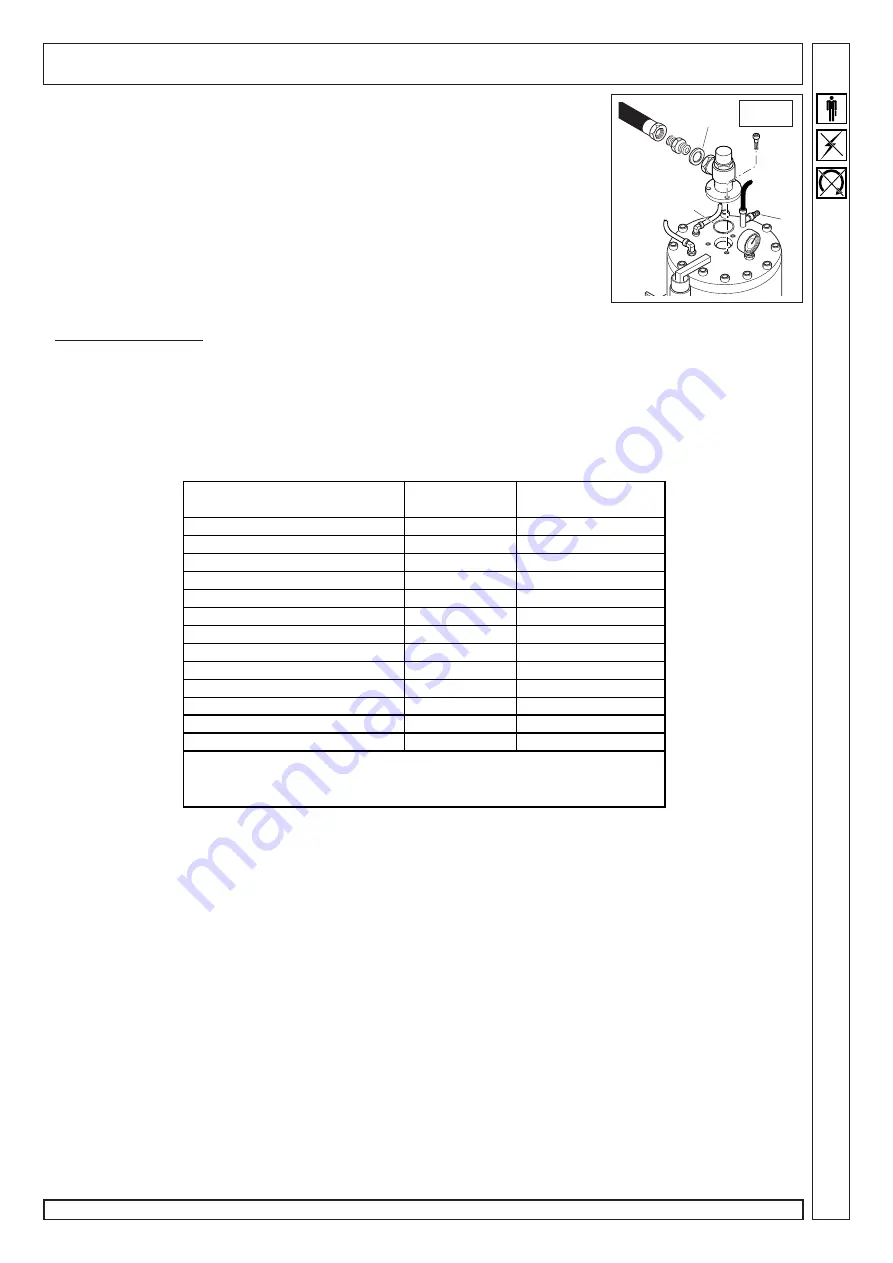
Rotar Giga 75-100 - Cod.197AA3900 - Rev.03 - 05/2007
GB
15
15
15
15
15
2
3
1
MAINTENANCE
13
EVERY 15,000 OPERATING HOURS
MIN. PRESSURE valve (fig.13)
Open door (F) (see fig.7) and bleed all air off the tank through the cock (1).
Replace gaskets (2) and (3)
.
SERVICE TABLE - WARNING
Oil is an essential factor. When using an oil type which is different from the recommended one - RotEnergy Plus - some service
intervals must be changed. Please refer to table.
In any case, a different oil MUST be used ONLY when oil is fully changed. NEVER MIX DIFFERENT TYPES OF OIL TOGETHER.
Never top up with a different type of oil.
EXHAUSTED OIL IS HIGHLY POLLUTANT! Dispose of exhausted oil in compliance with current laws.
Used oil
RotEnergy Plus
Different compatible oil
(see table)
Service description
Operating hours
Operating hours
Check and top up oil level
300
300
Clean intake filter and prefilter
500
500
Grease the electric motor bearings
4000
4000
Replace intake filter element
2000
2000
Replace oil filter
4000
4000
Replace oil separator filter
4000
4000
Change oil
8000
4000
Check driving belt tension
10000
10000
Check min. pressure valve
15000
15000
Replace driving belt
20000
20000
Replace compressor seal ring
20000
20000
Replace tank safety valve
20000
20000
Compatible oils: SHEEL Corena D46 - BP Energol HLP 46 - MOBIL D.T.E.
MEDIUM - AGIP Dicrea 46 - CASTROL Aircol MR46 - ESSO Univis 46 -
IP Veretum Oil 46 - FINA Eolan R046
Summary of Contents for Giga 100
Page 2: ......