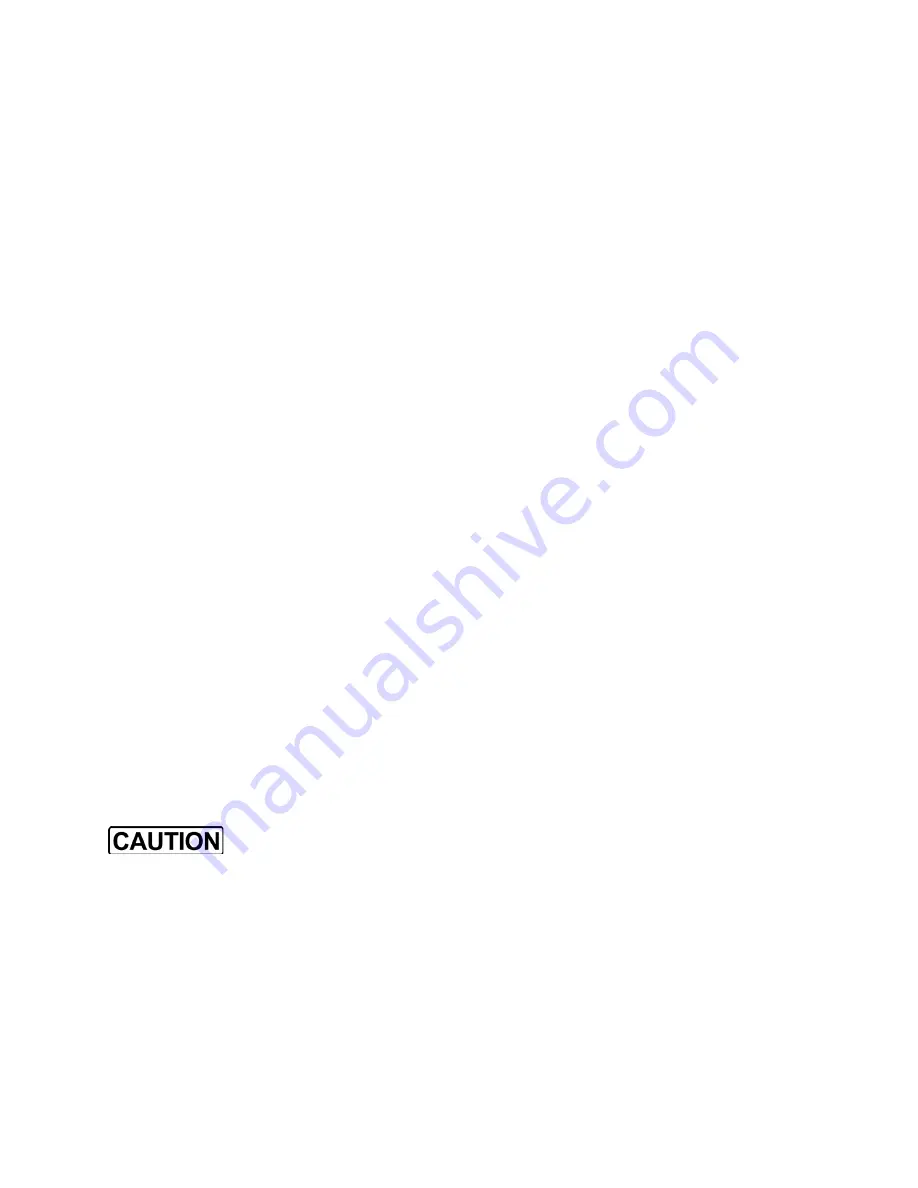
Section 2 Installation
SG10XY Manual
www.rottlermfg.com
2-10
Preparation for Placement
Air supply is connected at the left side of the machine, at base of lower casting. Connection can either
be a quick disconnect or permanent threaded connection. Be certain to use an adequately sized airline,
permitting proper operation of float. Air pressure should never drop below 90 PSI at any time. Failure to
provide adequate air supply may cause improper floating and clamping.
At this time, some customers will install a T fitting or manifold at the regulator, allowing another air hose to
be connected, providing a connection point for air tools. The auxiliary hose, if fitted, should be of sufficient
length to easily reach the entire front of the machine.
This machine comes pre-wired and ready to be connected to the power source. The power source should
meet all local and national electrical codes. This service should connect to its own circuit breaker or fuse.
The machine will require 220 VAC, 15 amp, single-phase power supply.
Machine Installation
• Lift Machine using a fork lift. Move fork lift to front of Machine and separate forks so they are visually
centered.
