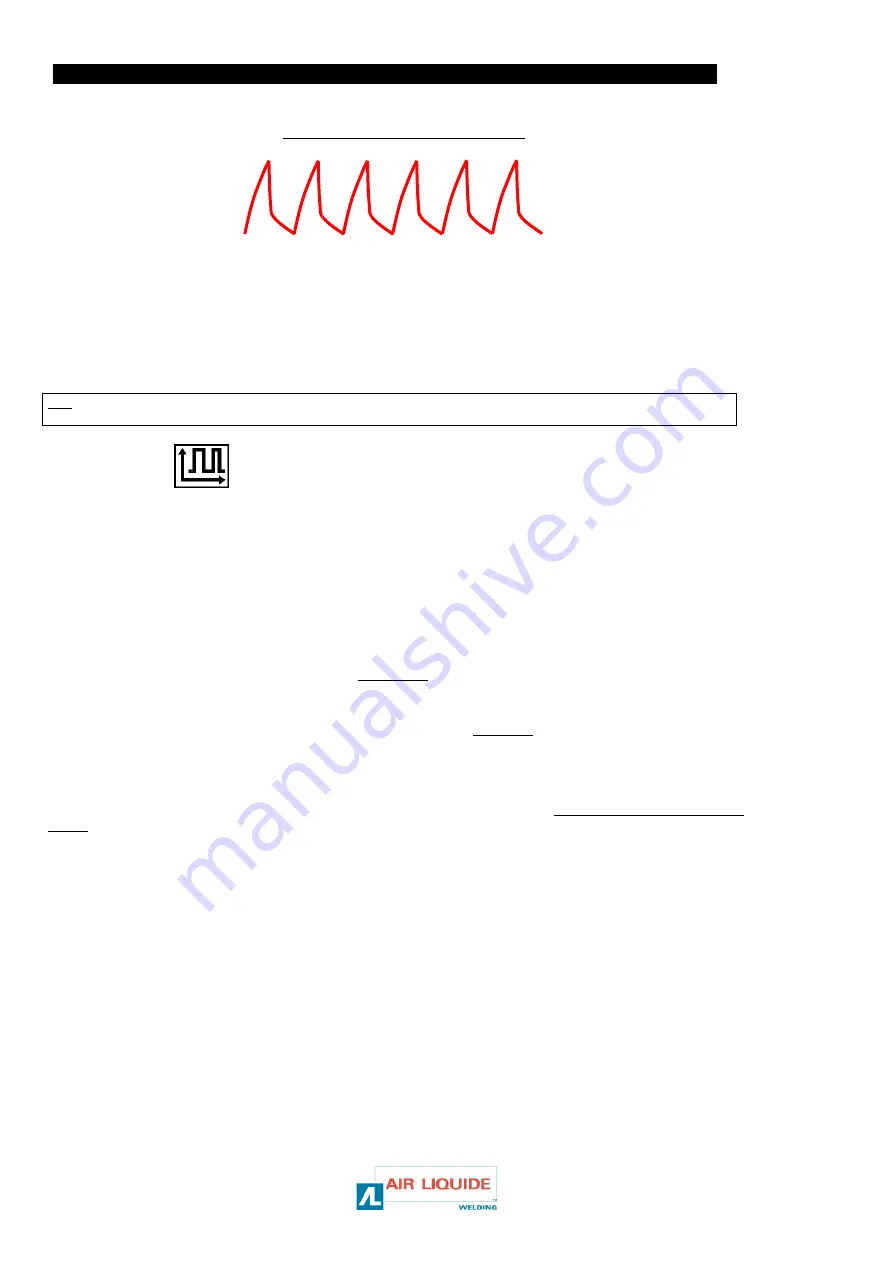
24
/
28
Waveform of speed short arc welding process
By eliminating the "globular" arc mode, which is characterized by heavy and sticky spatter and higher energy than the short a
speed short arc enables to:
Reduce the amount of distortions at high welding currents in the typical "globular" welding range
Reduce the amount of spatter compared to the globular mode
Achieve good weld appearance
reduce smoke emissions compared with the usual modes (up to 25% less)
Achieve good rounded penetration
Enable welding in all positions
Note
: The CO
2
programmes automatically and exclusively use
The “dynamic” short arc is not suitable for CO
2
, welding due to arc
NORMAL Pulsed MIG
Metal transfer in the arc takes place by detachment of droplets caused by current pulses. The microprocessor calculates all t
parameters for each wire speed, to ensure superior welding and striking results.
