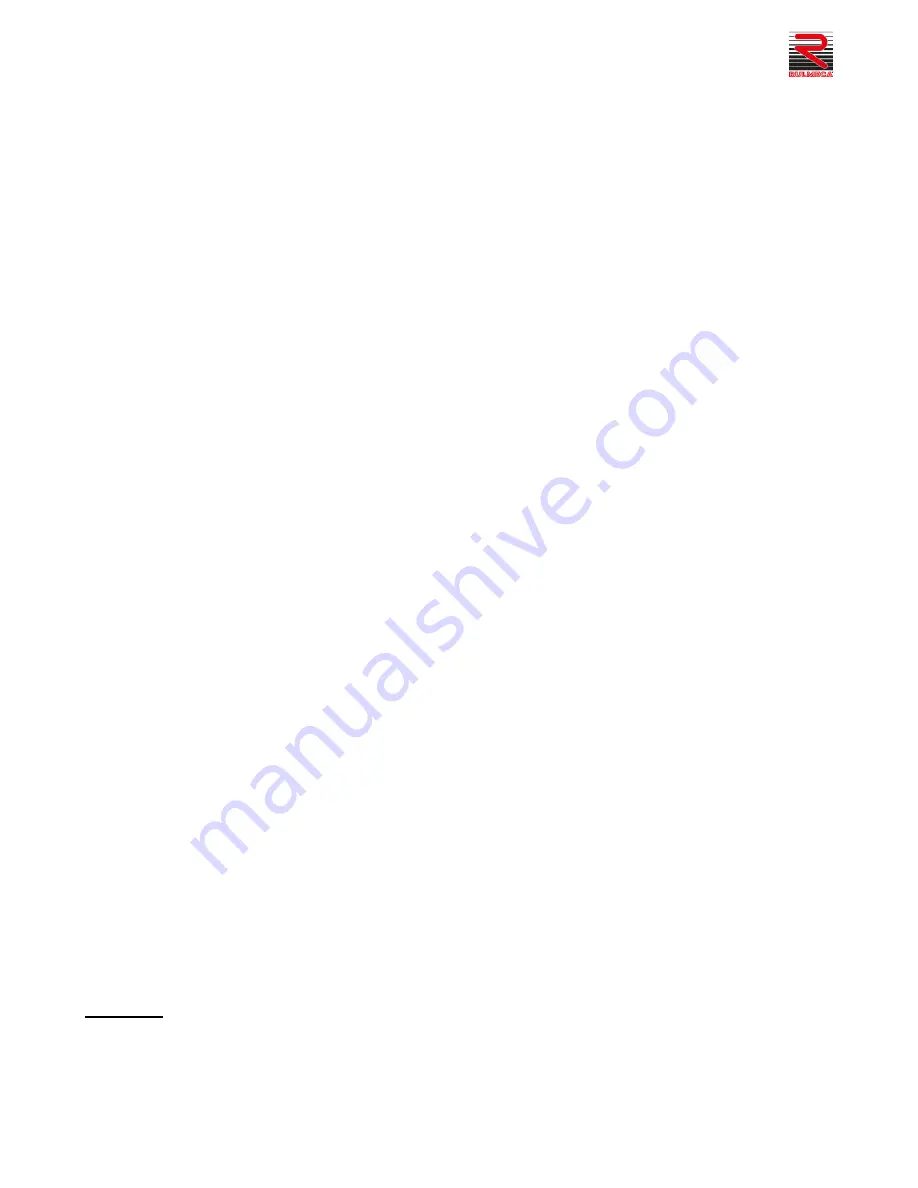
TECHNICAL MANUAL FOR THE RDR BL3 - V1.1 DRIVE ROLLER
Rev. 21/09/2018
page 31
10.1 Thermal overload fault
The Drive Roller motor has thermal overload protection provided by a temperature sensor positioned on the drive
electronics inside the motor casing.
The built-in temperature sensor's task is to monitor constantly the temperature inside the motor casing and send
temperature readings several times per second to the microprocessor.
When the motor casing's temperature exceeds the safety threshold the electronic system activates the used power
limitation function without sending fault signals.
The power limitation function automatically limits the power that can be supplied by the motor by limiting the motor's
current. This function limits motor performance to return the motor to an acceptable temperature. This function is
totally automatic and the power limitation results in the conveyed weight being conveyed with an increased
acceleration ramp.
If the motor continues to overheat despite the power limitation function, when the safety threshold is passed the
motor sends a fault signal, but only after 60 seconds in thermal overload status will the electronics force the arrest
of the motor as a precaution.
Thermal overload protection functions cannot be bypassed or deactivated.
The Drive Roller will restart automatically as soon as its internal temperature returns within the acceptable range.
The overheating of the motor casing may be due to:
-
too many start/stop cycles per minute (reduce the cycles)
-
a heavy weight being conveyed together with the start/stop cycles (reduce the weight, speed or start/stop
cycles)
-
the covering shell preventing proper heat dispersal (the Drive Roller has been subjected to too heavy a
work load)
-
the packages rubbing against side guides, supports or packages or material (films, packing, etc.), being
forced into contact or rubbing against the rollers.
10.2 Overcurrent fault
The Drive Roller is protected against overload due to material jams on the roller conveyor or conveyed packages
that are too heavy, outside the permitted range.
When maximum current is reached, the Drive Roller stops and three restart attempts are made before the fault
signal is sent that shuts down the motor.
In this case the motor shuts down and will not start up again automatically.
To restart:
- disconnect the mains supply to the Drive Roller and make the conveyor safe.
- remove any jams of conveyed materials or other causes of problems,
- restore supply voltage.
After the supply has been reset, if the causes of the fault have been eliminated, the fault signal will be reset and
the Drive Roller will be able to restart regularly.
WARNING:
Interrupt and repeat the START command to the motor in overload fault status to reset the fault and thus
restart the Drive Roller. Pay particular attention to this eventuality if the conveyor is being maintained.
Summary of Contents for RDR BL3
Page 9: ...TECHNICAL MANUAL FOR THE RDR BL3 V1 1 DRIVE ROLLER Rev 21 09 2018 page 9 RIGHT WRONG...
Page 18: ...TECHNICAL MANUAL FOR THE RDR BL3 V1 1 DRIVE ROLLER Rev 21 09 2018 page 18...
Page 19: ...TECHNICAL MANUAL FOR THE RDR BL3 V1 1 DRIVE ROLLER Rev 21 09 2018 page 19...
Page 21: ...TECHNICAL MANUAL FOR THE RDR BL3 V1 1 DRIVE ROLLER Rev 21 09 2018 page 21...