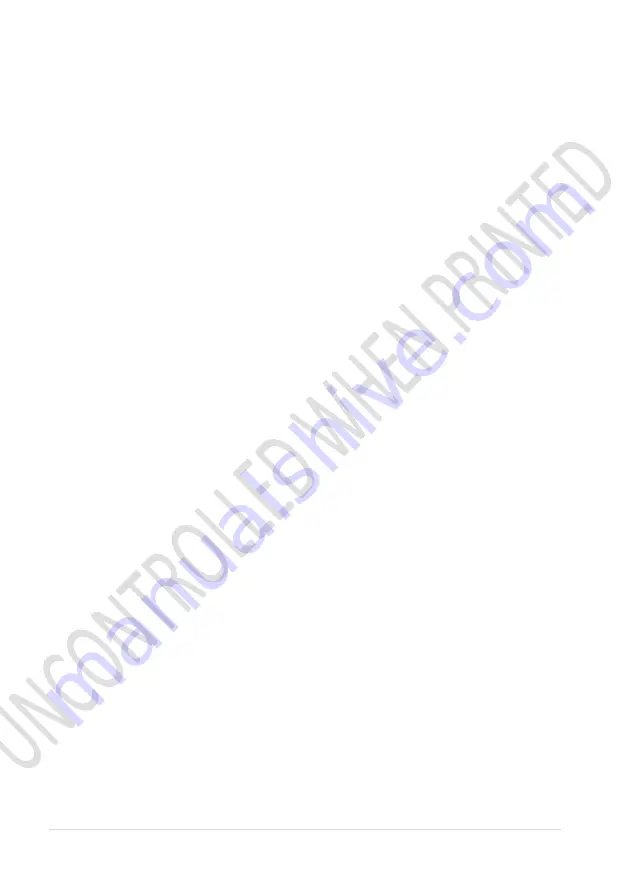
Operating and Maintenance Manual
16 |
P a g e
D e c a p p e r O & M M a n u a l R e v D
In some situations, the hose will have kinked when it is coiled in the box. The
hose can be re-shaped by plugging one end of the hose and filling the hose
with hot water and kneading the hose to re-shape the hose as required. After
the hose is straight and kinks removed drain the water and hang vertically to
cool for 1/2hr.
When not in use, the hose should be hung vertically from one end, or left in
a flat position to prevent kinks or bends in the hose. If this occurs repeat the
process above.
The placement of the cable tie on the drop tube end is required to prevent
cases in the hose catching on the end of the drop tube.
It’s a simple idea
,
but it does work.
In most cases, the end of the hose where it mounts on the drop tube is not
required to be secured, but can be secured if required, using cable ties or
hose clamps (not supplied).
➢
Processing Rates
The Decapper can process up to about 3,400 cases per hour when fully run
in (it varies slightly).
Typical rates from Dillon case feeders are between 1,500 to 4,500 cases per
hour depending on their condition and fill amount. Modified / upgraded case
feeder motors (variable speed) will perform significantly better and are
recommended for all Rollsizer.com machines. Aftermarket casefeeder plates
can also significantly improve the casefeeder performance.
❖
It is critical that you do not try to process cases through the
Decapper faster than the casefeeder can reliably supply.
❖
If you are getting jams due to cases not stabilizing in the
decapper pegs or falling over after decapping, Check the case
pusher adjustment in this manual first.