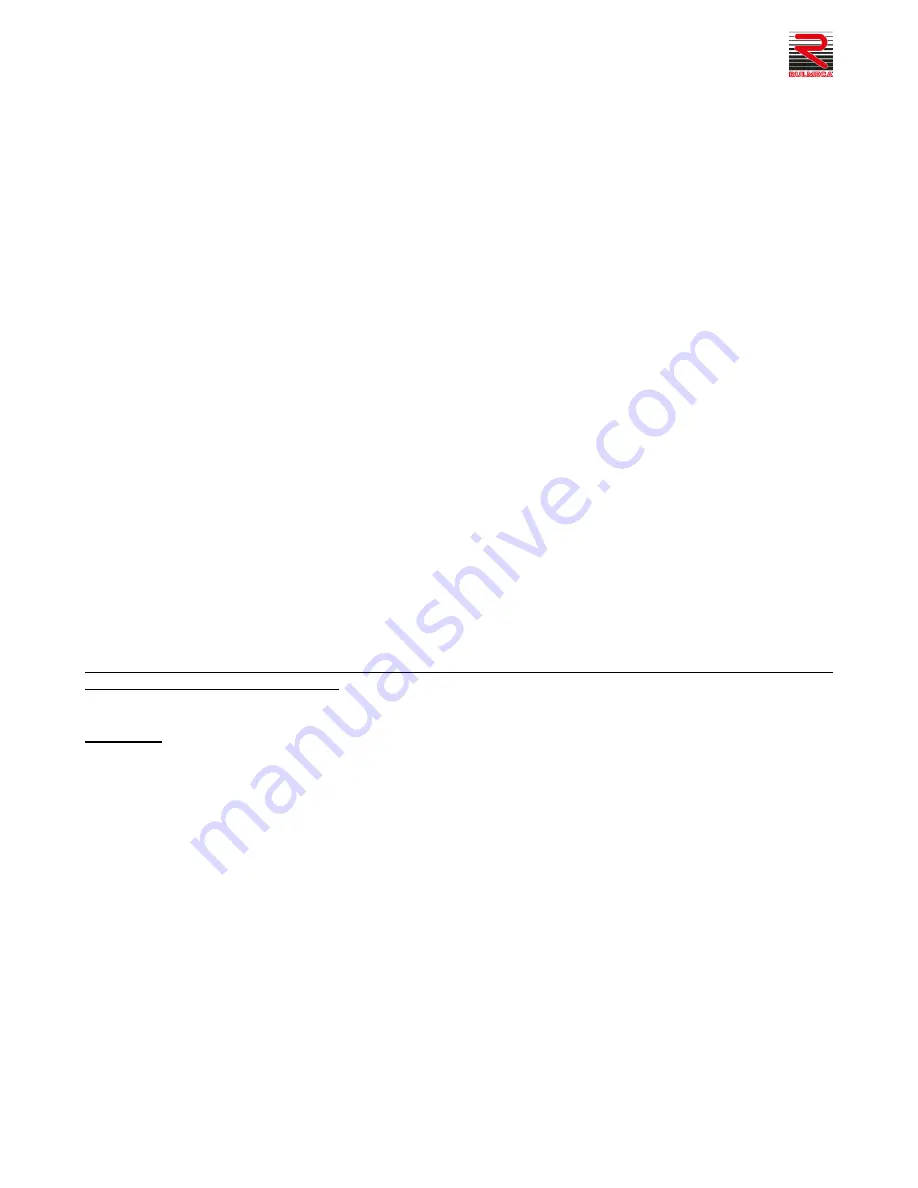
TECHNICAL MANUAL FOR THE RDR BL3 - V1.1 DRIVE ROLLER
Rev. 21/09/2018
page 22
MECHANICAL INSTALLATION
The Drive Roller is positioned inside the roller support profile.
The inner distance of the roller support profile sides (B) must not be 1 mm more or less than the
“C” value of the
Drive Roller; see the technical drawings of the Drive Roller and the order data.
In the structure, the fixing hole on the cable side must be 12 Ø, or size 11 hexagonal hole. Do not use open
recesses or long slot holes because when the nuts are tightened the reduced support surface for the nuts could
cause them to work loose.
On the side opposite the cable, make an 8 Ø hole, as for all driven rollers.
The Drive Roller is supplied with all the nuts and bolts required for installation already fitted to the Drive Roller,
where this is possible. Alternatively, the nuts and bolts are placed in a transparent plastic bag that accompanies
the installation instruction sheet and the warranty.
For correct installation of the Drive Roller, use a size 18 wrench that is no thicker than 4 mm so that it can be
inserted between the structure and the Drive Roller, to hold the inner M12 flanged locknut, enabling the tightening
of the outer M12 flanged nut.
The correct mechanical installation sequence is as follows:
•
Tilt the Drive Roller and insert the cable and the threaded pin into the 12 Ø hole or size 11 hexagonal hole
that must be made in the roller support profile on the cable side.
•
Position the Drive Roller in its seat.
•
Fit any straps or belts in the grooves.
•
Align the bored and threaded M8 pin (side opposite the cable) on the respective 8 Ø hole in the structure.
•
From outside the structure, insert the hexagonal head M8x15 screw and the spring washer and tighten the
screw with a size 13 wrench.
•
Tighten the M12x1.5 H12 flanged stainless steel nut with a size 18 wrench.
Final tightening of the nuts and screws:
Once the Drive Roller has been inserted, make sure that all the mechanical parts have been positioned correctly.
Make sure that there are no mechanical obstacles to normal rolling of the rollers.
Immobilize the M12 flanged locknut on the cable output side inside the structure, tighten the external M12 flanged
nut with a torque wrench to 60-65 Nm.
Then tighten the hexagonal head screw M8 on the idle side to 10-15 Nm.
WARNING
:
•
Noncompliance with the warnings, instructions and torque settings can cause the threaded pin to
rotate in the frame at less than the motor's torque, so that the cable is twisted. A twisted cable leads
to a malfunction, short circuit or blockage of the Drive Roller. Drive Rollers that are returned because
a cable has been damaged or twisted are not covered by the warranty.
•
Verify periodically the tightening torque of the Drive roller
’s fixing nut.
•
When fitting the Drive Roller (and rollers) in painted profiles, make sure that the fixing nut and the
relative washers come into contact with the metal surface of the grounded profile to ensure correct
grounding of the static electricity that may form on the rollers and Drive Roller and possibly cause
sparks and faults.
•
In order to avoid injury, do not place fingers between the rollers and the transmission (round belts,
Poly-V belts or chains).
•
During assembly, do not allow technicians to work in the area without PPE. Do not allow them to wear
long hair or wear loose or flowing items such as ties, loose or wide sleeves or garments that could get
accidentally caught up in moving parts.
•
If required to do so by law, the roller conveyor manufacturer must guard moving or potentially
hazardous part, provide an emergency stop system and place appropriate warning signs.
Summary of Contents for RDR BL3
Page 9: ...TECHNICAL MANUAL FOR THE RDR BL3 V1 1 DRIVE ROLLER Rev 21 09 2018 page 9 RIGHT WRONG...
Page 18: ...TECHNICAL MANUAL FOR THE RDR BL3 V1 1 DRIVE ROLLER Rev 21 09 2018 page 18...
Page 19: ...TECHNICAL MANUAL FOR THE RDR BL3 V1 1 DRIVE ROLLER Rev 21 09 2018 page 19...
Page 21: ...TECHNICAL MANUAL FOR THE RDR BL3 V1 1 DRIVE ROLLER Rev 21 09 2018 page 21...