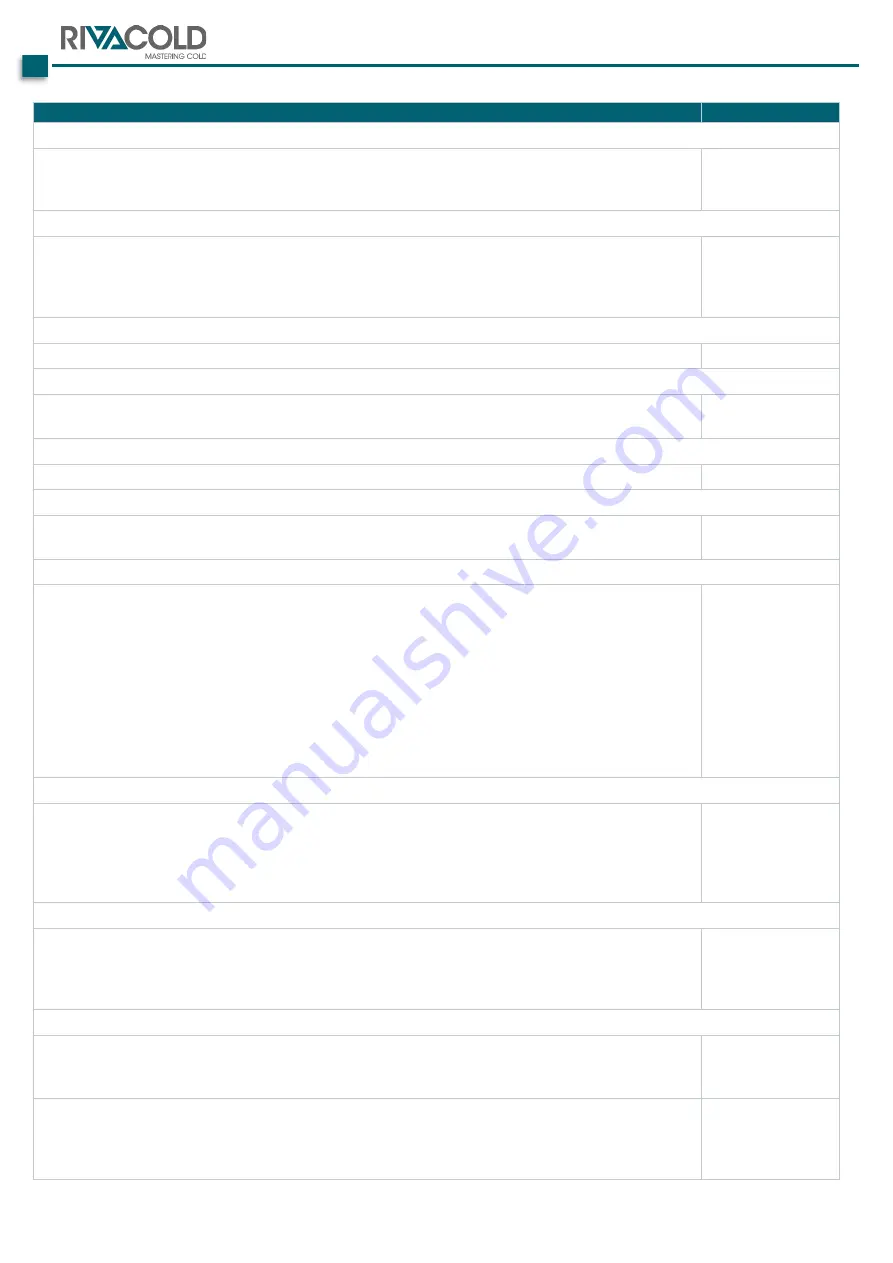
CO
2
NNEXT
rev.01
EN
112 / 293
DESCRIPTION OF THE MAINTENANCE
FREQUENCY
Controls and safety devices checks
Proceed with verification of the operation of all the safety control devices by checking
the anomalies signalled by the electronic control, which detects probe faults and
anomalies of the same. Refer to the dedicated manual.
Monthly
Check for the presence of oil on the separators (if any)
Check that there are no oil alarms on the electronic control and that the level on the
separators is higher than the minimum as indicated by the sensor. In the event that the
level is low before adding oil, wait a day and check for any alarms. In the presence of
alarms, add oil to the minimum level and check over the following days.
Monthly
Check of non-return valves for compressors (if any)
Check the tightness of the non-return valves on each compressor outlet.
Monthly
Cleaning of the compressor body
Perform regular cleaning of the external surfaces of the electric motor of the compressor
to prevent the accumulation of dust deposits.
Monthly
Air extraction fans (if present)
Check correct operation of the air extraction fan.
Quarterly
Check the status of electrical contacts
Clean the contacts, fixed and mobile, of all the contactors, replacing them if they show
signs of deterioration.
Quarterly
Refrigerant humidity control
Check the regular flow of the refrigerant in the sight glass on the IND1 liquid line and
carefully examine the colour of the moisture-sensitive element through the sight glass. The
green colour indicates dry, the yellow colour indicates humidity. In case of humidity
indication, immediately stop the partly-completed machine replacing the gas only after
having carried out the drain procedure again. It may also be necessary to replace the
filter on liquid FL1, which is installed by brazing. Replacement is possible by closing the R4
and R5 valves upstream and downstream of the filter itself. The RS3 service valve will allow
the refrigerant to be removed as well as the subsequent pressure test operations, gas
drain and preload up to 10 bar.
Quarterly
Compressor noise check
The control operations must be performed in the absence of unauthorised personnel and
with instruments suitable for the type of operation. The instruments must be positioned
with the machine switched off and, if inside the machine, all the protections removed
must be repositioned. The presence of clicks or vibrations may be a sign of breakage or
excessive mechanical clearance between moving parts.
Quarterly
Checking of HPV high pressure and VFL gas flash electronic valves
Clean the internal filter (if present) and the internal mechanisms of the HPV and VFL
electronic valves after having collected all the gas inside the liquid receivers using the
shut-off valves in the machine and the service valves for the operations of discharge and
of subsequent drainage.
Annual
Replacing HPV high pressure and VFL gas flash electronic valves
Replace the internal mechanisms of the HPV and VFL electronic valves using the shut-off
valves in the machine and using the service valves for the operations of discharge and
subsequent draining.
Five-yearly
Periodically clean the gascooler/capacitor removing dust and grease. If the environment
where the unit is installed is very dusty, it may be necessary to clean the machine more
frequently. For cleaning use a compressed air gun or, alternatively, an aspirator.
Monthly
Table 6 - Maintenance frequency