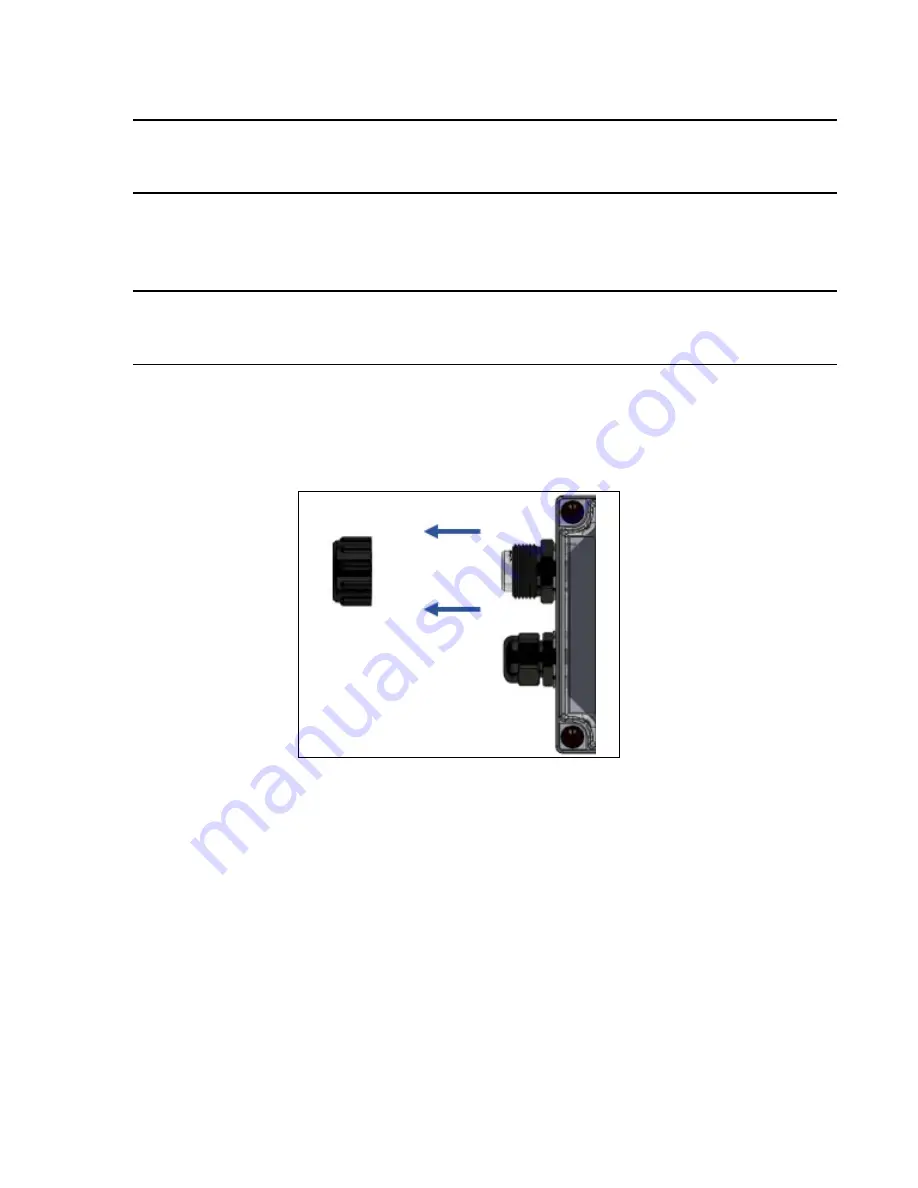
AirLink 6940XP Operator’s Manual
Maintenance
•
70
Replacing the Sensor
WARNING: Do not remove the sensor housing cap or enclosure lid while the circuits are
energized unless the area is determined to be non-hazardous. Keep the sensor
housing cap and enclosure lid tightly closed during operation.
RKI recommends replacing the sensor element whenever a slow response to gas is observed
during the normal calibration process. After replacing the sensor element, the device MUST be
zeroed and calibrated for proper operation of the device.
CAUTION:
Do not remove the sensor housing cap or enclosure lid while the circuits are
energized unless the area is determined to be non-hazardous. Keep the sensor
housing cap and enclosure lid tightly closed during operation.
1. Press and hold
SUB
for approximately 6 seconds until “OFF” shows on the display screen.
2. Unscrew the rain guard.
3. Unscrew and remove the sensor housing cap from the sensor housing base. Set aside.