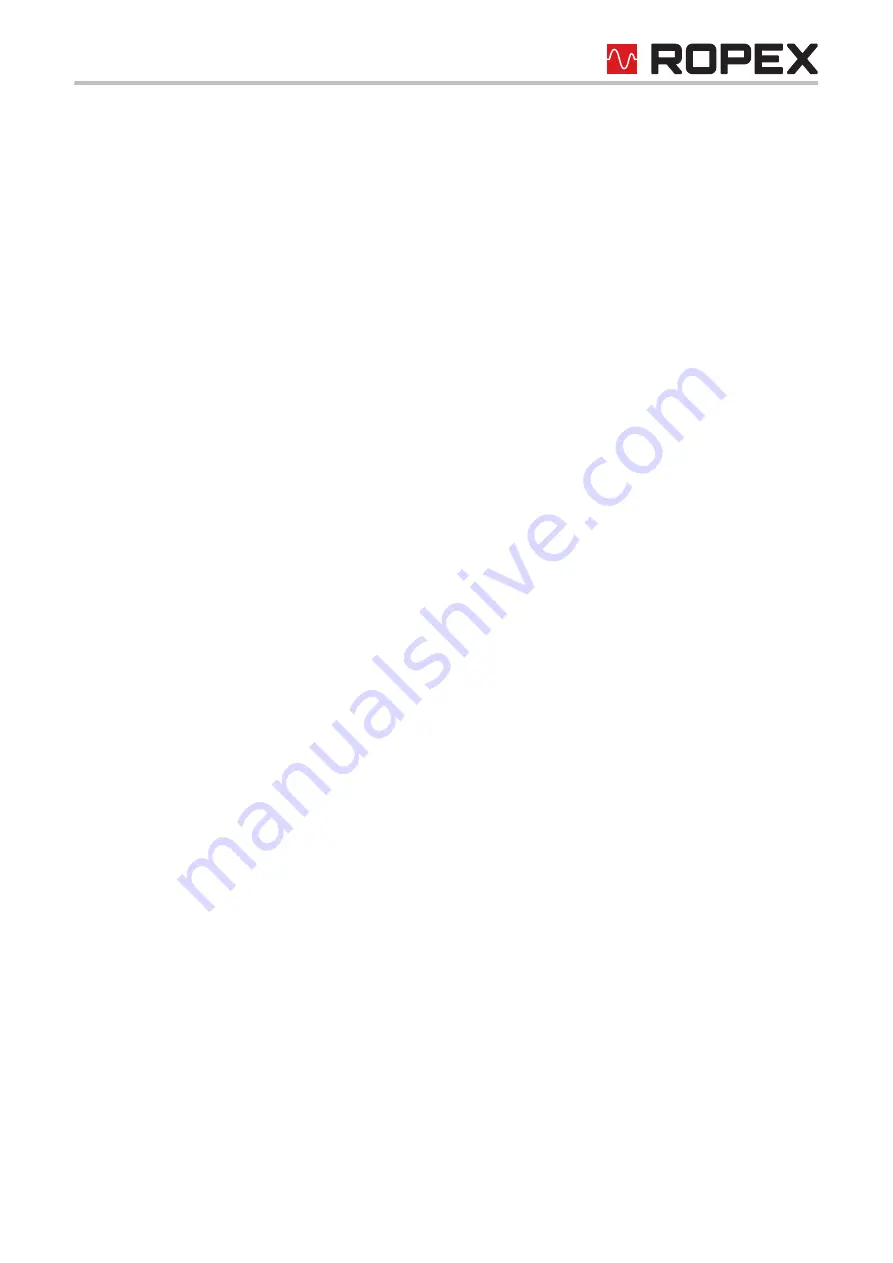
Functional principle
Version 2
RES-5011
Page 7
4
Functional principle
The resistance of the heating element, which changes with temperature, is measured by means of current and
voltage measurement, displayed and compared with the specified setpoint value. Measurements are made
50 times per second in a 50 Hz network, 60 times per second in a 60 Hz network.
The primary voltage of the impulse transformer is adjusted following the leading edge principle if the measured
values deviate from the setpoint value. The related current change in the heating element results in a rise in tem-
perature and change of resistance. The change in resistance is measured and evaluated by the RESISTRON
®
temperature controller. The temperature controller adjusts the control variables according to the change and the
set setpoint.
Even the smallest thermal loads on the heating element are recorded and can be quickly and precisely corrected.
Measurement of pure electric variables, together with the high measurement rate, result in a highly dynamic ther-
moelectric control circuit. The principle of primary-side transformer control proves to be especially advantageous
as it permits a very large secondary current range with low power loss. This permits an optimal adjustment to the
load and thus the desired dynamics with extremely compact device measurements.
5
Device features
The RESISTRON
®
temperature controller RES-5011 is equipped with a EtherNet/IP
TM
interface. Through this
interface, all functions and parameters can be parameterised by means of the higher level machine controller. In
addition, important controller information is queried and can be processed accordingly.
The ACTUAL temperature of the heating element is output through the EtherNet/IP
TM
interface and through an
analogue output 0…10 VDC. The real heating element temperature can be visualised on an external display
instrument (e.g. ATR-x) or via the operating unit of the machine controller.
The RES-5011 has an integrated error diagnosis that checks both the external system (heating element, wiring,
etc.) and the internal electronics. A differentiated error message is output through the EtherNet/IP
TM
interface in
case of malfunction.
To increase operational security and immunity to interference, all EtherNet/IP
TM
signals from the controller and
heating circuit are electrically isolated.
Adjustment for different heating element alloys (alloy A20, Vacodil, etc.) and setting of the temperature range to
be used (0…300 °C or 0…500 °C) can be made through coding switches on the temperature controller itself or
through the EtherNet/IP
TM
interface.
The compact design of the RESISTRON
®
temperature controller RES-5011 as well as the plug-in connecting ter-
minals make mounting and installation easier.
An overview of the most important features and functions:
• Easy calibration of the heating element through AUTOCAL, the automatic zero-point setting.
• Eight channels permit switching of the calibration parameters during tool change.
• High control dynamics through AUTOTUNE, automatic adjustment to the controlled system.
• High flexibility: The AUTORANGE function covers a secondary voltage range of 0.4 V to 120 V and a current
range of 30 A to 500 A.
• Automatic adjustment to the network frequency in the range of 47 Hz to 63 Hz.
• Wide voltage range for flexible use from 110 VAC to 415 VAC
• Easy and convenient system diagnosis and process visualisation through the free, downloadable software
ROPEXvisual®
• Comprehensive error diagnosis over the EtherNet/IP
TM
interface
• Booster output available for connecting a switching amplifier
• High process security through comprehensive options for evaluating the parameter data (e.g. temperature
diagnosis or heat-up time monitoring)