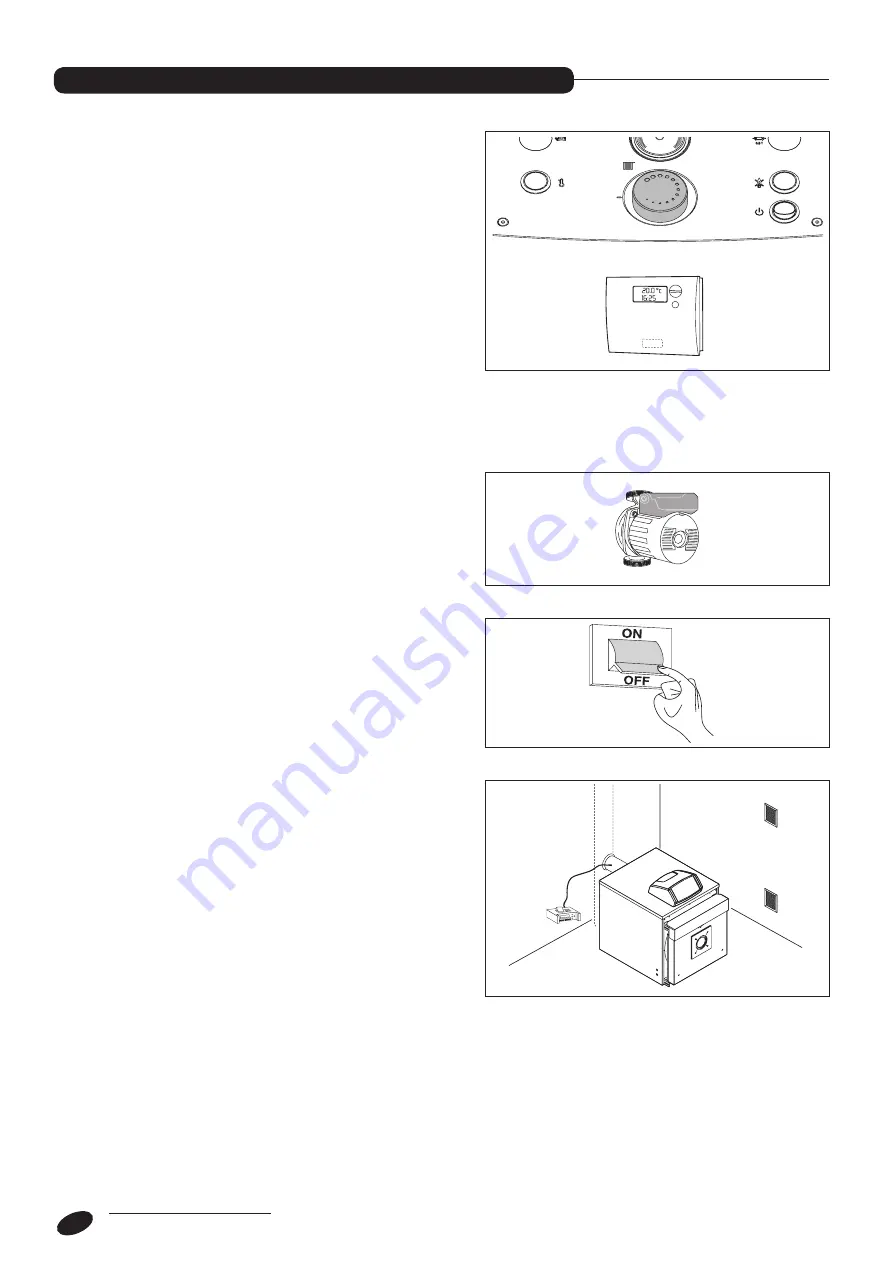
TECHNICAL ASSISTANCE SERVICE
28
Once the boiler has started up, make sure that it shuts
down and re-starts properly when the following actions
are taken:
- The boiler thermostat setting is changed
- Power to the control panel is switched off and on again
- The room thermostat or timer thermostat is adjusted.
Check that there are no leaks from around the door seal.
If there is any leakage of combustion gases, adjust the
door as instructed on page 29.
Make sure that all the pumps in the system are free and
rotate in the right direction.
Turn off the main power switch to the boiler and make
sure that the boiler shuts down properly.
Provided all the above conditions are satisfied, start the
boiler up again, then analyse the combustion fumes,
measure fuel flow and re-check the door seal.
CHECKS DURING AND AFTER INITIAL START-UP
20
40
60
80
100
0
120