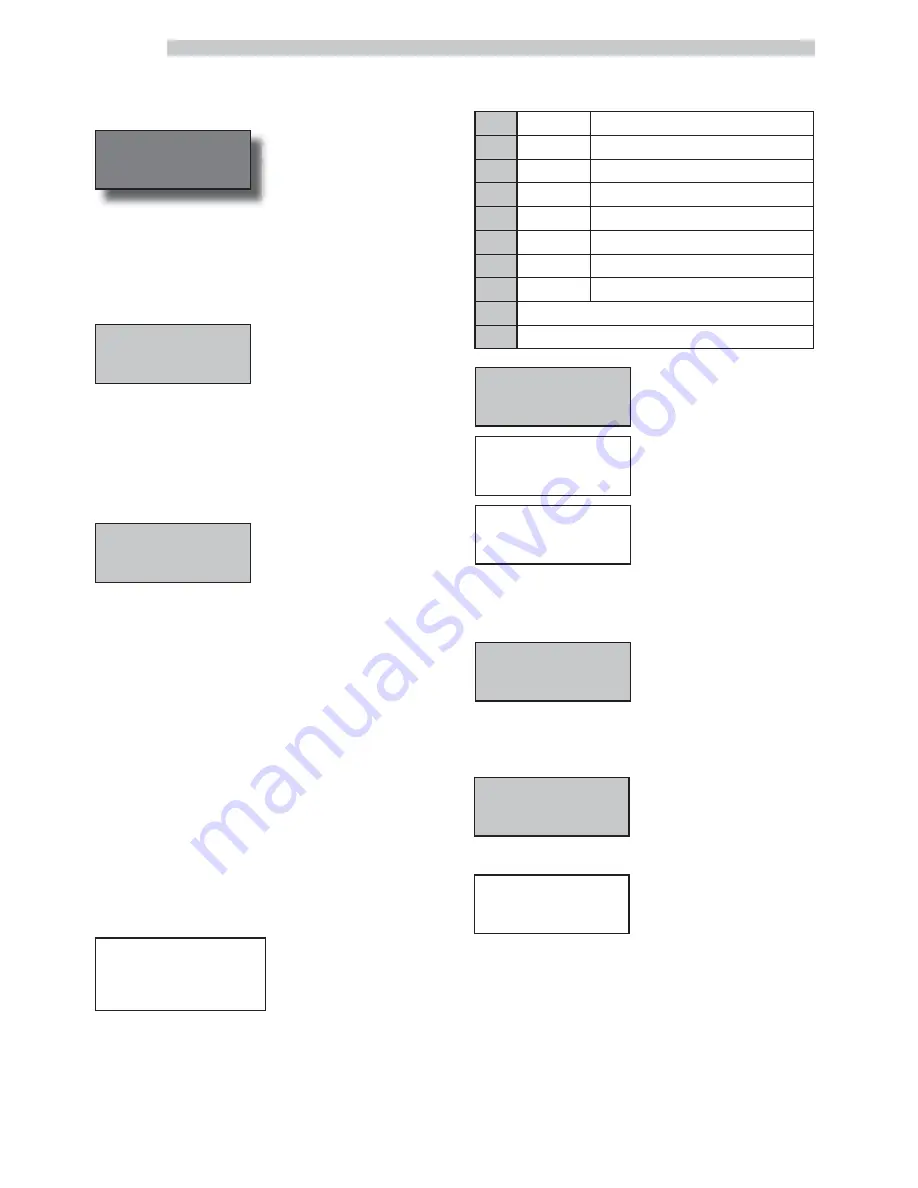
44
English
8.3.3
Description of messages in
the maintenance menu
MAINTENANCE
This function enables the
display and cancellation
of any errors that may be
present. It is also possible to
carry out maintenance on the vending machine.
To reset the errors, use the menu under the maintenance
item.
Error reset
This describes the current error
(check the cause in section
11.2 - Error messages). If no
error is present, this message
is not displayed.
After checking the error cause, press the ENTER key to reset
the vending machine (see section 11.2 for the complete list
of errors).
Error log
VM’s EEPROM records the
important events that occur in
the VMC (for example errors
that occurred, warning messages, etc.).
Recording takes place when the error condition is detected
and consists of saving the following information:
1- error code (or warning code) occurred;
2- location of signal source (e.g., which spiral motor, if the
error is due to a spiral motor, or which coffee or instant
product);
3- day, month, hour and minute of error detection (this
information is available only if the VM is equipped with
a timekeeper).
The recordings are included in a list which may contain
up to 50 elements; when this limit is exceeded the
information is input again starting from position 1
(previous information will be lost).
Note
All errors or faults are stored, except when blocks occur
(coffee, instant product, beverage, water).
Display:
1.1
ERROR LOG ii/NN
dd MMM hh:mm
Exx - aabb
M
Th
d
of
pr
1.
Maintenance
...
1.1.
Actual error
Format of warning error description recorded in LOG:
Exx
WHAT ==> xx code error/warning alarm
aabb
WHERE ==> if Myy = spiral motor yy
aabb
WHERE ==> if Syy = yy instant product dispensing
aabb
WHERE ==> if Lyy = yy instant product rinsing
aabb
WHERE ==> if C — = coffee brewing
aabb
WHERE ==> if aabb = hexadecimal codes
ddmmm
WHEN ==> day in figures, month in string (3 letters)
hh:mm
WHEN ==> hour:minutes
ii
error index in LOG
NN
number of errors in LOG
Step down counters
RESINS REGENERATION
Allows the use of the water
filter to be checked.
RESET
Select YES to indicate a new
filter has been installed. This
operation returns “Remaining
Qty” to the same value as
“Filter Limit” and the date in the “Last Filter Change” is
changed to today’s date.
Rinsing time
Enables rinsing of the instant
product brewing circuits.
By pressing the ENTER key
the automatic cycle starts, thus
activating each instant product circuit in sequence.
Test Water/Solubles
Allows some calibration
operations to set up the
machine.
BATCHER1 CALIB.
Allows checking the quantity
of powder dispensed by
dosing unit 1.
To carry out the check, you must:
1- remove the brew group
2- prepare a container (e.g. a cup) to collect the coffee
powder
3- Select “Yes” from the menu, the machine grinds a coffee
dose and discharges it
4- check if the weight of the resulting dose corresponds
to what expected, otherwise adjust the dosing unit as
shown in section 7.4
1.2.
Error log
1.3.
Step down counters
1.3.1.
Resins regeneration
1.3.2.
Reset
1.4.
Rinsing time
1.5.
Test water/solubles
1.5.1.
Batcher1 calib.