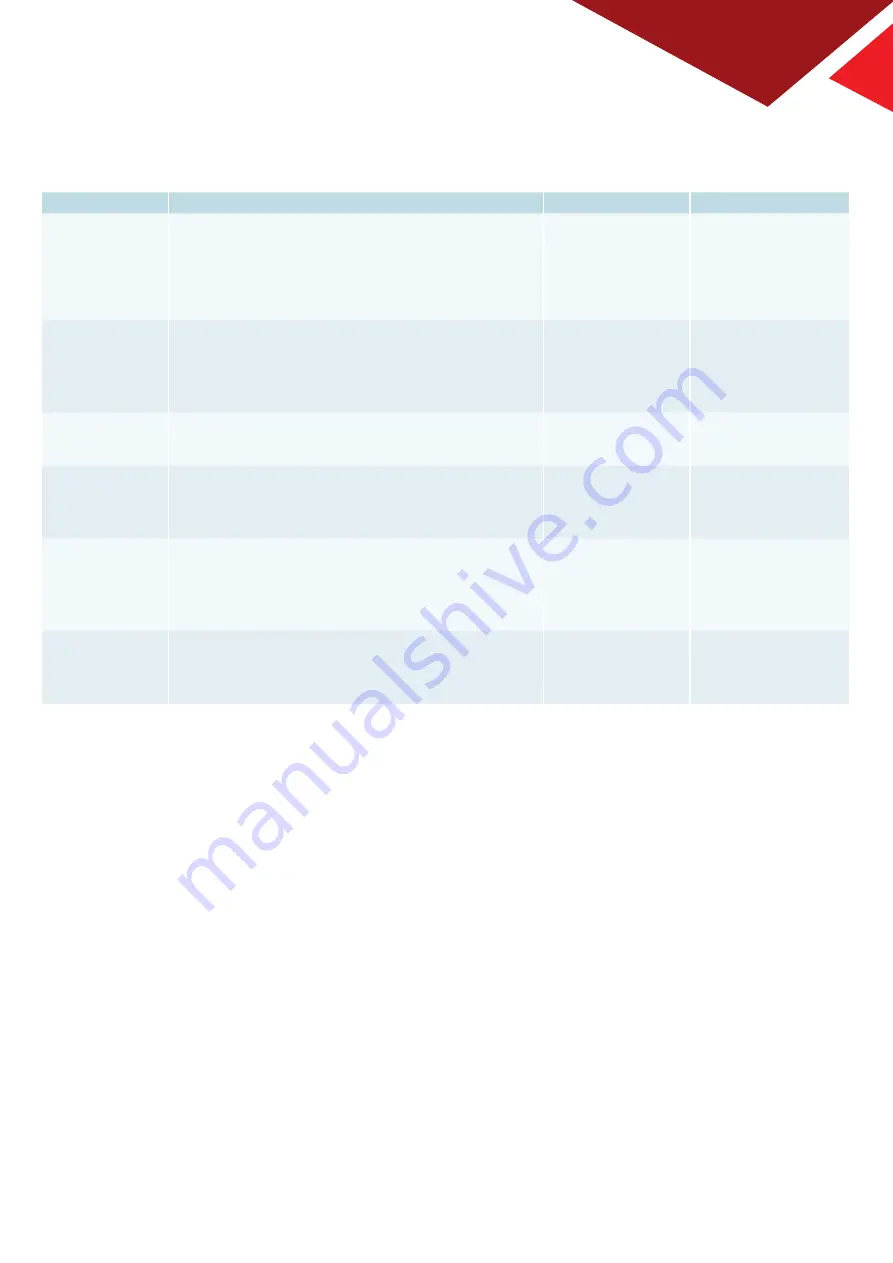
33
8
OVERVIEW OF ACCESSORIES
8.1 Overview and Order Numbers
Type
Product name
Description
Art. Nr.
Exhaust Filter
Oil Mist Separator AKD 16
DN 16 KF
320015
Replacement element for OME 10/16, AKD 16
800160
Trap
Cold Trap KFG16 set:
Cold trap with cold finger, 500 mm metal hose,
centering ring and clamping ring
DN 16 KF
330055
Tubing
Metal hose
DN 16, 1 m
710764
Application
Kits
Freeze Dryer Adapter Kit
DN 16 KF
330031
Service
Service Kit
For
ROTILABO
®
CR-DS 40
S3344-99
Oil
Directorr™
Premium vacuum oil
1 liter
HKE3.1