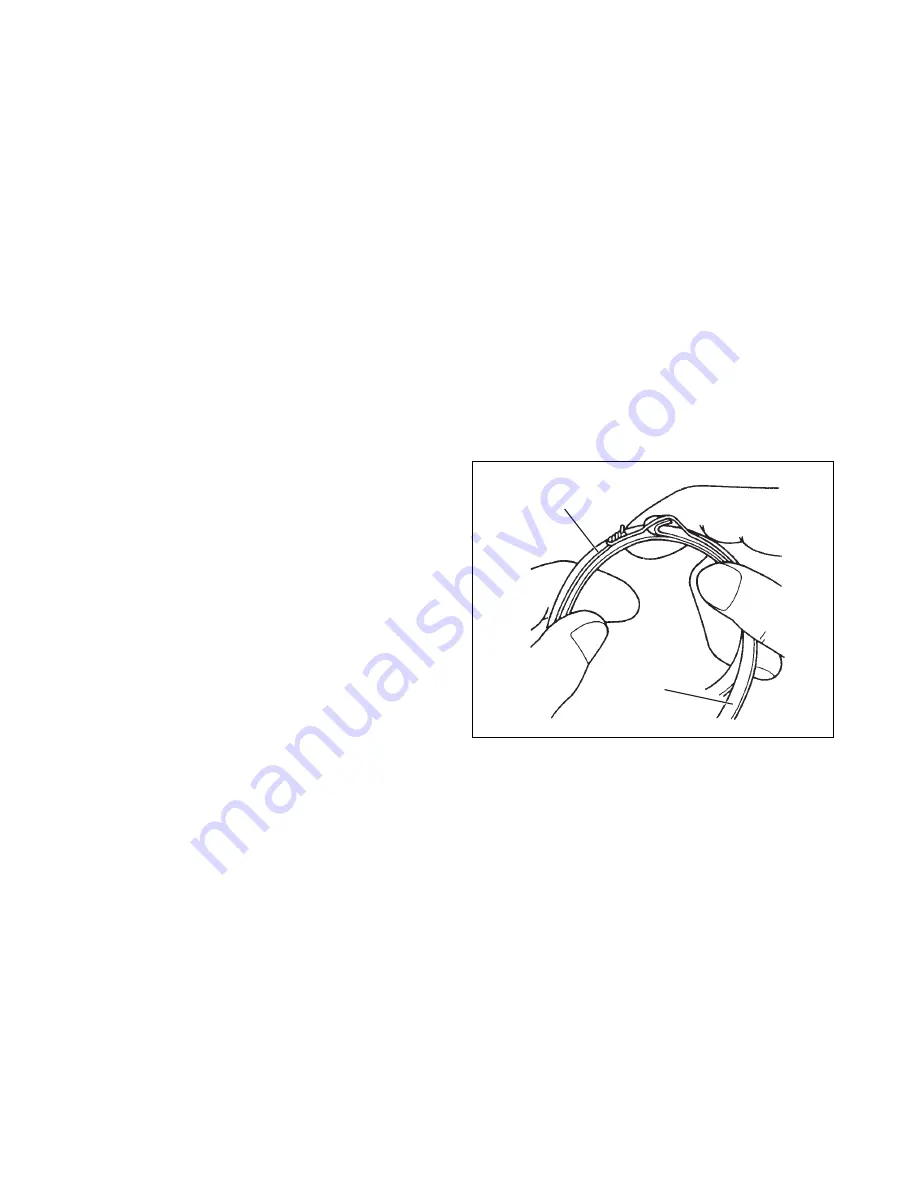
- 50 -
9-3 CHECK AFTER REASSEMBLE
(1) Pull the starter knob a few times to check if:
A. The starter knob is too heavy to pull, check that each part has been assembled as specified.
B. The ratchet fails to function, check is parts such as friction spring have been missing.
(2) Pull out the starter knob to extend the rope to its extreme to see if:
A. The starter rope still remains in the rope slot of the reel, unwind the rope by 1 to 2 turns as shown
in Fig. 9-1, as the spring may be over-stressed.
B. The starter rope is found weak to recoil or droops in halfway, apply grease or mobile oil to the
rotating part and to the friction parts. If it persists, wind-up the spring by 1 to 2 turns. (In this case,
check that the spring is not over-stressed.)
C. The spring escapes with a sound and the starter rope fails to spring back to its original position,
reassemble the starter from the beginning.
9-4 OTHER GUIDES
(1) When the spring escapes from the reel :
Make a ring having a rather small diameter
than spring housing using a thin wire.
Hook the outer end of the spring onto a part of
the ring and re-wind the spring into the wire
ring as shown in Fig.9-6 then put it into the
housing.
Remove the ring slowly while holding down
the spring to avoid getting out of place.
The ring can easily be removed by prying it
with the tip of a screwdriver.
Refer to Fig.9-4 for which way the spiral spring
must be placed.
(2) When it is lubricated :
Lubricate the starter shaft and spring with a
grease (If possible, heat-resistant type is pref-
erable) or a mobile oil when the starter is be-
ing disassembled and prior to long-term stor-
age.
(3) When the swing arm does not move smoothly:
Apply grease (Alevin No. 3) or mobile oil on it.
Fig. 9-6
SPRING
WIRE RING