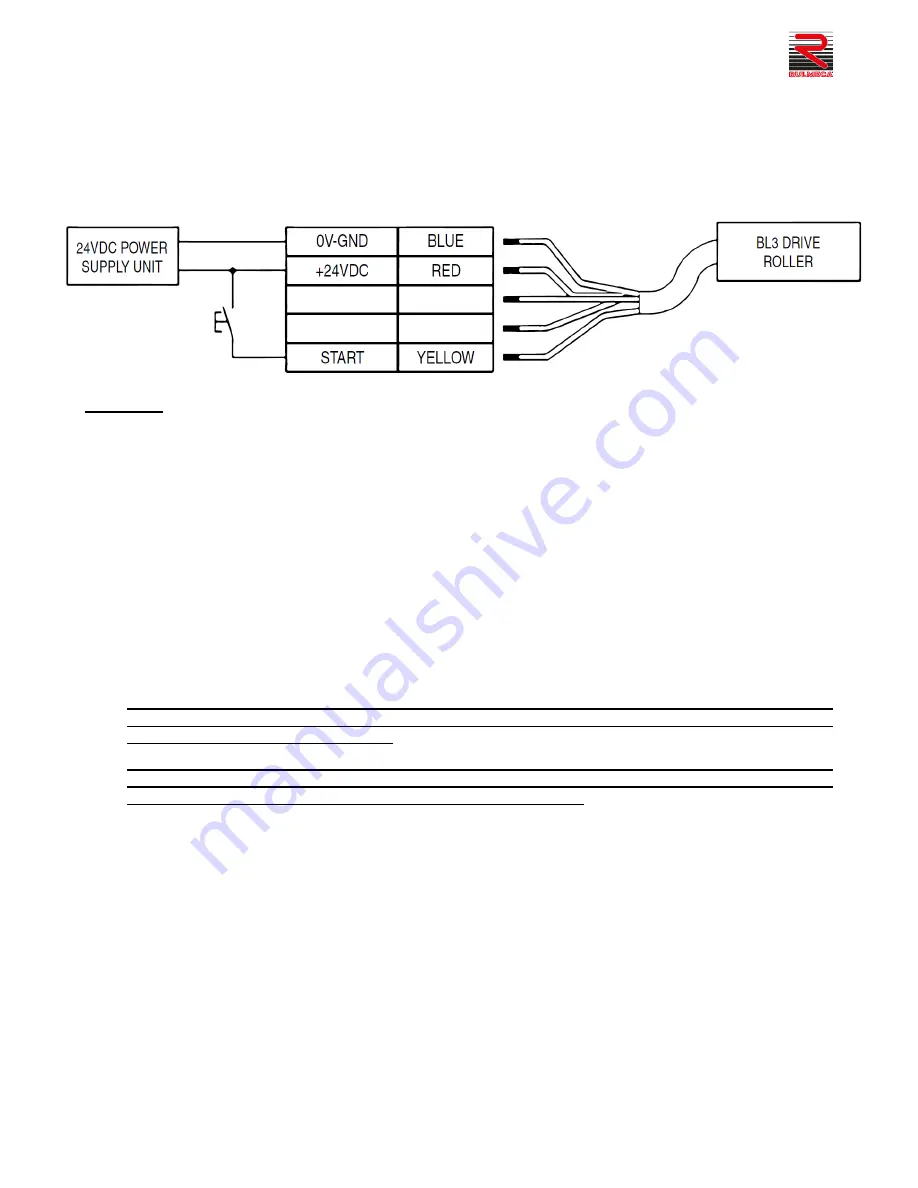
TECHNICAL MANUAL FOR THE RDR BL3 - V1.1 DRIVE ROLLER
Rev. 21/09/2018
page 27
9.2
Starting and stopping Drive Roller
If you wish to operate the Drive Roller without the help of the RMC-BL3 board, proceed as follows.
To start up and stop the Drive Rollers, use only the following connections:
With contact near the Drive Roller:
WARNING:
-
NEVER supply alternating current to the Drive Roller.
-
Supply the Drive Roller only with voltage values within the specified range 18-26 VDC. A supply at
lower voltage (with consequent reduction of torque, current and speed) is permitted if the maximum
conveyed load is reduced and subject to authorization from Rulmeca, providing all the data of the
application (using the form on the last page).
-
Protect with a suitable fuse the power supply cable coming from the power supply unit.
-
If a reduced number of Drive Roller wires is used, make sure that the remaining unused wires are
insulated.
-
Make sure that the connections between the wires are professional and secure, without false
contacts. Insulate the connections to prevent short circuits.
-
Make sure that the 0V-GND coming from the power supply unit is clean and free of disturbance
coming from alternating current motors and the like.
-
NEVER interrupt the continuity of the main supply wires (blue and red) to stop the Drive Roller.
Doing so could damage the Drive Roller permanently. Drive Rollers returned because of such
damage are not covered by warranty.
-
The Drive Roller is not designed to receive forced motion. NEVER force the rotation of the Drive
Roller moving it by hand. Check that loading/unloading packages manually with forklift trucks or
manipulators does not force rotation of stationary Drive Rollers.
Summary of Contents for RDR BL3
Page 9: ...TECHNICAL MANUAL FOR THE RDR BL3 V1 1 DRIVE ROLLER Rev 21 09 2018 page 9 RIGHT WRONG...
Page 18: ...TECHNICAL MANUAL FOR THE RDR BL3 V1 1 DRIVE ROLLER Rev 21 09 2018 page 18...
Page 19: ...TECHNICAL MANUAL FOR THE RDR BL3 V1 1 DRIVE ROLLER Rev 21 09 2018 page 19...
Page 21: ...TECHNICAL MANUAL FOR THE RDR BL3 V1 1 DRIVE ROLLER Rev 21 09 2018 page 21...