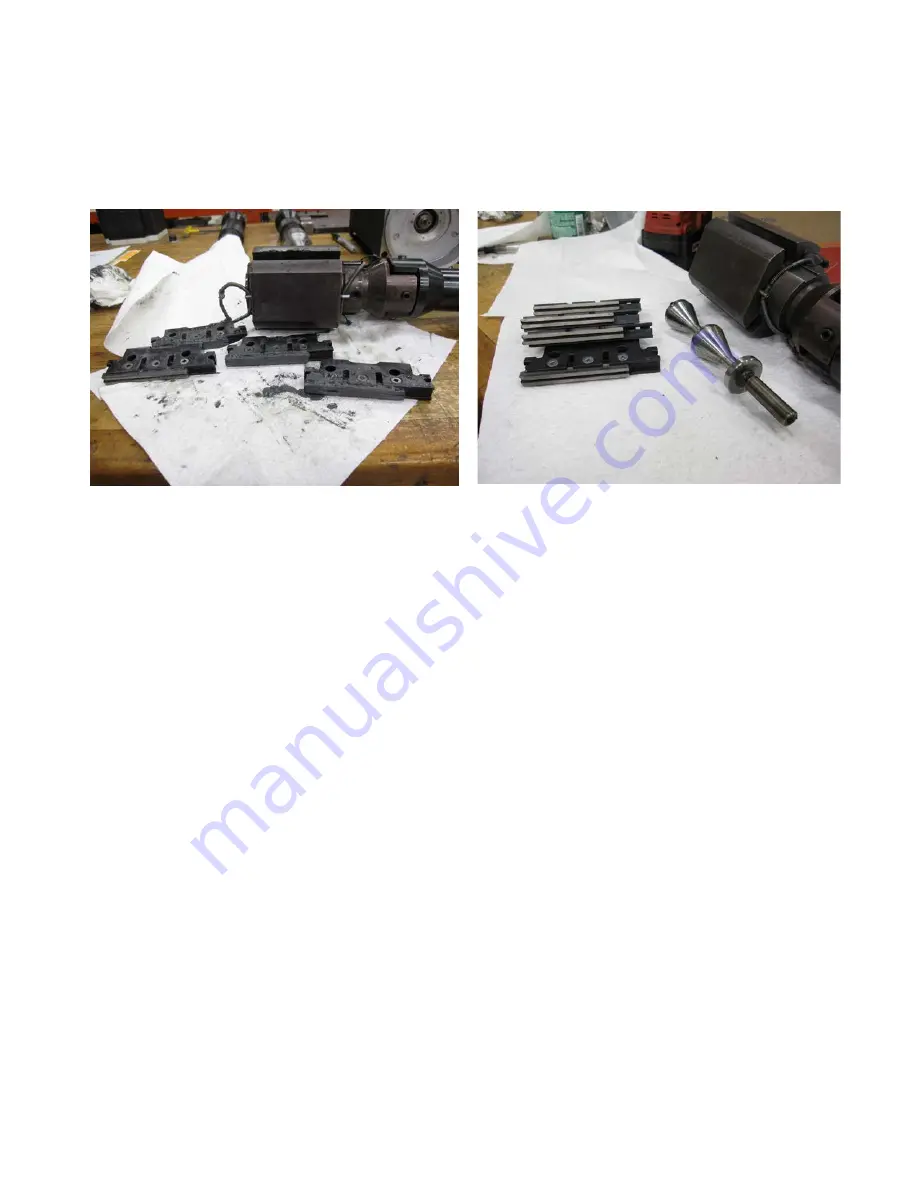
Section 5 Operating Instructions
H85A Manual
www.rottlermfg.com
5-10
Once you have achieved the desired contact area you must clean the abrasive from the cylinder that was
honed, diamond stones, stone holders and hone head. We recommend removing the stone holders, hone
body and feed out cone rod from hone head and cleaning thoroughly to remove any lapping compound. If
not completely removed, remaining lapping compound could cause excessive wear to moving parts in the
hone head.
Dressing Diamond Abrasives
Diamond Abrasives use a metal bond to hold the individual diamond particles. Failing to dress the stones
after honing 30 - 50 blocks will increase the pressure required to remove stock or the stock removal rate
slows down significantly. This will result in finishes with excessive folded and torn metal. Undressed
stones will also cause excess bore distortion and inaccuracies in the boring process. This is caused by
the diamond abrasive dulling or the bond not breaking down. The edge of the stone will also become very
sharp. This is a normal occurrence and is easily corrected by removing the holder/abrasive assembly,
use a wire brush to dress the abrasive. A common method is to remove the stone holder from the hone
head. Leave the stone in the stone holder and move the stone through a bench grinder wire wheel. The
brush rotation should be across the narrow width of the stone. Turn the holder over and pass the stone
through the wheel again. This process will return the abrasive to a like new cutting condition, and put a
slight radius on the edge of the abrasive stick (approx. .005 inch .127mm)
Torn Metal
This is often caused by improper coolant mix, lack of dressing, or the use of high honing pressure during
the finishing process. The Rottler hone head is capable of very high loads. If problems with torn metal
are encountered verify the coolant mix, proper dressing of the abrasives, and reduce the finishing load
during the final hone stage. If required make several strokes manually with minimum stone pressure (10-
20%).
