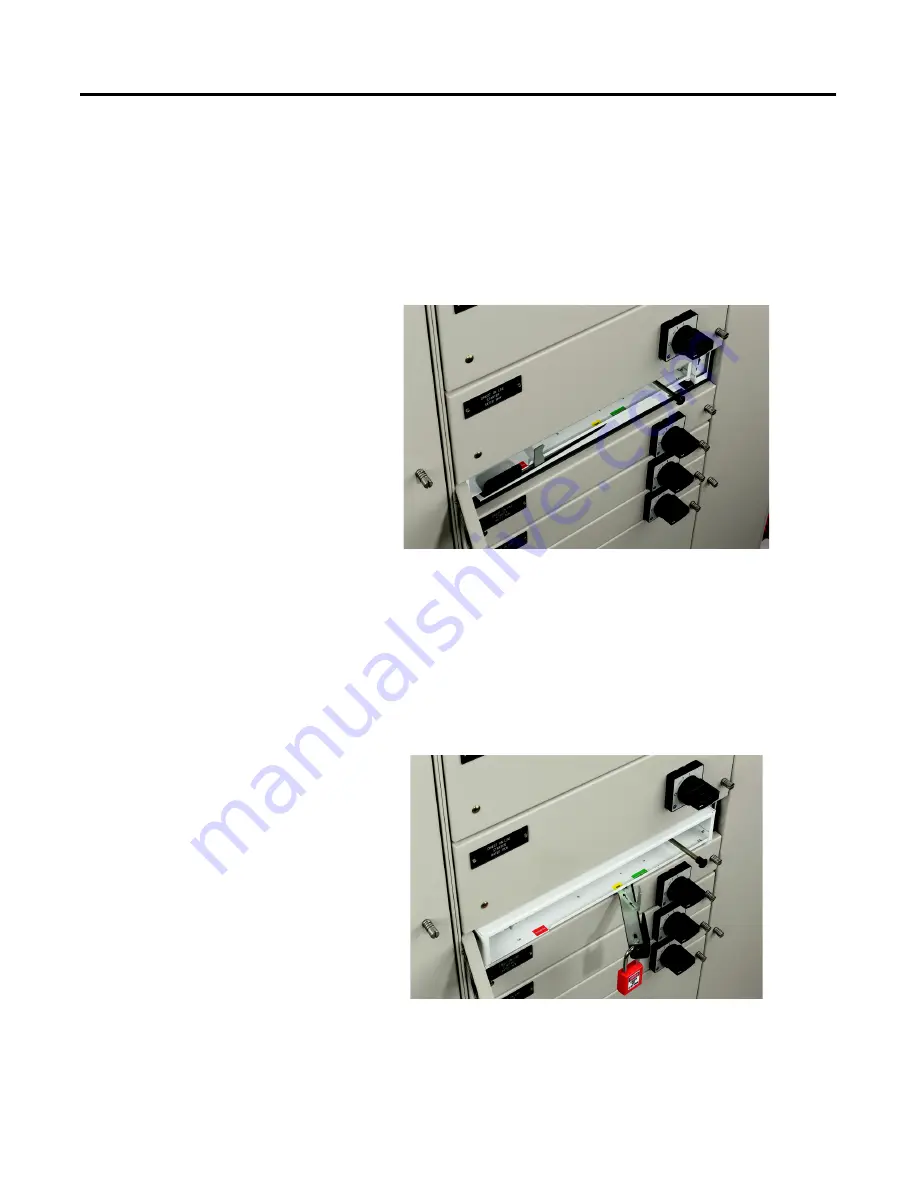
Publication 2500-IN001A-EN-P - May 2006
6-4
Unit Information
Connected
In the connected position, the line, load, control, network, and PE
connections are engaged. Closing the unit door helps ensure that the withdraw
lever is in the connected position. To engage the interlock or turn the branch
circuit device to the ON/I position, the unit door must be fully closed.
Figure 6.6 Connected Position
Test
In the test position, the control, network, and PE connections are engaged.
Line and load connections are isolated. This helps allow the control and
network wiring of the units to be verified. Units can be locked in this position.
Figure 6.7 Test Position (Locked)
Summary of Contents for Allen-Bradley CENTERLINE 2500
Page 1: ...CENTERLINE 2500 Low Voltage Motor Control Centers Instruction Manual...
Page 3: ...Instruction Manual CENTERLINE 2500 Motor Control Centers...
Page 4: ......
Page 10: ...Publication 2500 IN001A EN P May 2006 iv Notes...
Page 18: ...Publication 2500 IN001A EN P May 2006 1 8 General Information Notes...
Page 22: ...Publication 2500 IN001A EN P May 2006 2 4 Transporting Motor Control Centers Notes...
Page 52: ...Publication 2500 IN001A EN P May 2006 5 12 Commissioning Notes...
Page 82: ...Publication 2500 IN001A EN P May 2006 10 6 Maintenance Notes...
Page 84: ...Publication 2500 IN001A EN P May 2006 11 2 Maintenance After Fault Condition Notes...
Page 86: ...Publication 2500 IN001A EN P May 2006 12 2 Renewal Parts Notes...
Page 87: ......