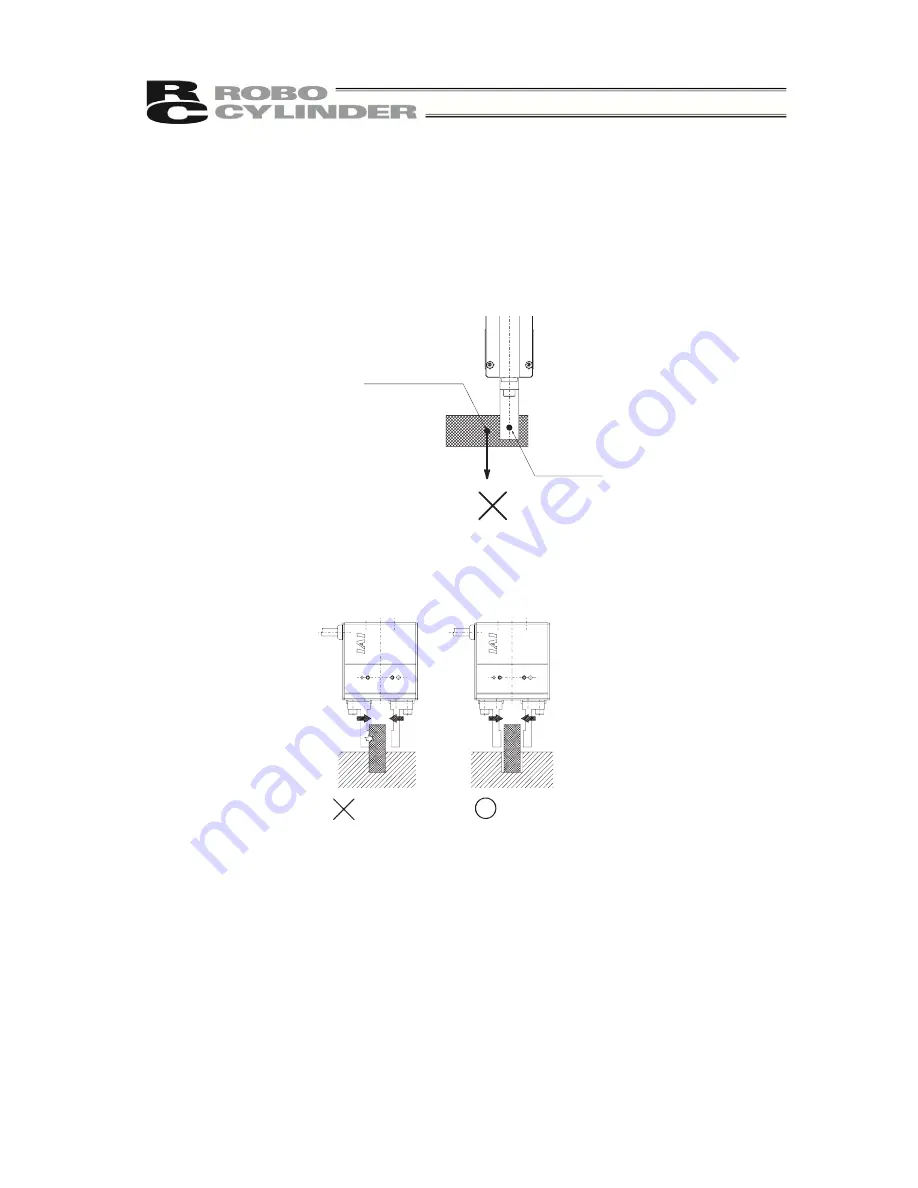
9
8. Make sure to follow the cautions listed below when transferring a work
piece.
If the fingers receive a strong force or impact other than the gripping force when transferring work
parts, the finger positions may deviate, looseness may occur or damage may result. Accordingly,
pay due attention to the points listed below.
¡
Cause the center of gravity of the work part to match the gripping point as much as possible. If
the two are not aligned, gravitational moments will force the work part to assume an unstable
posture.
Center of gravity of
the work part
Gripping point
Unstable
¡
While being gripped, the work part should have play (clearance) in the gripping direction. Also
perform thorough alignment and avoid using the gripper in a manner where loads concentrate
on one finger alone when a work part is gripped.
No clearance is
available. Loads are
received unevenly.
Clearance is available.
Summary of Contents for GR3LM
Page 2: ......
Page 4: ......
Page 71: ...2 Installation 65 4 GRHM Shaft bracket Flange bracket 5 GRHB Flange bracket Shaft bracket ...
Page 74: ...2 Installation 68 depth 8 depth 8 GRS GRM ...
Page 77: ...2 Installation 71 depth 5 depth 6 φ φ GR3SS GR3SM ...
Page 78: ...2 Installation 72 GR3LS GR3LM ...
Page 127: ......