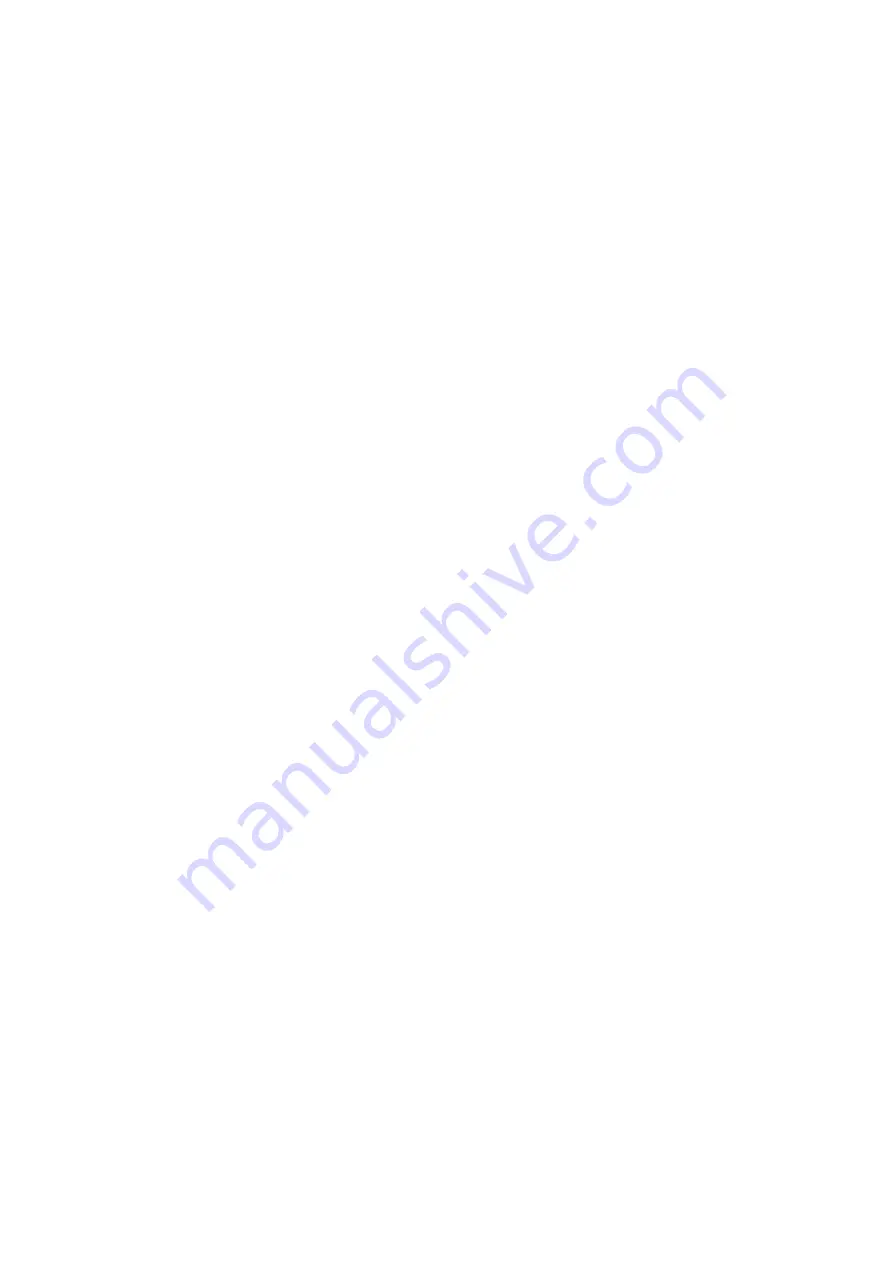
ROYAL ENFIELD WORKSHOP MANUAL
tightening the steering stem locknut after
loosening the nuts on the three pinch bolts
which secure the fork head to the steering stem
and to the two main tubes. The head should be
adjusted so that when the front wheel is lifted
clear of the ground a light tap on the handlebars
will cause the steering to swing to full lock in
either direction, while at the same time there
should be only the slightest trace of play in the
bearings. When testing for freedom of
movement the steering damper, if fitted, should
be disconnected by unscrewing the anchor plate
pin.
Adjustment of the steering head depends on
the ability of the fork head to slide on the
steering stem and on the fork main tubes. A
rubber washer is interposed between the fork
head and the top of the lamp bracket tube to
permit the necessary movement. If this rubber
washer is fully compressed while there is still
some play in the steering head, it will be
necessary to remove the fork head (see
paragraph 5) and shorten the lamp bracket tube
by, say, 1/32 in. Alternatively, if the lamp
bracket tube is loose when the steering head is
correctly adjusted, it can be tightened by fitting
an additional steel washer (Part No. 35974)
beneath the rubber washer.
