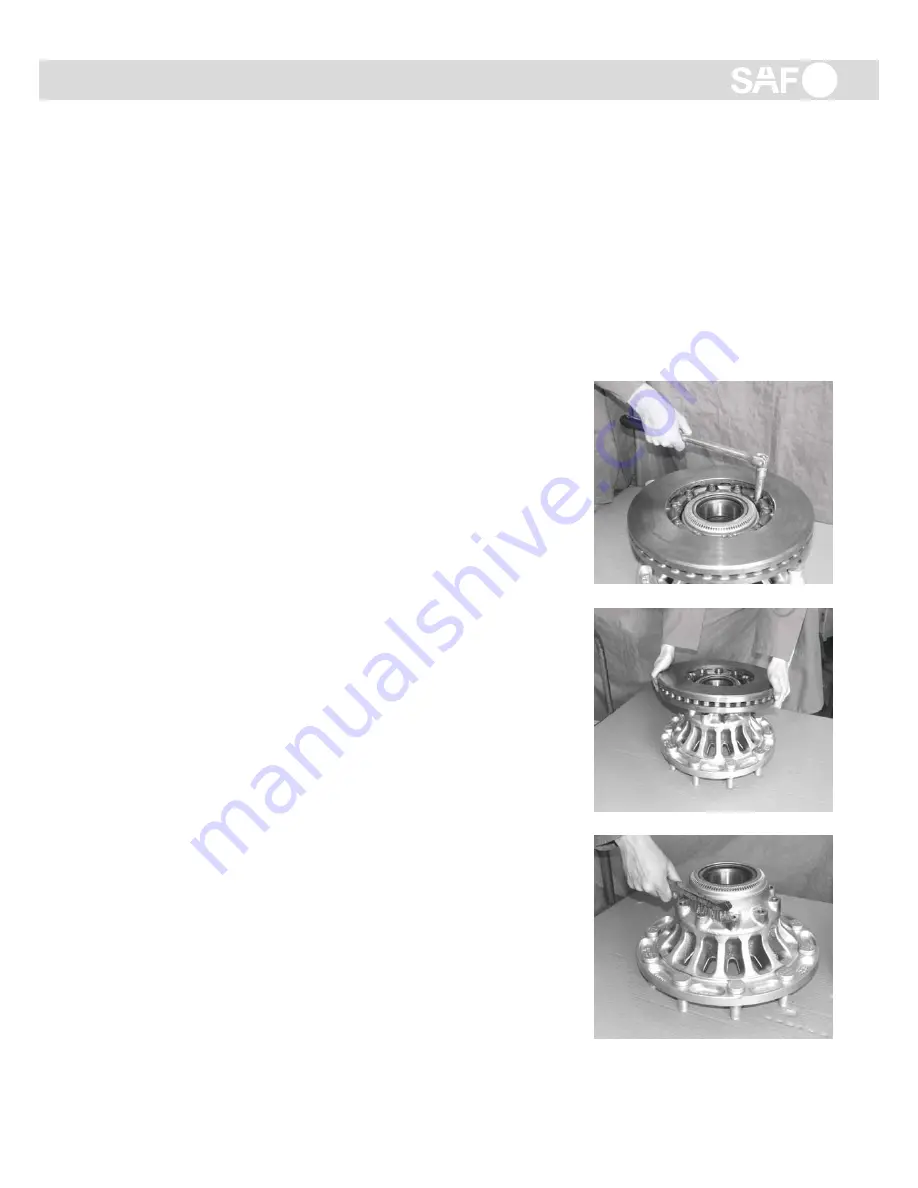
SK RB/RLB 9022WI with WABCO PAN 22-1
11.427GB Edition 11/09
-
21
-
3.0
Replace the Brake Disc on the Hub Unit SK RB INTEGRAL
3.1
Remove and install brake pads from brake calliper.
3.2
Remove and install brake cylinder from brake calliper.
3.3
Remove and install brake calliper from brake carrier.
3.4
Remove and install wheel cap.
3.5
Remove and install axle nut.
3.6
Pull hub unit SK RB
INTEGRAL
complete with brake
disc from the stub axle and place to one side.
See installation instructions, chapter 1
See installation instructions, chapter 2
3.7
Loosen and remove the DSK bolts holding the brake disc.
Torque wrench settings see page 7
3.8
Remove the brake disc from hub unit SK RB
INTEGRAL
.
3.9
Clean the contact surfaces for the brake disc on the hub unit SK RB
INTEGRAL
.
Blow out the tapped bores for the DSK bolts with compressed air.
Check the thread for easy bolt insertion.
Installation instructions