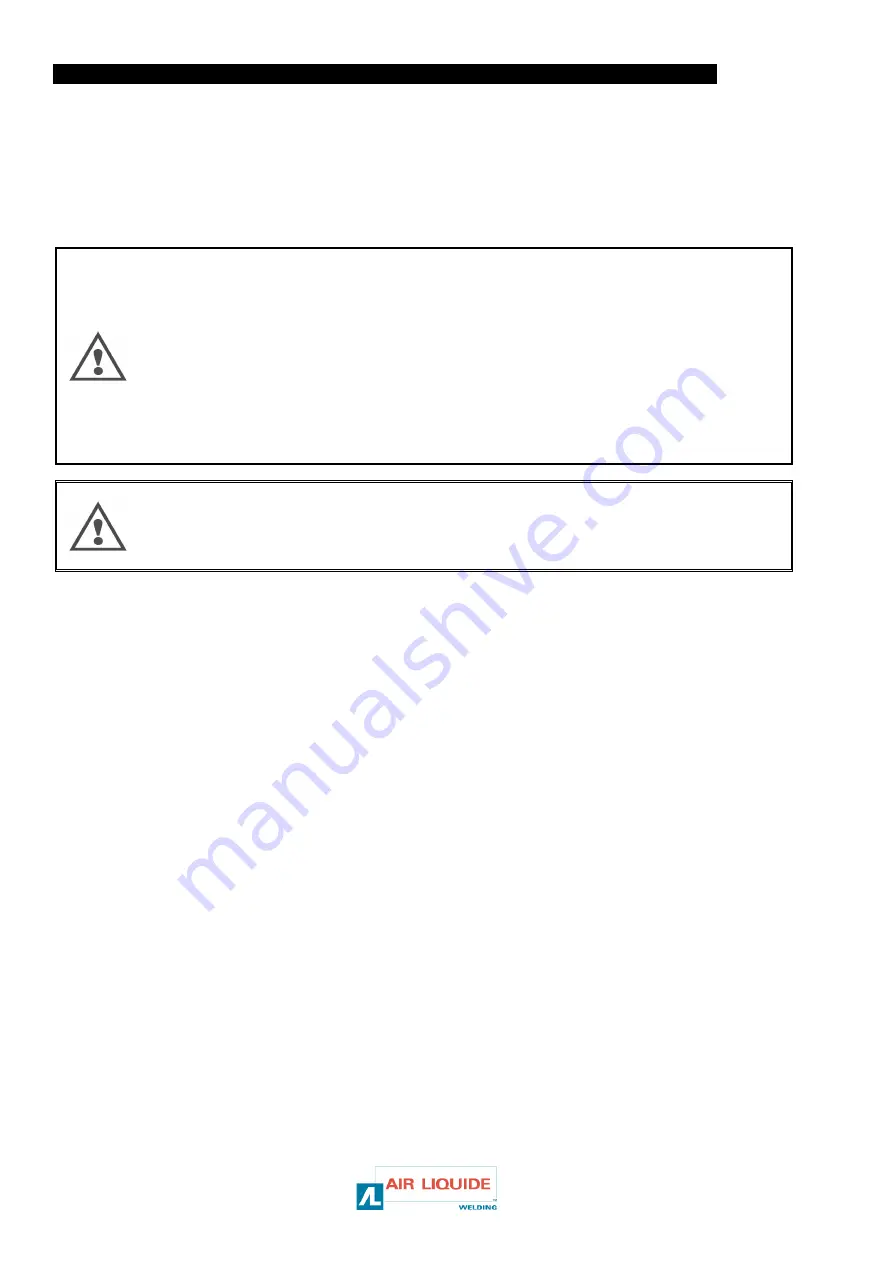
14
/
28
5 - MAINTENANCE
5.1. GENERAL
Twice a year, depending on the use of the device, inspect the
cleanliness of the pwer source
electrical and gas connections
WARNING :
Never carry out cleaning or repair work inside the device before making sure that the unit has been completely disconnected f
the mains.
Dismantle the generator panels and use suction to remove dust and metal particles accumulated between the magnetic circuits
and the windings of the transformer.
Work must be performed using a plastic tip to avoid damage to the insultation of the windings.
At each start-up of the welding unit and prior to calling customer c
Power terminals are not improperly tightened.
The selected mains voltage is correct.
There is proper gas flow.
Type and diameter of the wire.Torc
TWICE PER YEAR
Perform calibration of the current and voltage settings.
Check electrical connections of the power, control and power supply circuits.
