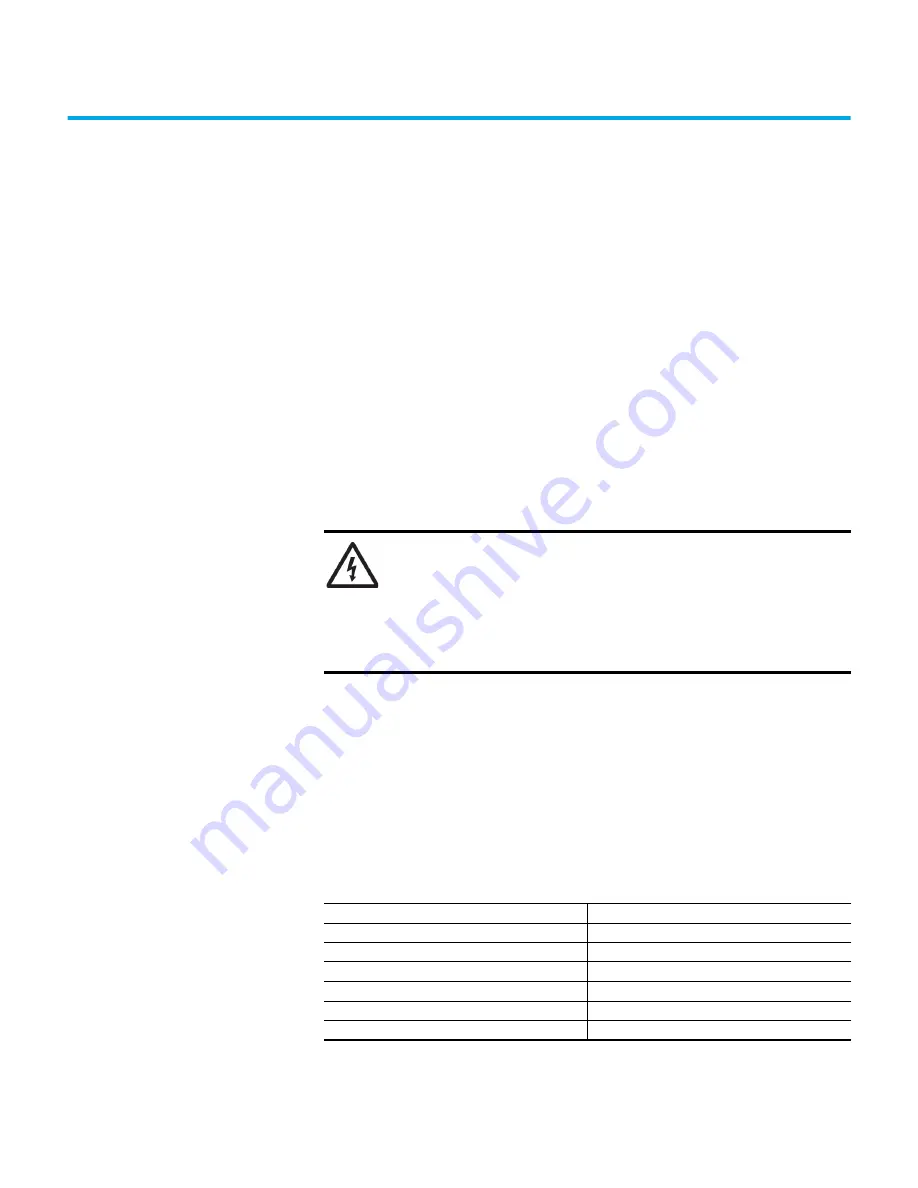
Rockwell Automation Publication 6000-UM002G-EN-P - August 2022
11
Chapter
1
Introduction
Around the world, Allen-Bradley® PowerFlex® medium voltage drives from
Rockwell Automation have built a reputation for providing efficient and
reliable motor control for industry's most demanding applications. From the
hardware designed to help optimize production to the power of networked
control platforms, users can quickly and easily gain access to valuable
information from their systems. Better information leads to higher asset
availability, reduced energy and maintenance costs, and asset and personnel
protection - all resulting in an increased return on your investment and real
bottom-line savings. No matter where your applications are located - and
whether your requirements are simple or complex, count on PowerFlex
medium voltage drives for the optimal solution.
Safety Considerations
Lockout and tagout the device feeding power to the input of the drive before
performing any drive maintenance or component replacements. After the
input device cabinet doors are opened, immediately test the outgoing power
cables feeding the drive with a live-line tool (hot stick) while wearing high-
voltage gloves. Repeat the live-line tool (hot stick) testing at the drive incoming
line power cable connections to verify that medium voltage is not present. Pay
special attention to any capacitors connected to medium voltage that can
retain a charge for a period of time. Only after the drive equipment has been
verified as isolated and de-energized can subsequent work be performed. Even
though the input to the drive may be open, it is still possible for hazardous
voltage to be present.
SHOCK HAZARD:
Energized industrial control equipment can be dangerous.
Severe injury or death can result from electrical shock, burn, or unintended
actuation of control equipment. Hazardous voltages may exist in the drive
cabinet even with the input circuit breaker in the off position. If it is
necessary to work in the vicinity of energized equipment, the safety-related
work practices that are outlined in Electrical Safety requirements for
Employee Work places must be followed. Before attempting any work, verify
that the system has been locked out and tested to have no potential.
Table 1 - Line-to-Ground Short-circuit Specifications
Attribute
Value
Line-to-Ground short-circuit current
31.5 kA
Incoming circuit breaker withstand current short time 4 s
Ik
≥
31.5 kA
Opening time
40...60 ms
Breaking time
50...75 ms
Inrush current
Inverter input current x 4 or Inverter input current x 5