• Insert forks under front-center of Machine, using care not to damage Foot Pedals Valve or Air Lines.
Tilt forks slightly upward so Machine will lean toward fork lift and lift Machine.
• While Machine is on fork lift, install six (6) Leveling Screws and Jam Nuts in holes provided in bottom
of Machine Base. Two (2) Screws installed in rear-corners and two (2) Screw installed in front corners
of Machine Base will serve as Leveling Screws; while two (2) Screws installed in center of Machine
Base will serve only as Support Screws.
• Move Machine to desired location and placed leveling bolts over the center hole of the Leveling Pad.
Be certain to allow sufficient clearance to allow access for leveling and also for connecting air and
electrical lines.
• Lower machine onto leveling pads making certain that the leveling bolts align into counter bore on
leveling pads.
•
Be certain nothing interferes with air or electrical tracking running from the floating head assembly to
the cabinet.
• Determine there is no possibility of air or electrical tracking dragging on wall surfaces or adjacent
machinery.
• Wipe top Rails with a clean, dry cloth to remove protective shipping oil.
Do not attempt to move the Work Head unless Air Supply is connected, and air
valve is turned on and power has been turn on (make sure the EMERGENCY STOP
Button is off). From the touch screen, float the workhead, spray, and clean surface with (WD40) or similar
degreaser and flow the work Head side by side to remove all the shipping oil from under the work head.
(Top Upper surfaces rails should be clean and free of oil).
Summary of Contents for SG10XY
Page 2: ......
Page 4: ......
Page 10: ...Section 1 Introduction SG9MTS Manual www rottlermfg com 1 5...
Page 19: ...Section 2 Installation SG10XY Manual www rottlermfg com 2 8 Machine Dimensions...
Page 72: ...Section 5 Operating Instructions SG10XY Manual www rottlermfg com 5 18...
Page 73: ...Section 5 Operating Instructions SG10XY Manual www rottlermfg com 5 19...
Page 84: ...Section 5 Operating Instructions SG10XY Manual www rottlermfg com 5 30...
Page 90: ...Section 6 Maintenance SG10AXY Manual www rottlermfg com 6 5...
Page 93: ...Section 6 Maintenance SG10AXY Manual www rottlermfg com 6 8 Spindle Lock Nut Service Procedure...
Page 98: ...Section 6 Maintenance SG10AXY Manual www rottlermfg com 6 13...
Page 110: ...Section 8 Machine Parts SG10XY Manual www rottlermfg com 8 7 Base Assembly 88 89 87...
Page 117: ...Section 8 Machine Parts SG10XY Manual www rottlermfg com 8 14 Transmission Assembly...
Page 123: ...Section 8 Machine Parts SG10XY Manual www rottlermfg com 8 20 Solenoid Valves...
Page 129: ...Section 8 Machine Parts SG10XY Manual www rottlermfg com 8 26 Air Line Diagram...
Page 130: ...Section 8 Machine Parts SG10XY Manual www rottlermfg com 8 27...
Page 132: ...Section 9 Options SG10XY Manual www rottlermfg com 9 2...
Page 134: ...Section 10 Material Data Safety Sheets SG10XY Manual www rottlermfg com 10 2...
Page 135: ...Section 10 Material Data Safety Sheets SG10XY Manual www rottlermfg com 10 3...
Page 136: ...Section 10 Material Data Safety Sheets SG10XY Manual www rottlermfg com 10 4...
Page 137: ...Section 10 Material Data Safety Sheets SG10XY Manual www rottlermfg com 10 5...
Page 138: ...Section 10 Material Data Safety Sheets SG10XY Manual www rottlermfg com 10 6...
Page 139: ...Section 10 Material Data Safety Sheets SG10XY Manual www rottlermfg com 10 7...
Page 140: ...Section 10 Material Data Safety Sheets SG10XY Manual www rottlermfg com 10 8...
Page 141: ...Section 10 Material Data Safety Sheets SG10XY Manual www rottlermfg com 10 9...
Page 142: ...Section 10 Material Data Safety Sheets SG10XY Manual www rottlermfg com 10 10...
Page 143: ...Section 10 Material Data Safety Sheets SG10XY Manual www rottlermfg com 10 11...
Page 144: ...Section 10 Material Data Safety Sheets SG10XY Manual www rottlermfg com 10 12...
Page 145: ...Section 10 Material Data Safety Sheets SG10XY Manual www rottlermfg com 10 13...
Page 146: ...Section 10 Material Data Safety Sheets SG10XY Manual www rottlermfg com 10 14...