The advantages of pulsed Mig are :
☞
Reduced distortions at high welding currents in the customary "globular" welding and spray arc ranges
☞
Enables all welding positions
☞
Excellent fusion of stainless steel and aluminium wires
☞
Almost complete elimination of spatter and hence of finishing work
☞
good bead appearance
☞
Reduced smoke emissions compared with customary methods and even
Pulsed
DIGISTEEL III 320C / DIGIPULS III 320C
programs
low wire feed speeds. These "balls" are caused by slight spraying of the metal at the time of droplet detachment. The extent
phenomenon depends on the type and origin of the wires.
These programmes for stainless steel have undergone improvements for operation at
sheet welding using Pulsed MIG method.
Excellent results for welding thin stainless steel sheets (1 mm) are obt
Noxalic-12 shield (average 30A is acceptable).
The appearance of joints processed using,
DIGISTEEL III 320C / DIGIPULS III 320C
welding.
DIGISTEEL
III
320C
Waveform of speed short arc welding process
By eliminating the "globular" arc mode, which is characterized by heavy and sticky spatter and higher energy than the short a
distortions at high welding currents in the typical "globular" welding range
Reduce the amount of spatter compared to the globular mode
reduce smoke emissions compared with the usual modes (up to 25% less)
programmes automatically and exclusively use the “soft” short arc and do not enable access to the speed short arc.
due to arc instability.
Metal transfer in the arc takes place by detachment of droplets caused by current pulses. The microprocessor calculates all t
parameters for each wire speed, to ensure superior welding and striking results.
Reduced distortions at high welding currents in the customary "globular" welding and spray arc ranges
Excellent fusion of stainless steel and aluminium wires
elimination of spatter and hence of finishing work
Reduced smoke emissions compared with customary methods and even-speed short-arc (up to 50% less);
programs for stainless steel eliminate the small spatter that may occur on thin sheets at very
low wire feed speeds. These "balls" are caused by slight spraying of the metal at the time of droplet detachment. The extent
phenomenon depends on the type and origin of the wires.
These programmes for stainless steel have undergone improvements for operation at low currents and increasing the flexibility of use for thin
Excellent results for welding thin stainless steel sheets (1 mm) are obtained using the pulsed MIG method with Ø 1 mm wire in Arcal
DIGISTEEL III 320C / DIGIPULS III 320C
is of a quality comparable with that achieved by TIG
EN
320C
/
DIGIPULS
III
320C
By eliminating the "globular" arc mode, which is characterized by heavy and sticky spatter and higher energy than the short arc, the
the “soft” short arc and do not enable access to the speed short arc.
Metal transfer in the arc takes place by detachment of droplets caused by current pulses. The microprocessor calculates all the Pulsed MIG
eliminate the small spatter that may occur on thin sheets at very
low wire feed speeds. These "balls" are caused by slight spraying of the metal at the time of droplet detachment. The extent of this
and increasing the flexibility of use for thin
ained using the pulsed MIG method with Ø 1 mm wire in Arcal-12 or
comparable with that achieved by TIG
Summary of Contents for DIGISTEEL III 320C
Page 16: ...16 28 DIGISTEEL III 320C EN 320C DIGIPULS III 320C...
Page 17: ...DIGISTEEL III 320C DIGIPULS III 320C Internal and inverter 320C EN 17 28...
Page 18: ...18 28 Front and rear DIGISTEEL III 320C EN 320C DIGIPULS III 320C...
Page 22: ...22 28 5 7 ELECTRICAL DIAGRAM EN DIGISTEEL III 320C DIGIPULS III 320C...