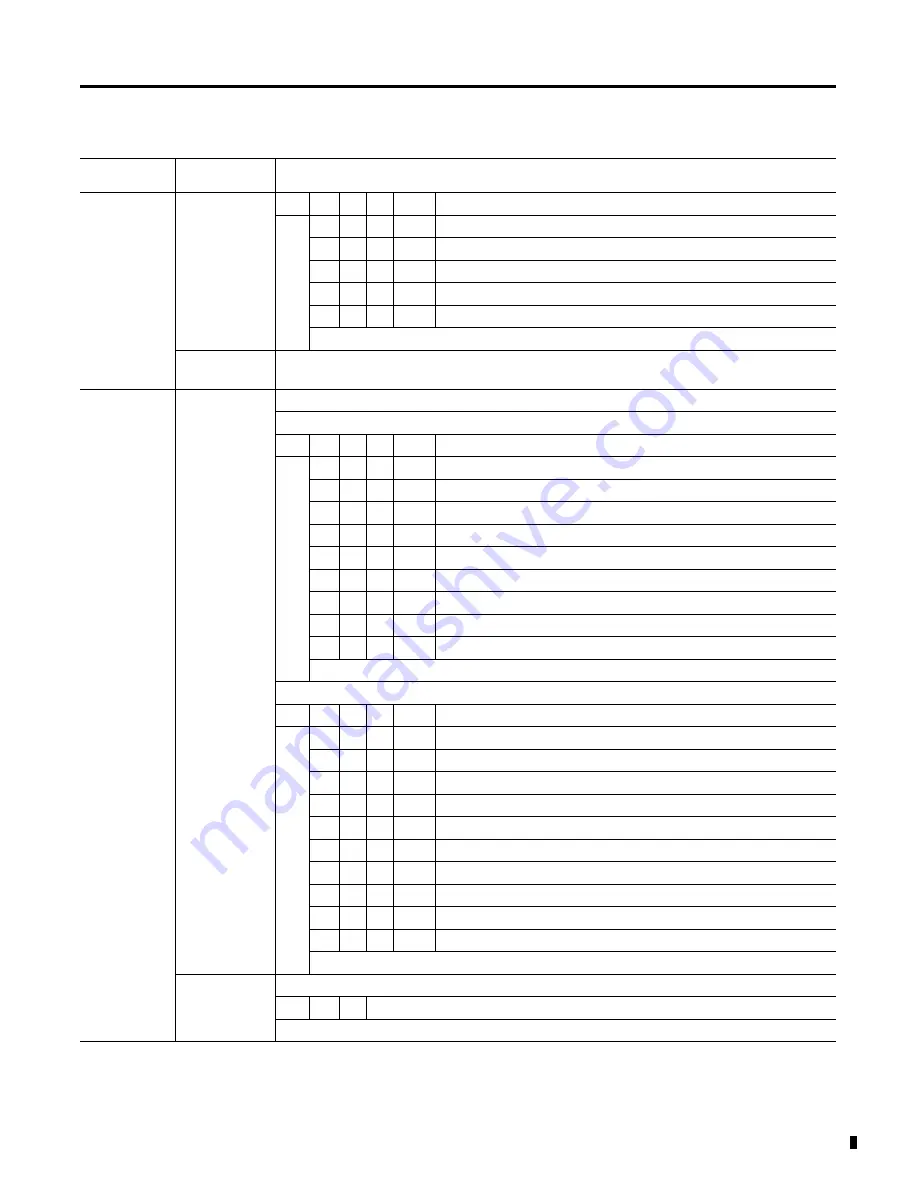
Publication 1794-6.5.12 - September 2011
Read and Write Configuration Maps for the FLEX I/O Module
35
Write Word 0
(continued)
Bits 08…11
(10…13)
Bit
11 10 09 08
Data type for channels 0…7
0
0
0
0
°C (implied decimal point xxxx.x)
0
0
0
1
°F (implied decimal point xxxx.x)
0
0
1
0
°K (implied decimal point xxxx.x)
0
0
1
1
-32767…+32767
0
1
0
0
0…65535
0101…1111 not used
Bits 12…15
(14…17)
Not used
Write Word 1
Bits 00…03
Sensor Type (Thermocouple or RTD)
RTD Type
Bit
03 02 01 00
Sensor type for channels 0…3
0
0
0
0
Resistance (default)
0
0
0
1
100
Ω
Pt
α
= 0.00385 Euro (-200…+870 °C) (-328…1598 °F)
0
0
1
0
200
Ω
Pt
α
= 0.00385 Euro (-200…+400 °C) (-328…752 °F)
0
0
1
1
100
Ω
Pt
α
= 0.003916 U.S. (-200…+630 °C) (-328…1166 °F)
0
1
0
0
200
Ω
Pt
α
= 0.003916 U.S. (-200…+400 °C) (-328…752 °F)
0
1
0
1
100
Ω
Nickel (-60…+250 °C) (-76…482 °F)
0
1
1
0
200
Ω
Nickel (-60…+200 °C) (-76…392 °F)
0
1
1
1
120
Ω
Nickel (-80…+320 °C) °F) (-112…608 °F)
1
0
0
0
10
Ω
Copper (-200…+260 °C) °F) (-328…500 °F)
1001…1111 not used
Thermocouple Type
Bit
03 02 01 00
Sensor type for channels 0…3
0
0
0
0
mV (default)
0
0
0
1
B 300…1800 °C (572…3272 °F)
0
0
1
0
E -270…1000 °C (-454…1832 °F)
0
0
1
1
J -210…1200 °C (-346…2192 °F)
0
1
0
0
K -270…1372 °C (-454…2502 °F)
0
1
0
1
TXK/XK(L) -200…800 °C (-328…1472 °F)
0
1
1
0
N -270…1300 °C (-450…2372 °F)
0
1
1
1
R -50…1768 °C (-58…3214 °F)
1
0
0
0
S -50…1768 °C (-58…3214 °F)
1
0
0
1
T -270…400 °C (-454…752 °F)
1010…1111 not used
Bits 04…05
Sensor Mode Select bits
Bit
05 04 Sensor mode select for channels 0…3
Thermocouple
Bit/Word Descriptions for Block Transfer Write Words
Word
Dec. Bits
(Octal Bits)
Description
Summary of Contents for Allen-Bradley 1794-IRT8K
Page 4: ...Publication 1794 6 5 12 September 2011 iv Summary of Changes Notes ...
Page 8: ...Publication 1794 6 5 12 EN E September 2011 viii Table of Contents Notes ...
Page 62: ...Publication 1794 6 5 12 September 2011 50 Calibrate Your Module Notes ...
Page 84: ...Publication 1794 6 5 12 September 2011 72 Index Notes ...
Page 85: ...Publication 1794 6 5 12 September 2011 Index 73 ...