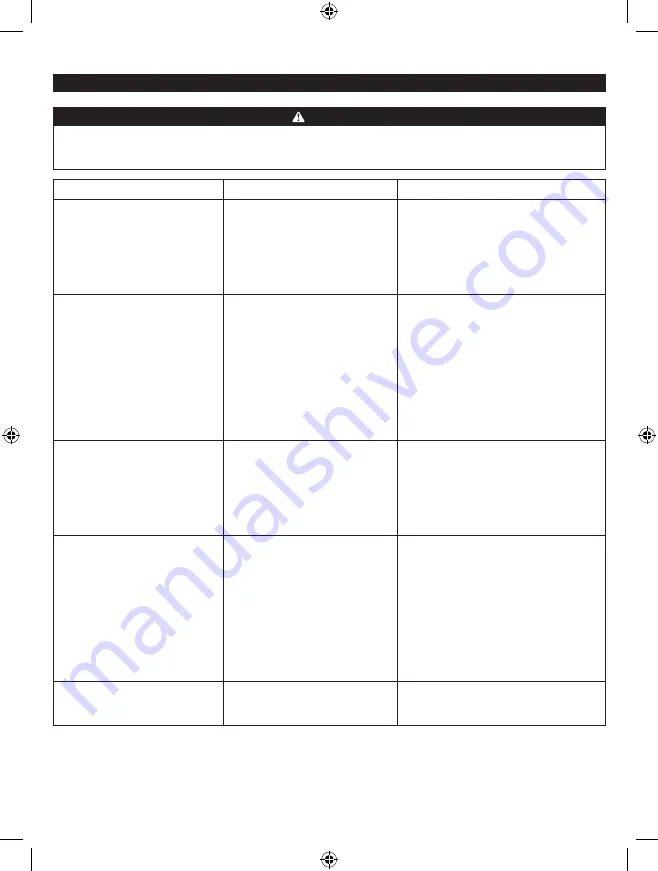
7
tROUBLEshOOtINg
WARNINg
If any of the following symptoms appears during operation, stop using the product immediately, or serious personal
injury could result. Only qualified persons or an authorised service centre can perform repairs or replacement of the
product.
pROBLEM
cAUsE
sOLUtION
Product will not run.
1. Compressor is not turned on.
2. Air line is not connected
properly.
3. There are iron chips into
cutting set.
1. Turn compressor on.
2. Check that air line is connected
properly.
3. Remove the cutting set and any chips
found.
Product runs at normal speed but
fails under load.
1. Motor parts are worn.
2. Cam clutch is worn or sticking
due to lack of lubricant.
1. Lubricate clutch housing.
2. Check for excess clutch oil. Clutch
cases need only be half full. Overfilling
can cause drag on high speed clutch
parts, i.e. a typical oiled/lubricated tool
requires 14.20 ml (1/2 ounce) of oil.
3. Grease lubrication
NOtE:
Heat usually indicates
insufficient grease in chamber. Severe
operating conditions may require more
frequent lubrication.
Product runs slowly. Air flows
slightly from exhaust.
1. Motor parts are jammed with
dirt particles.
2. Power regulator is in closed
position.
3.
Air flow is blocked by dirt.
1.
Check air inlet filter for blockage.
2. Pour air tool lubricating oil into air inlet
as per instructions.
3. Operate the product in short bursts
quickly reversing rotation back and
forth where applicable.
4. Repeat above as needed.
Product will not run. Air flows
freely from exhaust.
1. One or more motor vanes are
stuck due to material build up.
1. Pour air tool lubricating oil into air inlet.
2. Operate the product in short bursts of
forward and/or reverse rotation where
applicable.
3. Tap motor housing gently with a plastic
mallet.
4. Disconnect the air supply. Free the
motor by rotating drive shank manually
where applicable.
5. If the product remains jammed, return
to the service centre.
Product will not shut off.
1. ‘O’ rings throttle valve is
dislodged from seat inlet valve.
1. Replace the ‘O’ ring.
NOtE:
Repairs should be carried out
by a qualified person.
NITTO is a registered trademark owned by Nitto Kohki Co., Ltd