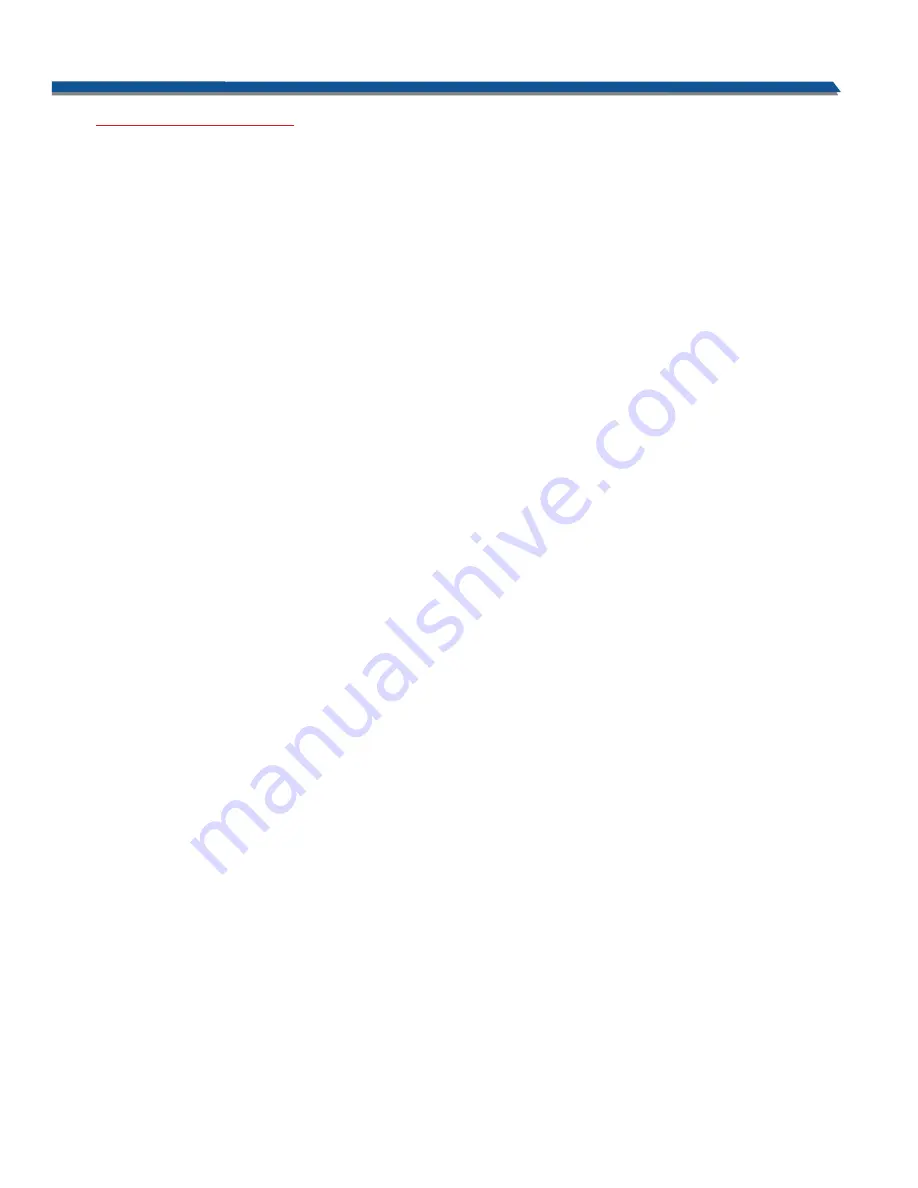
Page # 23
877 1st Ave. N.W. | Sioux Center, IA 51250 | Toll Free: 1.866.722.1488 | siouxautomation.com
OPERATION
REPLACEMENT PARTS
READ complete manual CAREFULLY
BEFORE attempting operation.
877 1st Ave. N.W. | Sioux Center, IA 51250 | Toll Free: 1.866.722.1488 | siouxautomation.com
OPERATION
REPLACEMENT PARTS
READ complete manual CAREFULLY
BEFORE attempting operation.
SHEAR BOLT PROTECTION
•
There are some basic concepts that must be understood to achieve top mixing performance with the mixer.
•
A new machine will need an initial run-in period to polish the auger and mixer sides to achieve correct material movement inside
the mixer. Until the unit is polished inside, one may experience spillage, dead spots, or increased horsepower requirements.
The load size may need to be reduced until the unit is polished inside.
•
Mixing a ration in a vertical mixer generally involves three steps; processing, mixing, and unloading. The operation of the mixer
will vary greatly with the various feeds and climatic conditions. In most instances, “trial and error” is the best method of setting
the machine up for a particular commodity to obtain maximum performance. To prevent over-cutting of feed, we suggest
starting with the restrictor blades in the out position, and then adjusting to obtain the desired coarseness of the mix. The
bulkiest and lightest commodities should be added first. Once these commodities are partially cut and broken apart, others
can be added. Additional cutting will take place during mixing, so be careful not to over cut. The type of mix required varies
from one operation to the other, and therefore, mixing times and procedures will vary as well.
•
It is recommended that commodities are added to the mixing chamber while the augers are turning for maximum mix efficiency.
Starting the augers from a standstill with a full load in the mixing chamber places additional stress on the machine. Even though
it is designed to handle this stress, repetitive startups under load may affect the service life of the machine. If however, due to
circumstances, it is required to restart the machine while loaded, retract the restrictor blades all the way in order to decrease
starting torque as much as possible.
•
The sequence and timing of these steps is very important, and is different for every operator because of variations in materials
and conditions. There is some experimentation that must be done to work out the best equipment, sequence, and timing for
your particular operation. The following steps are some general suggestions to achieve good results.
Follow these procedures when using the machine:
1. Attach the machine to the tractor, as described in the ‘Attaching/Unhooking’ section.
2. Review the Pre-Operation checklist, as described in the ‘Pre-Operation Checklist’ section.
3. Review the location and function of all controls, as described in the ‘Controls’ section.
4. Transport the machine to the feed storage area.
5. Starting:
a. Start the tractor engine and run at low speed.
b. Engage the PTO clutch to start auger.
Important:
Rapid engagement under a heavy load can break the shear bolt. Engage slowly for the best results.
c. Increase engine speed until the desired RPM is reached.
d. Proceed with loading of the ration.
6. Stopping:
a. Stop forward motion.
b. Close unloading door.
c. Stop conveyor when commodity is off.
d. Slow engine to low idle.
e. Disengage PTO clutch.
f. Stop engine if required.
7. Emergency Stopping:
If an emergency should arise, disengage PTO, turn hydraulics off, stop forward motion and stop engine immediately.
8. Loading Feed Rations:
a. Position the mixer where the loading machine has clear and easy access.
b. Start the machine (Refer to #5). Run at rated PTO speed.
c. Begin adding ingredients to the mixing chamber in order to cut and mix a uniform feed ration.
MIXING PROCEDuRE
MIXER OPERATION
Summary of Contents for MAXI-MIXER 3500 TRAILER Series
Page 104: ......