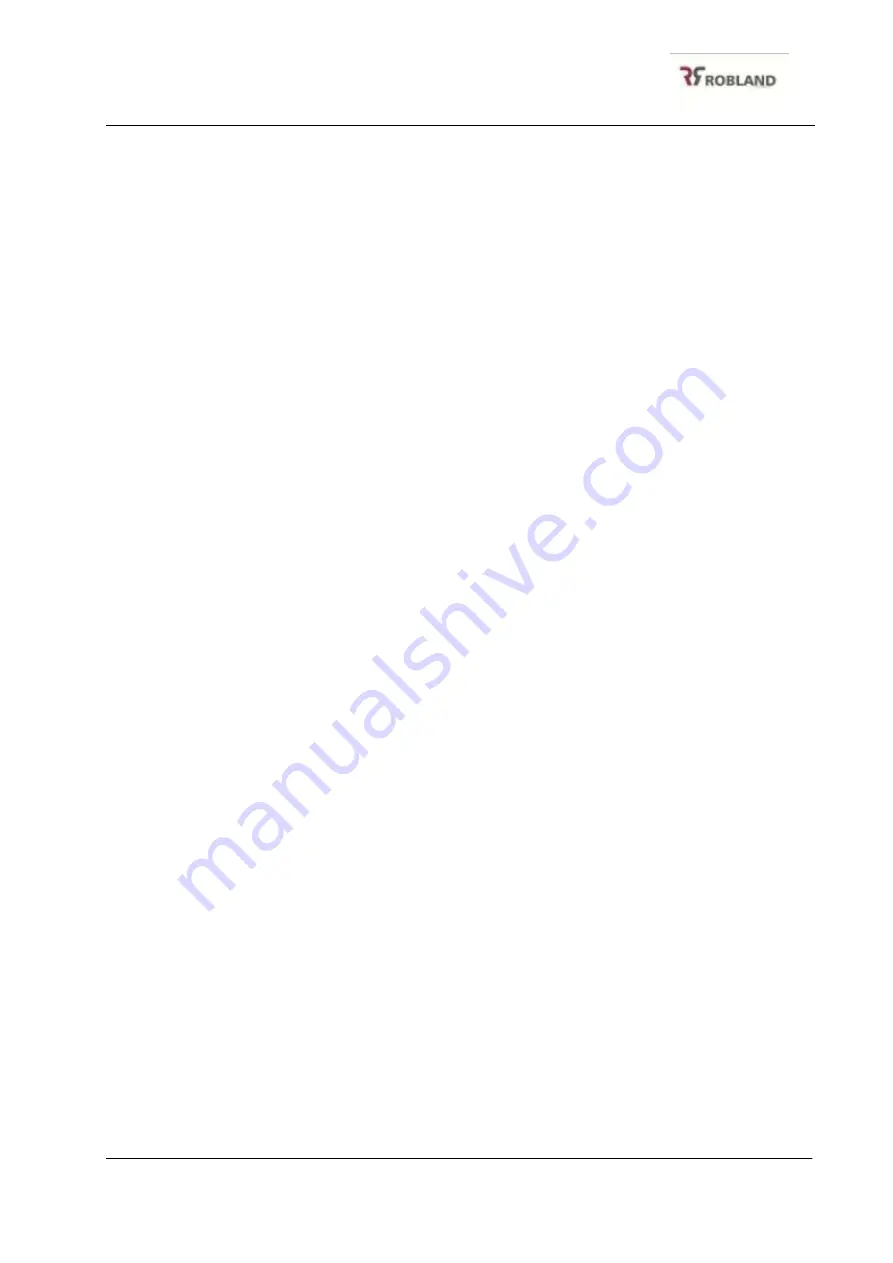
Instructions manual KM 775 - 785
26
6 MAINTENANCE:
THE MACHINE MUST BE FULLY DISCONNECTED BOTH ELECTRICALLY
AND PNEUMATICALLY BEFORE UNDERTAKING EITHER ROUTINE OR
SPECIAL MAINTENANCE WORK.
