30 Parts Drawings...
Page 31: ...31...