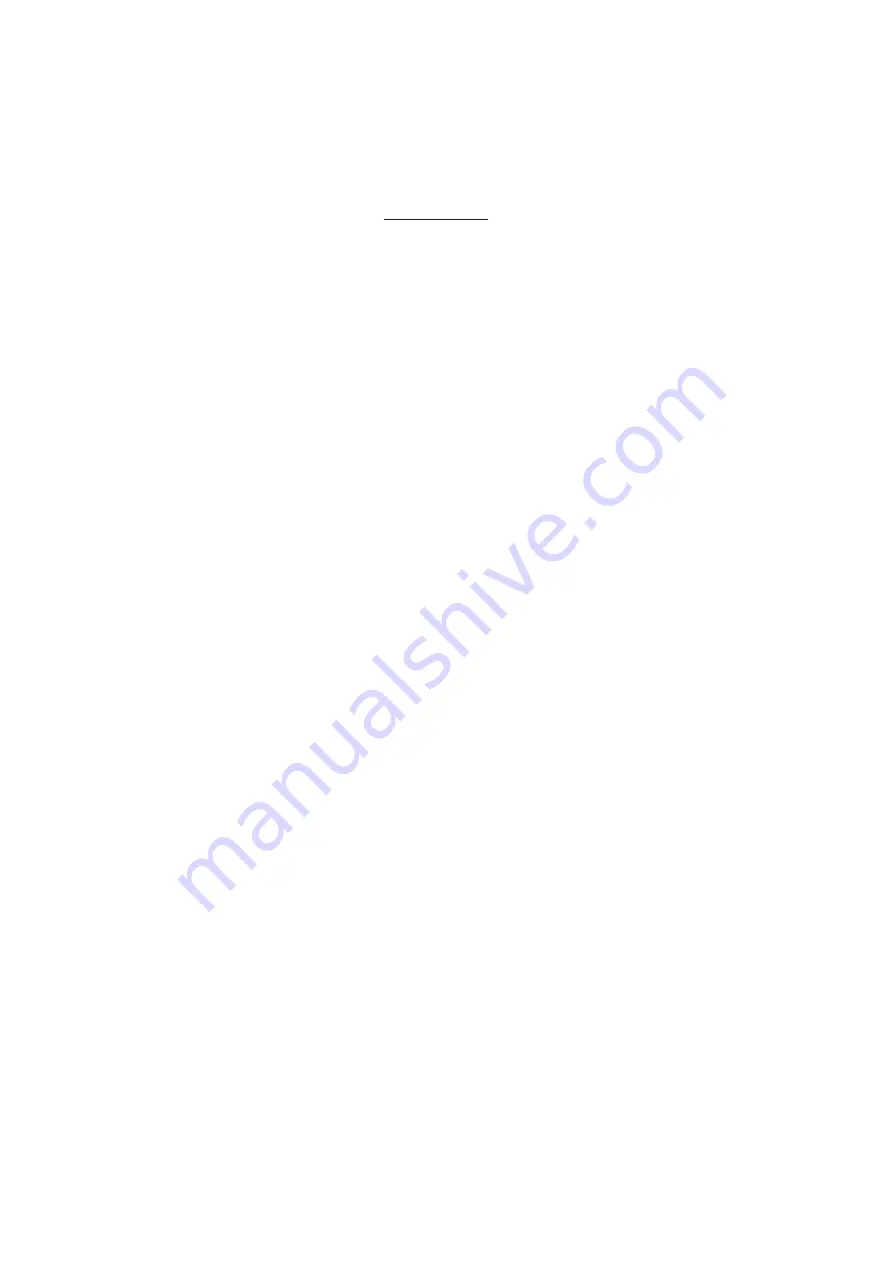
54
General information on the cycles
●
Before each operation, it is necessary to correctly set the X and Z axis zero points and check
the entered feedrate, XP and ZP values.
●
Before each operation, a release by START is necessary, also in the gearbox modes.
●
Each cycle can be aborted immediately by STOP. With a STOP the axes are moved to the
waiting position or to 0.0. If a complete stop is necessary, activate the EMERGENCY STOP
function! Only then will the axes stop
immediately and not move to a rest position.
●
For all cycles except „GRINDING“, the spindle must run before starting the operation!
●
You can also turn off the spindle during a cycle in progress, and after restarting the spindle,
the machining will continue. Please keep in mind that the tool can be damaged, especially
ceramic inserts often do not survive this undamaged.
●
Thread cutting is possible up to 1200 rpm, all other cycles run up to 3000 rpm (exceptions:
if the encoder on the spindle delivers different pulse rates than recommended)..
●
Automatic spindle stop: After the end of a cycle and in case of an emergency stop, the
SPINDLE STOP output is activated for the set duration (spindle stop switching duration), so
that, for example, the spindle drive can be switched off after the end of the cycle if an input
is available on the machine for this purpose.
SELECTION OF CUTTING PASSES
So that the tool or the material is not overloaded, cutting is usually carried out in several in-
feeds, we speak of „passages“. Before each pass, the cutting edge is driven into the material by
a certain amount in order to chip the material layer by layer.
The cutting depth during machining is called
a
p
, in the display we use
Ap
.
For rough roughing we use „Ap Rough“, for fine finishing we use „Ap Finish“, so that we know in
which direction this is meant we put the letter before it.
There are four values in the settings that influence the cutting depth: X Ap Rough, X Ap Finish
for cutting depths in X direction, Z Ap Rough and Z Ap Finish for Z direction.
Starting from the desired cutting depth, the control divides the individual depths per pass ac-
cording to these settingvalues. The division is carried out so that „X/Z Ap Rough“ is never ex
-
ceeded and is cut as a finishing pass with X/Z Ap Finish. Before the cut, the division is shown
on the display, the user can change the number of roughing passes from 1-99 with the rotary
knob, the depths are recalculated and displayed on-the-fly. As long as the number of cuts is
greater than 1, a finishing pass is always inserted.
Example: External turning, cutting depth should be 5.00 mm, set to X roughing Ap= 1.00 mm, X
finishing AP = 0.10 mm. 5x0.98 mm + 0.1 mm is offered for cutting.
The cut is therefore divided in such a way that the set 1.00 mm is not exceeded during roughing
but is used as well as possible, the last step being to cut the finishing pass with 0.10 mm.
Summary of Contents for ELS 4 Basic
Page 2: ......
Page 23: ...21 ...
Page 59: ...57 ...
Page 63: ...61 ...
Page 96: ...Zeroing is done as follows Possible grooves 94 ...