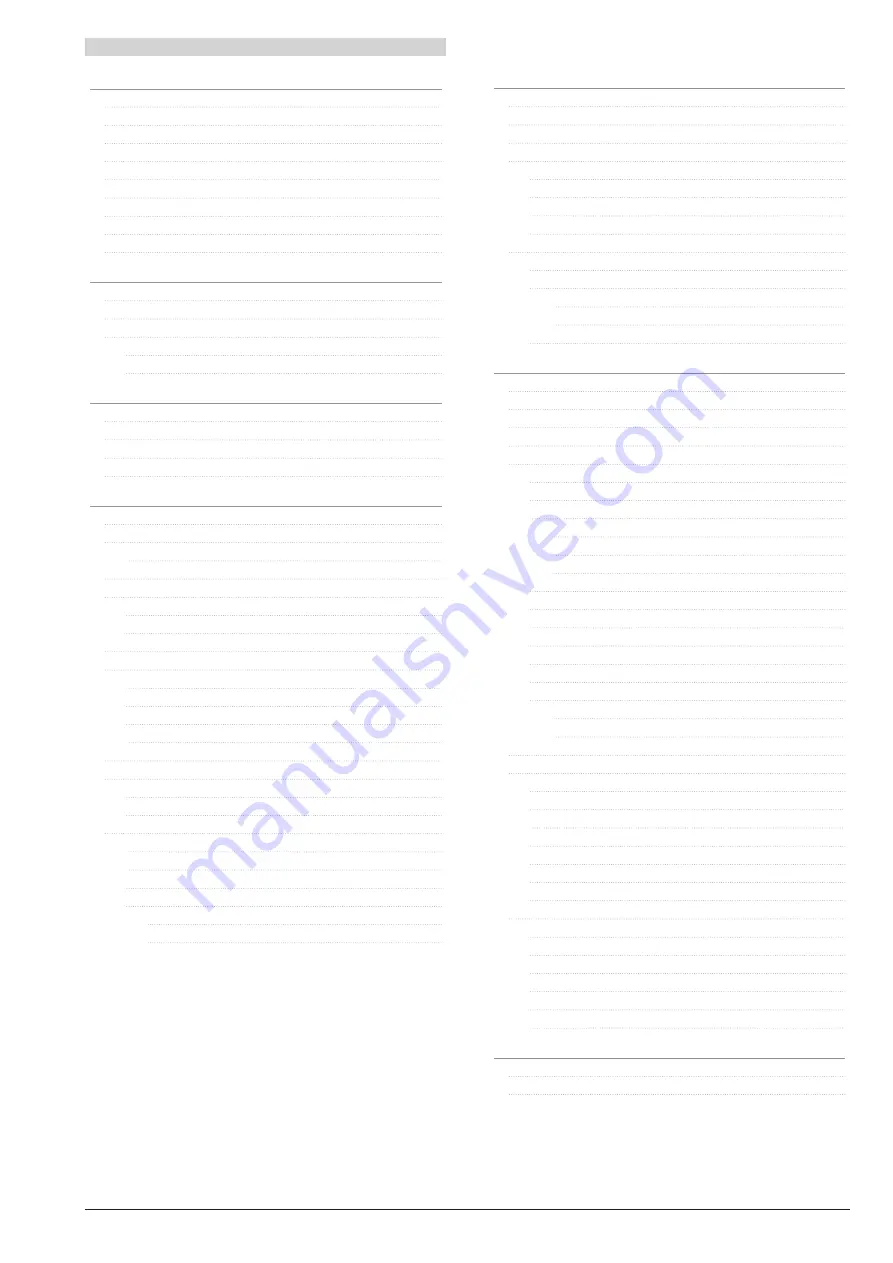
3
EN
Index
1. Safety Instructions
4
1.1. Equipment
4
1.2. Risks from noise development
4
1.3. Risks posed by moving parts
4
1.4. Risks posed by gas emissions
4
1.5. Risks posed by fuel
4
1.6. Risks posed by high temperatures
4
1.7. Risks posed by exhaust gas
4
1.8. Maintenance intervals
4
1.9. Disposal of toxic waste
4
2. Transportation and storage
5
2.1 Transportation for assembly
5
2.2. Storage as newdrive
5
2.3. Prolonged downtime/Storage
5
2.3.1. From 30 days to 6 months
5
2.3.2. Longer than 6 months
5
3. Specification
6
3.1. Technical data
6
3.2. Derating chart for operation under different conditions 7
3.3. Performance Curve
7
3.4. Flange and shaft dimensions
8
4. Installation
9
4.1. Preparation
9
4.2. State of installation site
9
4.2.1. In- and outtake Ventilation
9
4.3. Motor mounting
9
4.4. Exhaust gas system
9
4.4.1. Mounting the muffler
9
4.4.2. Information about other exhaust gas systems
9
4.5. Fuel System
9
4.6. Coupling
10
4.6.1. Maximum axial and radial load
10
4.6.2. Balancing
10
4.6.3. Direct coupling
10
4.6.4. Operating with a pulley
10
4.7. Concluding mechanical installation instructions
11
4.8. Speed controller
11
4.8.1. Type “A” – for variable speed
11
4.8.2. Type “C” – for constant speed
11
4.9. Electrical installation
11
4.9.1. Electrical connection (chords)
11
4.9.2. Starter battery
11
4.9.3. Circuit diagram of starter-dynamo
12
4.9.4. Oil-pressure sensor
12
4.9.4.1. Schematics of oil-pressure sensor-lamp
12
4.9.4.2. Oil-pressure sensor with magnetic valve
12
5. Usage
13
5.1. Components
13
5.2. Information about engine performance
13