It is also possible that the steering head
cannot be adjusted because the main tube is
bottoming in the recess in the fork head in
which it fits. In this case the fork crown clamp
screws must be loosened, thus permitting the
main tubes to slide through the fork crown. Do
no forget to tighten the fork head pinch bolts
and the fork crown clamp screws after adjusting
the steering head.
5. Removal of Facia Panel Fork Head,
Spring, etc.
To remove the Facia Panel Fork Head for
access to the lamp bracket tubes (or to change
the fork spring without disturbing the bearings)
proceed as follows - disconnect all control
cables at the handlebar end and remove the
headlamp from the lamp brackets. The switch
panel can conveniently be removed from the
back of the lamp so that the body of the lamp
can be removed completely.
Now unscrew the two Fork Spring Scroll
Bolts from the fork head, unscrew the nuts on
the fork head clip bolt and the two main tube
clip bolts, remove the three clip bolt sleeves and
knock out the three clip bolts. The facia panel
fork head can now be tapped gently upwards
with a hide mallet or a hammer and a wooden
drift but care must be taken to hit only the more
solid parts of the fork head, i.e. beneath the
handlebar clip and at the back of the main tubes,
avoiding the underside of the comparatively thin
portion in front of the speedometer.
After removal of the fork head the lamp
bracket tubes can be lifted straight off and the
springs can be withdrawn from the upper end of
the main tubes after unscrewing the oil level
plug and the nut which secures the spring stud
to the fork end and knocking the spring stud
upwards.
6. Removal of Main Tubes
To remove the main tubes first dismantle the
fork as described in paragraph 2, then remove
the facia panel fork head and lamp bracket
tubes as described in paragraph 5. Now loosen
the fork crown clamp screws and knock the
main tubes out of the fork crown either upwards
or downwards as may be most convenient. If
the machine has been in an accident and the
tube is badly bent both above and below the
fork crown, it may be necessary to cut through
the tube with a hacksaw before it can be
withdrawn.
7. Reassembly of Parts
No difficulty should be experienced with
this.
When refitting the main tube, use the lamp
bracket tube as a guide to its correct position in
the fork crown. The small shoulder some 1.1/2
in. from the upper end of the tube should be
flush with the top of the lamp bracket tube
when the latter is in position on the fork crown.
With the main tube in this position, tighten the
fork crown clamp screws before fitting the facia
panel fork head.
If new oil seals have been fitted it may be
found that the action of the fork is very stiff
when the gland nuts are tightened down fully.
In this case the nuts may be left half a turn or
so slack until the seals have freed off, after
which they should be tightened down. Note that
the seal, must be fitted with the larger bore
uppermost, i.e. with the scraping edges facing
downwards.
When refitting the three clip bolts, which
secure the fork head to the main tubes and
steering stem, make sure that the clip bolts and
their sleeve, are correctly fitted so that the
cut-away portions of them bear against the
tubes. Any attempt to tighten the nuts with the
bolts or sleeves incorrectly fitted may result in
cracking the facia panel fork head.
8. Lubrication
The lubrication of the fork bearings is
effected by the oil which forms the hydraulic
damping medium. The oil level is fixed by a
cross hole in the spring stud leading to a drilled
passage terminating in the oil level plug. To fill
each fork leg to the correct level remove the
plug screws from the fork head and the oil level
plugs from the fork end. Pour oil in at the top
until it runs out at the bottom of the fork. Wait
till oil has stopped running and replace level
plugs and plug screws.
Recommended grades of oil are Castrolite,
Mobiloil Arctic, Essolube 20, B.P. Energol
S.A.E. 20, Shell X-100 20/20 w.
Section J4 Page 3
www.hitchcocksmotorcycles.com
Summary of Contents for 350 BULLET 1949
Page 7: ...ROYAL ENFIELD WORKSHOP MANUAL w w w h i t c h c o c k s m o t o r c y c l e s c o m ...
Page 53: ...ROYAL ENFIELD WORKSHOP MANUAL w w w h i t c h c o c k s m o t o r c y c l e s c o m ...
Page 59: ...ROYAL ENFIELD WORKSHOP MANUAL w w w h i t c h c o c k s m o t o r c y c l e s c o m ...
Page 71: ...ROYAL ENFIELD WORKSHOP MANUAL w w w h i t c h c o c k s m o t o r c y c l e s c o m ...
Page 81: ...ROYAL ENFIELD WORKSHOP MANUAL w w w h i t c h c o c k s m o t o r c y c l e s c o m ...
Page 100: ...ROYAL ENFIELD WORKSHOP MANUAL NOTES w w w h i t c h c o c k s m o t o r c y c l e s c o m ...
Page 101: ...ROYAL ENFIELD WORKSHOP MANUAL NOTES w w w h i t c h c o c k s m o t o r c y c l e s c o m ...