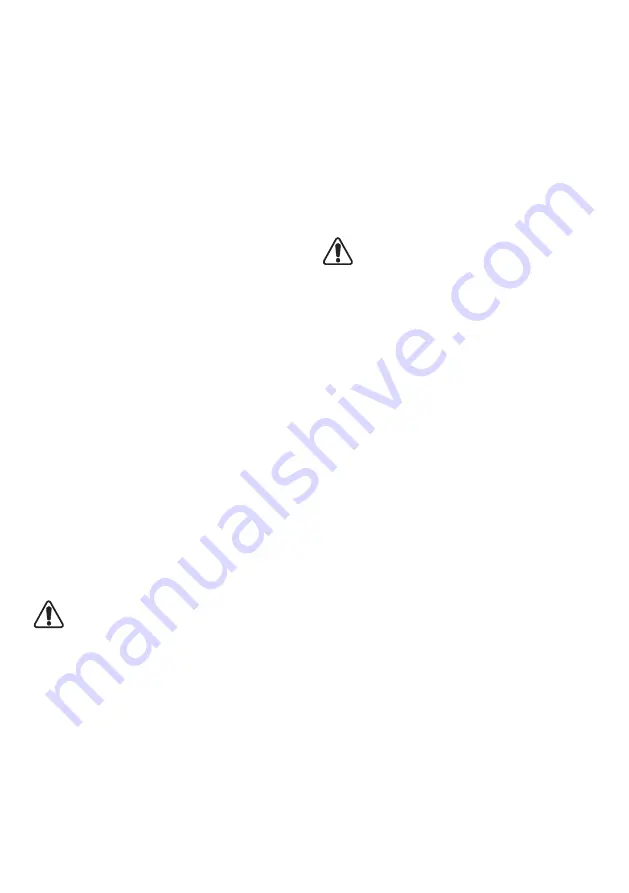
7
they are designed to be used for peripheral grinding
operations and for the application of lateral forces.
Always
use the cutting/grinding wheels with undamaged flanges and
verify that their shape and dimensions are appropriate for the
selected cutting/grinding wheel.
The purpose of flanges is to
support the cutting/grinding wheel and reduce the potential
risk of breakage.
Flanges for cutting wheels may be different
from those of grinding wheels.
Do not use grinding/cutting
wheels that have been fitted on larger tools.
These cutting/
grinding wheels are unsuitable because of their higher speed
as compared to that of smaller tools and could therefore
cause explosions.
Do not “stall” the cutting wheel or
apply an excessive pressure. Do not attempt to increase
the cutting depth.
The application of a high pressure on the
cutting wheel increases the load and the risk of torsion and
bending during cutting, with the consequent risk of rebound
forces or breakage.
Do not stand in line with the cutting/
grinding wheel or behind it while it is rotating. When the
cutting/grinding wheel moves away from the operator’s
body during operation, the rebound force may push the
revolving cutting/grinding wheel and the tool towards the
operator.
If the cutting/grinding wheel bends or the cutting
operations stops for any reason, disconnect the tool from the
power supply and keep it still until the cutting/grinding wheel
has come to a full stop.
Do not attempt to remove the cutting
wheel while it is moving because this could produce a
rebound force. I
dentify the cause of the problem and perform
the necessary corrective actions to prevent the problem from
reoccurring.Do not resume the cutting operation.
Resume the
cutting operation only when the cutting wheel has reached
its maximum speed. The cutting wheel may stall, lift or
produce a rebound force if the tool is restarted when the
work piece is present.
Always use appropriate supports for
panels or large work pieces in order to minimise the risk of
interlocking and rebound forces. Large work pieces tend to
bend because of their weight. Supports must therefore be
placed under the work piece, close to the cutting line and
to the edge of the work piece on both sides.
Pay particular
attention when cutting “pockets” on existing walls or other
areas with limited visibility.
The projecting cutting wheel may
cut gas or water pipes, electrical cables or other objects and
thus produce a rebound force.
ROC50-ROC75:
Do not use sandpaper any larger in
size than the sanding discs. Follow the manufacturers’
instructions when choosing the sandpaper.
The use of a
larger sheet of sandpaper extending beyond the sanding disc
can cause tearing and tangling, leading to jerking movements.
STARTING UP
The compressed air production and distribution
system must meet the requirements indicated by
the data on the identification plate (1).
TOOL ASSEMBLY
The tool is supplied without the compressed air connection
(5); the user can use either a quick release coupling or hose
type connection according to his needs, purke they have an
hole of air passing mm. 8. In the latter case the air line must
be fixed to the nozzle by a hose clip. In the latter case the air
line must be fixed to the nozzle by a hose clip.
ANP125
Screw the auxiliary handle (8) in one of the holes on the
gearbox.
ACCESSORIES ASSEMBLY
TE23
Insert spindle of the wheel or cutter in the collet seating, keep
the collet spindle still using the wrenches (7) supplied and
tighten lock-nut.
ROC50-ROC75
PAD
Block the spindle (4) using the wrench (7) and screw the pad (9).
ABRASIVE PAPER
Velcro discs are mounted by simply pressing them into the
pad (9).
ANP125
1. Insert the spacer (12);
2. insert the abrasive wheel (14);
3. screw and tighten the lock nut (15) using the pin wrench
(7), preventing the spindle form moving using the 17 mm.
spanner (7) or the spindle locking button.
START AND STOPPING
- Starting: push the control lever (2) forward towards the body
of the tool and keep it pressed acting on the safety lever (3).
- Stopping: release the control lever.
The tool continues to rotate after it is turned off.
SELECTING RPM
The number of revolutions can be adjusted by using the speed
control (6) from MAX to OFF. The choice of speed depends on
the characteristics of the abrasive paper disc and the material
to be worked.
ACCESSORIES DISASSEMBLY
TE23
- Block the cllect spindle and unscrew nut with the wrenches
supplied (7).
- Extract the used wheels or cutters.
ROC50 - ROC75
PAD
Block the spindle (4) using the wrench (7) and dismount the
pad (9).
ABRASIVE PAPER
- Used discs can be removed by simply tearing them off;
- new velcro discs are mounted by simply pressing them into
the pad.
ANP125
Lock the wheel spindle by inserting the 17 mm spanner (7) in
the nocth in the spindle between the wheel and the gearbox.
Unscrew the locking ring (15) using the pin wrench (7),
replace the wheel, re-tighten the locking ring.
ALLOWED ACCESSORIES
TE23
Grinder or millers on the market compatible max. Speed of
the tool.
ROC50-ROC75
Ø 75 mm – Ø 50 mm velcro abrasive paper discs.
ANP125
Depressed center Ø 125 mm. Abrasive wheel.