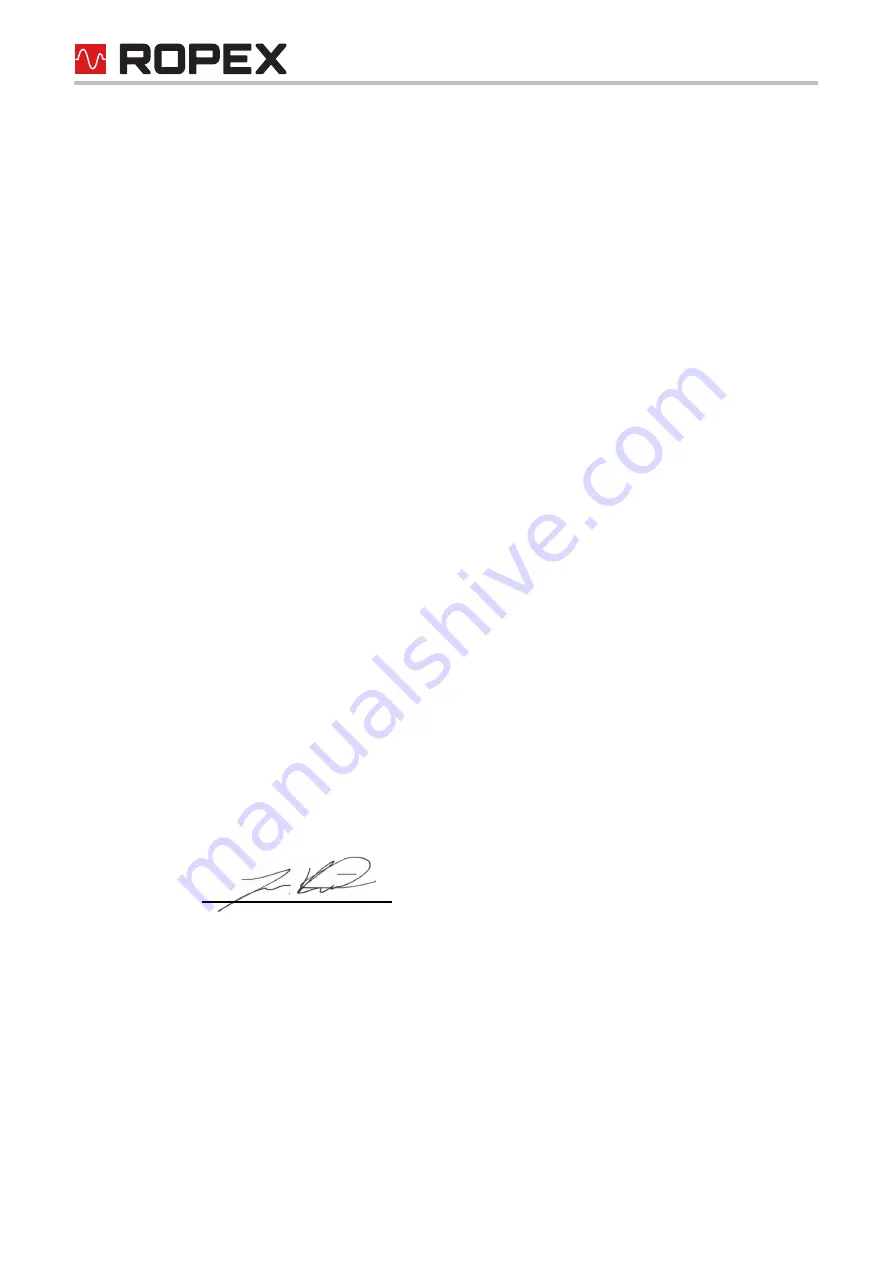
General information
Page 6
RES-403
Version 1
DECLARATION OF CONFORMITY
We hereby declare that the following device has been developed and manufactured in conformance with the direc-
tives cited below:
Compliant with following standards and directives:
Note:
This declaration of conformity certifies that the device/electronic itself complies with the above-mentioned direc-
tives. The CE mark on the device/electronic does not relieve the machinery manufacturer of his duty to verify the
conformity of the completely installed, wired and operationally ready system in the machine with the EMC directive.
Comments:
RESISTRON/CIRUS temperature controllers are not independently operable devices. They are used by the
machinery manufacturer to form a sealing system by adding EMC-relevant components such as filters, transfor-
mers, heatsealing bands and wiring. The final configuration may vary significantly in terms of performance and
physical dimensions. All information provided by us in connection with the line filter is merely intended as a guide
and is based on a typical measuring setup. It serves to demonstrate that compliance with the EMC directive can
be achieved by using a line filter that is suitable for the overall system. The line filter and current transformer must,
however, be determined on the basis of the respective application. We also wish to point out that the transformer
which is used must be designed in accordance with VDE 0551/EN 61558 or UL 5058 for safety reasons.
ROPEX Industrie-Elektronik GmbH
Adolf-Heim-Str. 4
74321 Bietigheim-Bissingen (Germany)
Designation:
RESISTRON temperature controller with accessories
Type:
RES-403 with line filter and current transformer
Operating principle:
Impulse sealing of films and plastics
EN 61010-1
Safety requirements for electrical equipment, control, and laboratory use
2014/35/EU
low voltage directive
2014/30/EU
electromagnetic compatibility directive
2011/65/EU
RoHS directive
July 12, 2020
J. Kühner (CEO)