Stock Removal Rate
The hardness of the cylinder you are honing will affect the stock removal rate. If you find the stock
removal rate for a given cylinder is slower than normal check to make sure you have properly dressed the
stones. Improperly dressed stones can increase honing time by as 50% or more. Improperly dressed
stones will also produce an unacceptable finish.
Diameter Range
Because the diamond abrasives break down very slowly, a single set of stones is limited in its diameter
range. One set of diamonds should be used for each stone holder range. A set of diamonds can not be
constantly changed from one stone holder size to another. The stones would constantly be in the break-
in process and very poor performance or finishes will result.
Summary of Contents for H85A
Page 2: ......
Page 4: ......
Page 10: ...Section 1 Introduction H85A Manual www rottlermfg com 1 5 Specifications...
Page 18: ...Section 2 Installation H85A Manual www rottlermfg com 2 7...
Page 23: ...Section 2 Installation H85A Manual www rottlermfg com 2 12 Top View...
Page 66: ...Section 4 Control Definitions H85A Manual www rottlermfg com 4 26...
Page 106: ...Section 5 Operating Instructions H85A Manual www rottlermfg com 5 38...
Page 112: ...Section 6 Maintenance H85A Manual www rottlermfg com 6 5 Grease Fitting Locations...
Page 120: ...Section 6 Maintenance H85A Manual www rottlermfg com 6 13 Z Axis Motor Belt Adjustment...
Page 126: ...Section 6 Maintenance H85A Manual www rottlermfg com 6 19...
Page 128: ...Section 7 Troubleshooting H85A Manual www rottlermfg com 7 1...
Page 132: ...Section 8 Machine Parts H85A Manual www rottlermfg com 8 2 Oiler and Filter Assembly...
Page 133: ...Section 8 Machine Parts H85A Manual www rottlermfg com 8 3 Linear Rails and X Axis Rack...
Page 134: ...Section 8 Machine Parts H85A Manual www rottlermfg com 8 4 Coolant Pump Assembly...
Page 135: ...Section 8 Machine Parts H85A Manual www rottlermfg com 8 5 Doors...
Page 136: ...Section 8 Machine Parts H85A Manual www rottlermfg com 8 6 Base Plate Assembly...
Page 138: ...Section 8 Machine Parts H85A Manual www rottlermfg com 8 8 Linear Rails...
Page 139: ...Section 8 Machine Parts H85A Manual www rottlermfg com 8 9 Oiler Distribution Block...
Page 140: ...Section 8 Machine Parts H85A Manual www rottlermfg com 8 10 Z Axis Motor Assembly...
Page 141: ...Section 8 Machine Parts H85A Manual www rottlermfg com 8 11 Inner Wire Track Assembly...
Page 143: ...Section 8 Machine Parts H85A Manual www rottlermfg com 8 13 Upper Section...
Page 144: ...Section 8 Machine Parts H85A Manual www rottlermfg com 8 14 Outer Wire Track Assembly Mounts...
Page 145: ...Section 8 Machine Parts H85A Manual www rottlermfg com 8 15 Wire Tracks...
Page 147: ...Section 8 Machine Parts H85A Manual www rottlermfg com 8 17 Inner Components...
Page 149: ...Section 8 Machine Parts H85A Manual www rottlermfg com 8 19 Feed Motor Assembly...
Page 150: ...Section 8 Machine Parts H85A Manual www rottlermfg com 8 20 Lower Section...
Page 151: ...Section 8 Machine Parts H85A Manual www rottlermfg com 8 21 Spindle Drive Motor Assembly...
Page 152: ...Section 8 Machine Parts H85A Manual www rottlermfg com 8 22 Spindle Drive Cover...
Page 154: ...Section 8 Machine Parts H85A Manual www rottlermfg com 8 24 Inside Parts...
Page 155: ...Section 8 Machine Parts H85A Manual www rottlermfg com 8 25 Inside Components...
Page 156: ...Section 8 Machine Parts H85A Manual www rottlermfg com 8 26 Computer Components...
Page 157: ...Section 8 Machine Parts H85A Manual www rottlermfg com 8 27...
Page 158: ...Section 8 Machine Parts H85A Manual www rottlermfg com 8 28 Electrical Panel Assembly...
Page 160: ...Section 8 Machine Parts H85A Manual www rottlermfg com 8 30 Pendant Mount...
Page 161: ...Section 8 Machine Parts H85A Manual www rottlermfg com 8 31 Coolant Sump Tank...
Page 162: ...Section 8 Machine Parts H85A Manual www rottlermfg com 8 32 Wiring Diagram...
Page 164: ...Section 9 Options H85A Manual www rottlermfg com 9 2...