THIS PROCESS SHOULD BE CARRY OUT BY WELL EDUCATED WORKER.
6.1 Routine maintenance:
The maintenance below is carried out daily before running the machine, and
consists of:
Before starting the machine, check that there is nothing obstructing movement of
the station and motors that could lead to damage or personal injury.
Check that pressures are correct.
Make sure that all micros (the rods) are correctly positioned (vertically, waiting to
contact the work piece), that they are firmly tightened and that they move as they
should.
These maintenance points are carried out at the close of each working day:
Clean the work zone.
Make sure that the main supply cable shows no signs of cuts or burning.
Check the condition of cutters and tracers.
Check the oil level in the air service unit lubricator reservoir.
6.2 Special maintenance:
This maintenance is carried out weekly:
Carry out all routine maintenance operations.
Check the safety of the electrical installation.
Check locking of mechanical components.
Examine cable insulation, operation of devices and continuity of protective
conductor.
Check the cutters for wear.
Clean the chain wheels and rubbers with a cloth dampened with neutral solvent
(that damages neither silicon nor rubber). Do this after lifting the presser, having
completely stopped the machine.
Use a little machine oil (SAE-10) and a cloth to clean the tracer bearings, then dry
off and apply a thin film of grease.
Check the condition and tension of the transmission pulleys inside the cabinet
under the tray and glue pot.
Transmission set: This refers to all the equipment under the glue pot whose
function is the synchronised transmission of chain movement to the glue roller,
band feed system and first press roller.
Belt condition and tension needs periodic checking. The flat belt is tensioned by
simply loosening the fixing screws and moving the angle bevel box to achieve the
required tensioning.
Summary of Contents for KM 775
Page 1: ...i INSTRUCTIONS MANUAL EDGE BANDING MACHINE OF HOT MELT GLUE Model KM 775 785 Document Rev 1 ...
Page 2: ...Instructions manual KM 775 785 ii ...
Page 4: ...Instructions manual KM 775 785 iv ...
Page 40: ...Instructions manual KM 775 785 33 ...
Page 41: ...Instructions manual KM 775 785 34 FEEDING STATION REFERENCE 560 20 01N CUTTER FEEDING ...
Page 44: ...Instructions manual KM 775 785 37 SPARE PARTS DRIVE GEAR BOX 0600400A ...
Page 46: ...Instructions manual KM 775 785 39 SPARE PARTS ANGULAR GEAR BOX 0510600A ...
Page 48: ...Instructions manual KM 775 785 41 ...
Page 49: ...Instructions manual KM 775 785 42 ...
Page 50: ...Instructions manual KM 775 785 43 ...
Page 51: ...Instructions manual KM 775 785 44 SPARE PARTS INFEED TABLE 912 02 00 P ...
Page 52: ...Instructions manual KM 775 785 45 ...
Page 53: ...Instructions manual KM 775 785 46 SPARE PARTS GLUE POT 070 05 00 ...
Page 54: ...Instructions manual KM 775 785 47 ...
Page 55: ...Instructions manual KM 775 785 48 ...
Page 57: ...Instructions manual KM 775 785 50 ...
Page 59: ...Instructions manual KM 775 785 52 SPARE PARTS END TRIM STATION 0620600 V 7 ...
Page 60: ...Instructions manual KM 775 785 53 SPARE PARTS TOP TRIMMING STATION JC 5 ...
Page 61: ...Instructions manual KM 775 785 54 SPARE PARTS TOP TRIMMING STATION 0700700SUP ...
Page 62: ...Instructions manual KM 775 785 55 SPARE PARTS BOTTOM TRIMMING STATION JC 5 ...
Page 63: ...Instructions manual KM 775 785 56 SPARE PARTS BOTTOM TRIMMING STATION 0700700SDW ...
Page 65: ...Instructions manual KM 775 785 58 ...
Page 67: ...Instructions manual KM 775 785 60 S PA RE PA RT S FL AT SC RA PE R UN IT RR 7 ...
Page 69: ...Instructions manual KM 775 785 62 SPARE PARTS POLISHER STATION 0601300R ...