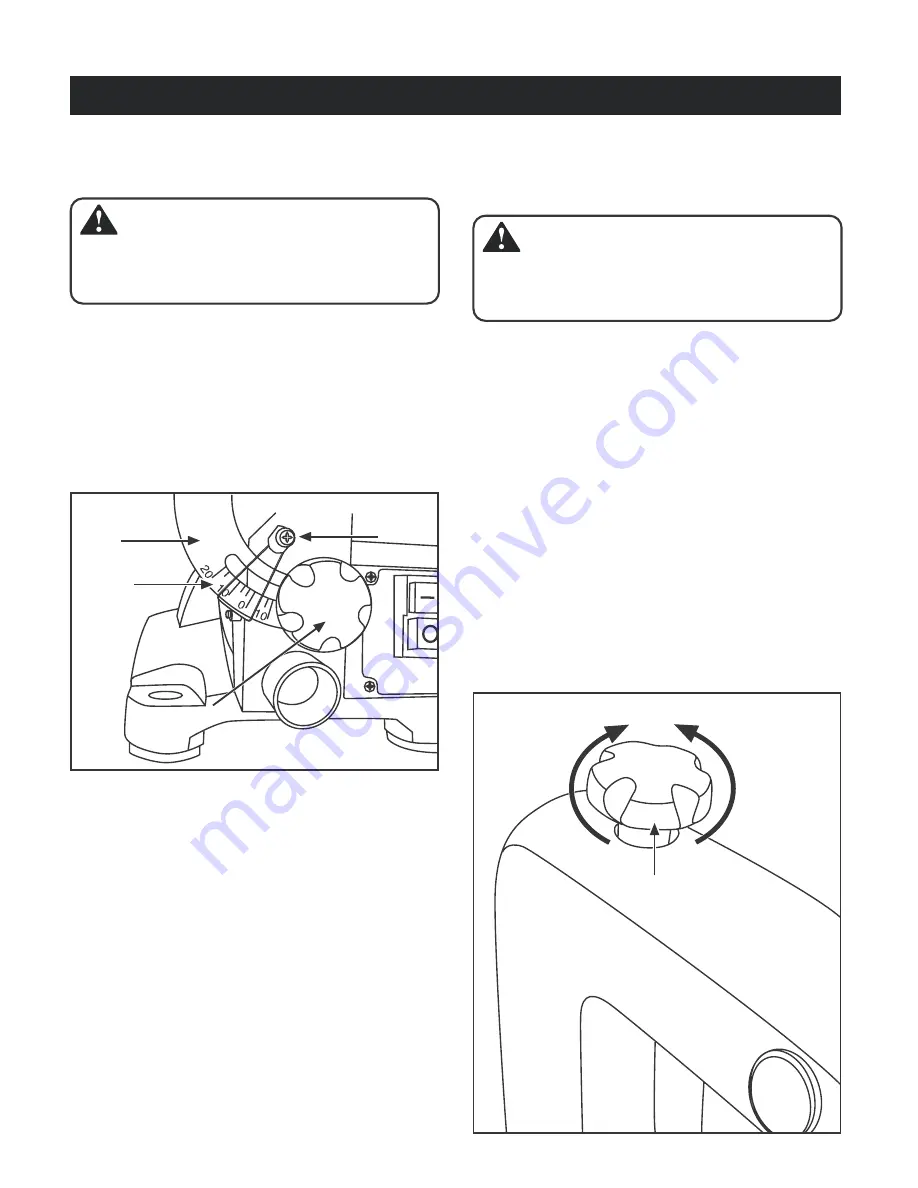
Page 6
ADJUSTMENTS
SETTING THE TABLE FOR HORIZONTAL OR
BEVEL CUTTING
See Figure 6.
A bevel scale is located under the saw table as a convenient
guide for setting the approximate saw table angle for bevel
cutting. When greater precision is required, make practice
cuts on scrap material and adjust the saw table as necessary
for your requirements.
Note:
When cutting at angles, the drop foot should be tilted
so it is parallel to the saw table and rests flat against the
workpiece. To tilt the drop foot, loosen philips screw, tilt drop
foot to the proper angle, then retighten screw.
ADJUSTING BLADE TENSION
See Figure 7.
■
Turn off and unplug the saw from the power source.
■
Turning the blade tension knob counter-clockwise decreases
(or loosens) blade tension.
■
Turning the blade tension knob clockwise increases (or
tightens) blade tension.
Note:
Adjustments to blade tension can be made at any time.
Check tension by the sound the blade makes when plucked
like a guitar string. This method of adding tension to the blade
can be developed with practice and requires knowing your
scroll saw.
■
Pluck the back straight edge of blade while turning tension
adjustment knob. Sound should be a musical note. Sound
becomes less flat as tension increases. Sound decreases
with too much tension.
Note:
Be careful not to adjust blade too tight. Too much tension
may cause the blade to break as soon as you start cutting.
Too little tension may cause the blade to bend or break before
the teeth wear out.
WARNING:
Failure to turn the saw off and unplug the saw from the
power source could result in accidental starting causing
possible serious injury.
Bevel
scale
Blade tension knob
Table lock knob
Fig. 6
Fig. 7
WARNING:
Failure to turn the saw off and unplug the saw from the
power source could result in accidental starting causing
possible serious injury.
Scale
indicator
To tighten
To release
Screw