Check the condition of insulation, cables, connections and pipes
Perform a compressed air cleaning
5.2. ROLLERS AND WIRE GUIDE
Under normal conditions of use, these accessories have a long serviceable life before their replacement becomes necessary.
Sometimes, however, after being used over a period of time, excessive wear
To minimise such harmful effects, make sure the wire feeder plate remains clean
The motor reduction unit requires no maintenance.
5.3. TORCH
Regularly check the proper tightness of the connections of
some parts of the torch, particularly:
The contact tube
The coaxial cable
The welding nozzle
The quick connector
Check that the gasket of the gas inlet spigot is in good condition
Remove the spatter between the contact tube and the nozzle and between the nozzle and the skirt.
Spatter is easier to remove if the procedure is repeated at short intervals.
Do not use hard tools that may scratch the surface of these
SPRAYMIG SIB, W000011093
SPRAYMIG H20, W000010001
Blow out the liner after each change of a spool of wire. Carry out this procedure from the side of the quick fitting connecto
If necessary, replace the wire inlet guide of the torch
Severe wear of the wire guide may cause gas leaks towards the rear of the torch.
The contact tubes are designed for long use. Nevertheless, the passage of wire causes them to wear off, widening the b
permissible tolerances for good contact between the tube and the wire
The need to replace them becomes clear when the metal transfer process becomes unstable, all the settings of the work paramet
otherwise normal.
DIGISTEEL
III
320C
Twice a year, depending on the use of the device, inspect the following:
Never carry out cleaning or repair work inside the device before making sure that the unit has been completely disconnected f
generator panels and use suction to remove dust and metal particles accumulated between the magnetic circuits
and the windings of the transformer.
Work must be performed using a plastic tip to avoid damage to the insultation of the windings.
ding unit and prior to calling customer cupport for technical servicing, please check that:
Power terminals are not improperly tightened.
The selected mains voltage is correct.
.Torch condition.
Perform calibration of the current and voltage settings.
Check electrical connections of the power, control and power supply circuits.
Check the condition of insulation, cables, connections and pipes.
air cleaning
Under normal conditions of use, these accessories have a long serviceable life before their replacement becomes necessary.
Sometimes, however, after being used over a period of time, excessive wear or clogging due to adhering deposits may be noted
To minimise such harmful effects, make sure the wire feeder plate remains clean.
.
Regularly check the proper tightness of the connections of the welding current supply. Mechanical stresses related to thermal shocks tend to loosen
in good condition.
Remove the spatter between the contact tube and the nozzle and between the nozzle and the skirt.
Spatter is easier to remove if the procedure is repeated at short intervals.
Do not use hard tools that may scratch the surface of these parts and cause spatter to become attached to it.
Blow out the liner after each change of a spool of wire. Carry out this procedure from the side of the quick fitting connecto
necessary, replace the wire inlet guide of the torch.
Severe wear of the wire guide may cause gas leaks towards the rear of the torch.
The contact tubes are designed for long use. Nevertheless, the passage of wire causes them to wear off, widening the b
permissible tolerances for good contact between the tube and the wire.
The need to replace them becomes clear when the metal transfer process becomes unstable, all the settings of the work paramet
EN
320C
/
DIGIPULS
III
320C
Never carry out cleaning or repair work inside the device before making sure that the unit has been completely disconnected from
generator panels and use suction to remove dust and metal particles accumulated between the magnetic circuits
upport for technical servicing, please check that:
Under normal conditions of use, these accessories have a long serviceable life before their replacement becomes necessary.
or clogging due to adhering deposits may be noted.
the welding current supply. Mechanical stresses related to thermal shocks tend to loosen
Blow out the liner after each change of a spool of wire. Carry out this procedure from the side of the quick fitting connector plug of the torch.
The contact tubes are designed for long use. Nevertheless, the passage of wire causes them to wear off, widening the bore more than the
The need to replace them becomes clear when the metal transfer process becomes unstable, all the settings of the work parameters remaining
Summary of Contents for DIGISTEEL III 320C
Page 16: ...16 28 DIGISTEEL III 320C EN 320C DIGIPULS III 320C...
Page 17: ...DIGISTEEL III 320C DIGIPULS III 320C Internal and inverter 320C EN 17 28...
Page 18: ...18 28 Front and rear DIGISTEEL III 320C EN 320C DIGIPULS III 320C...
Page 22: ...22 28 5 7 ELECTRICAL DIAGRAM EN DIGISTEEL III 320C DIGIPULS III 320C...