5.3. Information about starter battery (optional)
13
5.4. Check-ups before every start-up
13
5.4.1. Engine oil
13
5.4.2. Fuel
14
5.4.3. Fuel system ventilation
14
5.4.4. Other check-ups
14
5.5. Start-up
14
5.5.1 Special information about initial start-up
14
5.5.2. Starting the engine
14
5.5.2.1. Hand start (all versions)
15
5.5.2.2. Electric start (only motor version “E”)
15
5.5.3 Stopping the engine
15
6. Maintenance
16
6.1. Instructions about maintenance
16
6.2. Precautions
16
6.3. Starter battery
16
6.4. Cleaning the crankcase
16
6.5 Upkeep
16
6.5.1 Changing the engine oil
16
6.5.2 Cleaning and exchanging the air filter
17
6.5.3. Fuel Supply
17
6.5.3.1. Changing the fuel filter
17
6.5.3.2. Ventilating the injection system
17
6.5.3.3. Examining, cleaning the injection nozzle
17
6.5.4. Proper timing/adjusting the valves
18
6.5.5. Governing behaviour
18
6.5.6. Muffler and colours of exhaust fumes
18
6.5.7. Other
18
6.5.8. General tightening torque
19
6.5.9. Engine torque and measured values
19
6.5.10. Solving electric issues
19
6.5.10.1 Starter malfunction
19
6.5.10.2. Battery does not charge
19
6.6. Maintenance intervals
20
6.7. Possible errors and their solutions
21
6.7.1. Engine does not start
21
6.7.2. Abnormal colour of exhaust gas
21
6.7.3. Low engine performance
22
6.7.4. Rough engine run
22
6.7.5. Engine overheating
22
6.7.6. Engine suddenly stopps
22
6.7.7. Abnormal running noise
22
6.8. List of parts/exploded assembly drawing
23
6.8.1. Crankcase
23
6.8.2. Cylinder head
24
6.8.3. Shafts
25
6.8.4. Fuel
25
6.8.5. Flywheel
26
6.8.6. Electrics
26
7. Appendix
27
7.1. Warranty conditions
27
7.2. Declaration of conformity
27