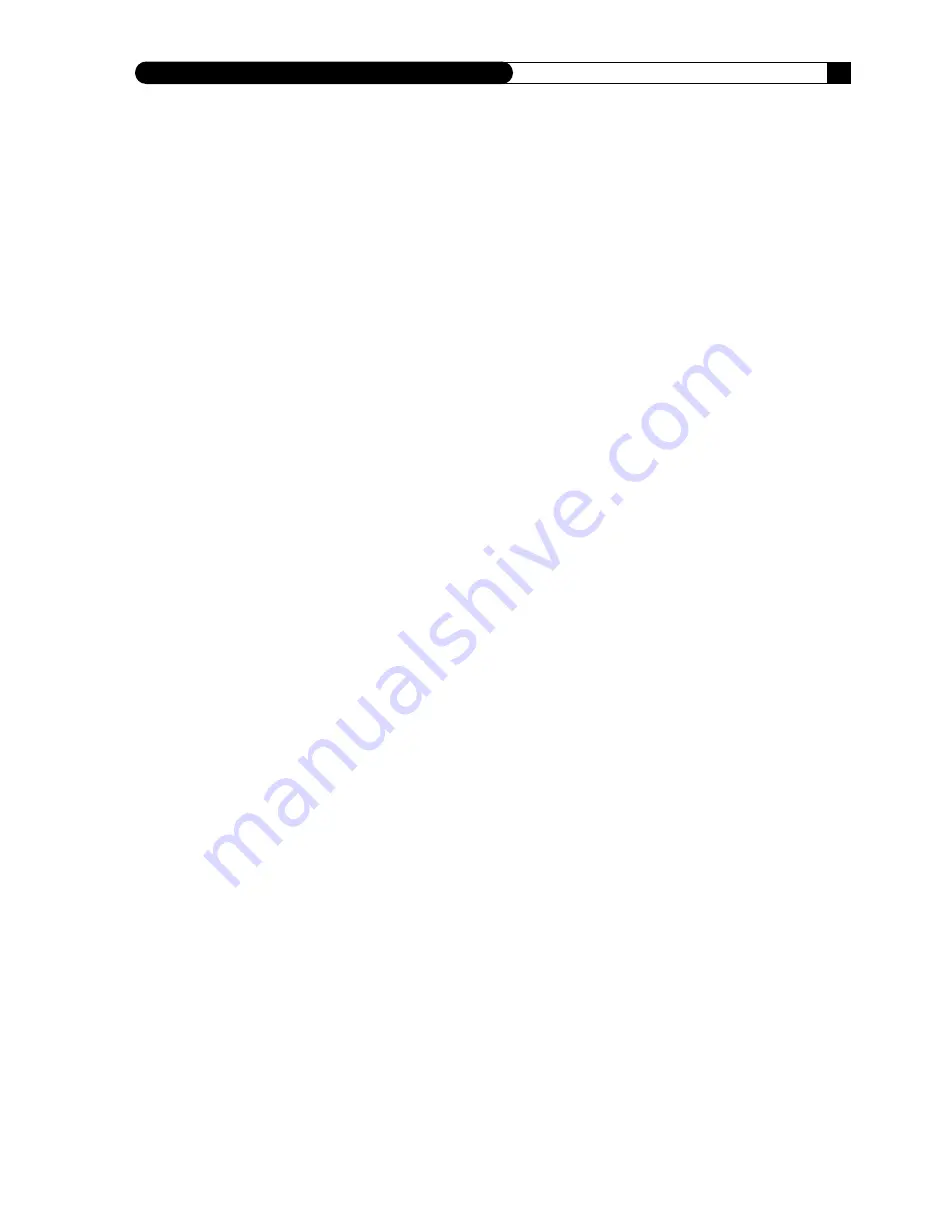
O p e r a t i o n s a n d I n s t r u c t i o n M a n u a l
UNPACKING YOUR SAGE METER
Your Sage flow meter is a sensitive, yet rugged,
precision built electronic instrument. Upon delivery,
care should be taken when opening the shipping
container and removing your meter. The meter
should be inspected for any damage that may have
occurred during transit. If damage is found, please
contact the carrier immediately to place a claim for
damaged goods. The contents of the container
should be checked against the packing list for any
discrepancies. If there are any questions as to the
contents or configuration of the equipment includ-
ing calibration ranges, or, mounting hardware,
contact Sage Metering as soon as possible. Please
save shipping container and packaging materials
(including PVC tube probe protector on Sage
Insertion Flow Meters) in case the unit needs to
be returned for any reason.
MAINTENANCE
Sage thermal mass flow meters essentially require
little or no maintenance. While the sensing element
is somewhat resistant to dirt and particulate build
up, it may become necessary to clean it from time to
time if mounted in extremely dirty environments.
NOTE: ALWAYS DISABLE THE TRANSMITTER
POWER SUPPLY PRIOR TO ANY CLEANING OR
MAINTENANCE. A detergent or appropriate
non-corrosive solvent for removing the buildup
may be required. A soft brush can be used to gently
clean the sensing element’s surface, using caution
to avoid damaging the sensor elements (the RTDs).
If any disassembly is necessary, contact Sage
Metering, Inc. for instructions.
In general, it is
recommended that your Sage Thermal Mass Flow
Meter be returned to the factory if cleaning,
repair, or recalibration is needed. This is usually
the most cost-effective and reliable alternative.
CALIBRATION
Sage thermal mass flow meters have built-in diag -
nostics. The menuing system (see Section D) has
provisions to check the sensor’s operation by ac cess -
ing the sensor’s output and comparing it to the origi -
nal reported “zero flow” value noted on the last few
lines of your meter’s Certificate of Conformance.
This diagnostic procedure not only checks the sensor
performance and the "live zero" calibration point,
but it verifies that the sensor is clean. It essentially
provides a means to validate the meter's perform-
ance, verifies that there is no shift or drift, and elimi-
nates the need for annual factory calibrations. See
“Sensor Functionality and Zero Calibration Self
Check” on page 42.
Getting Started
9
S A G E M E T E R I N G , I N C .
REV. 03-SIE/SRE
a
CAUTION Cable glands shipped with unit are for shipping purposes only.
Remove shipping cable glands before installing.
a
CAUTION If installing in a Class I hazardous location the installation
must comply with appropriate electrical codes (CSA units per CEC Part 1
Appendix J18-100).
a
CAUTION Installer must supply proper ground and bond wire for the
transmitter and the sensor per appropriate electrical codes (CSA units per
CEC Part 1).
Summary of Contents for SIE Series
Page 2: ......
Page 6: ......
Page 7: ...Section GETTING STARTED A ...
Page 8: ......
Page 23: ...Section STYLES AND FEATURES B ...
Page 24: ......
Page 28: ......
Page 29: ...Section DRAWINGS C ...
Page 30: ......
Page 39: ...Section USER INTERFACE D ...
Page 40: ......
Page 58: ......
Page 59: ...Section DIAGNOSTICS E ...
Page 60: ......
Page 63: ...Section WARRANTIES AND SERVICE WORK F ...
Page 64: ......
Page 69: ...G Section APPENDIX G ...
Page 70: ......