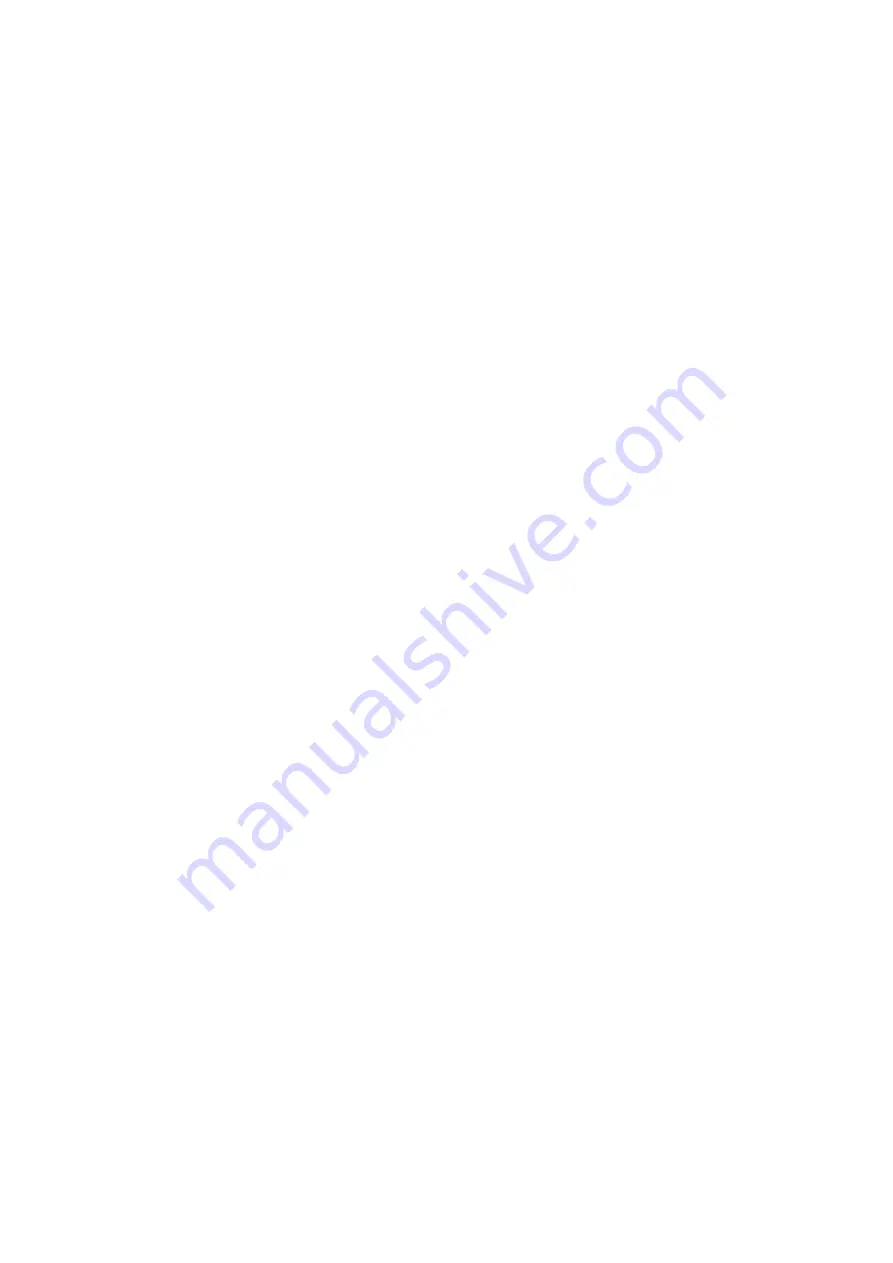
50
It is strongly recommended to connect the encoder 1:1 to the spindle, if this is not possible
then use straight ratios, 1:2, 1:4 e.g. Then select the number of pulses at the encoder accord
-
ingly, optimally 400 pulses arrive at the control per revolution afterwards. Avoid the use of gear
wheels, this will lead to problems.
Every controller is checked for correct function before delivery. A defect is therefore almost
impossible and does not manifest itself in inaccurate travel paths. Therefore, always check the
system carefully; experience has shown that the fault usually lies in the connection of the en-
coder or the motors.
If you have any problems, please feel free to contact us at [email protected] . It is best to
write down the setting values as well..
If the motors run correctly and the encoder provides correct values, the worst is already done,
now only the speeds and acceleration have to be adjusted:
5. Checking the stepper motor parameters
First the acceleration of the Z-motor:
1.
Stop the spindle
2.
Change to the settings and set the value for F rapid traverse of the Z stepper motor to a
value around 1000.
3. Move the Z-axis a few times to the left and right using the traverse keys.
4.
If you notice that the motor is blocking, you must try to adjust it using the acceleration and
rapid traverse values. If the motor blocks at the end of the acceleration ramp, it will spin too
fast. If it blocks at the beginning, the acceleration is too high. This requires a few passes, you
can switch to the settings at any time.
Then the values of the motor of the X axis:
Do the same for the X-axis, also move back and forth and adjust the values accordingly until
nothing blocks in rapid traverse.
6. Checking the route
1. Mount a caliper gauge or a dial gauge on the Z-axis so that its displacement can be meas
-
ured.
2.
Move the carriage manually in the direction of the chuck.
3. Set the Z axis to 0 by pressing the Z0 key.
4. Set the measuring instrument to 0
5. Set ZP to -50mm and move manually with < to the chuck until the control stops at -50mm.
6. The measuring instrument should now display 50mm.
Repeat this also for the X-axis.
Summary of Contents for ELS 4 Basic
Page 2: ......
Page 23: ...21 ...
Page 59: ...57 ...
Page 63: ...61 ...
Page 96: ...Zeroing is done as follows Possible grooves 94 ...