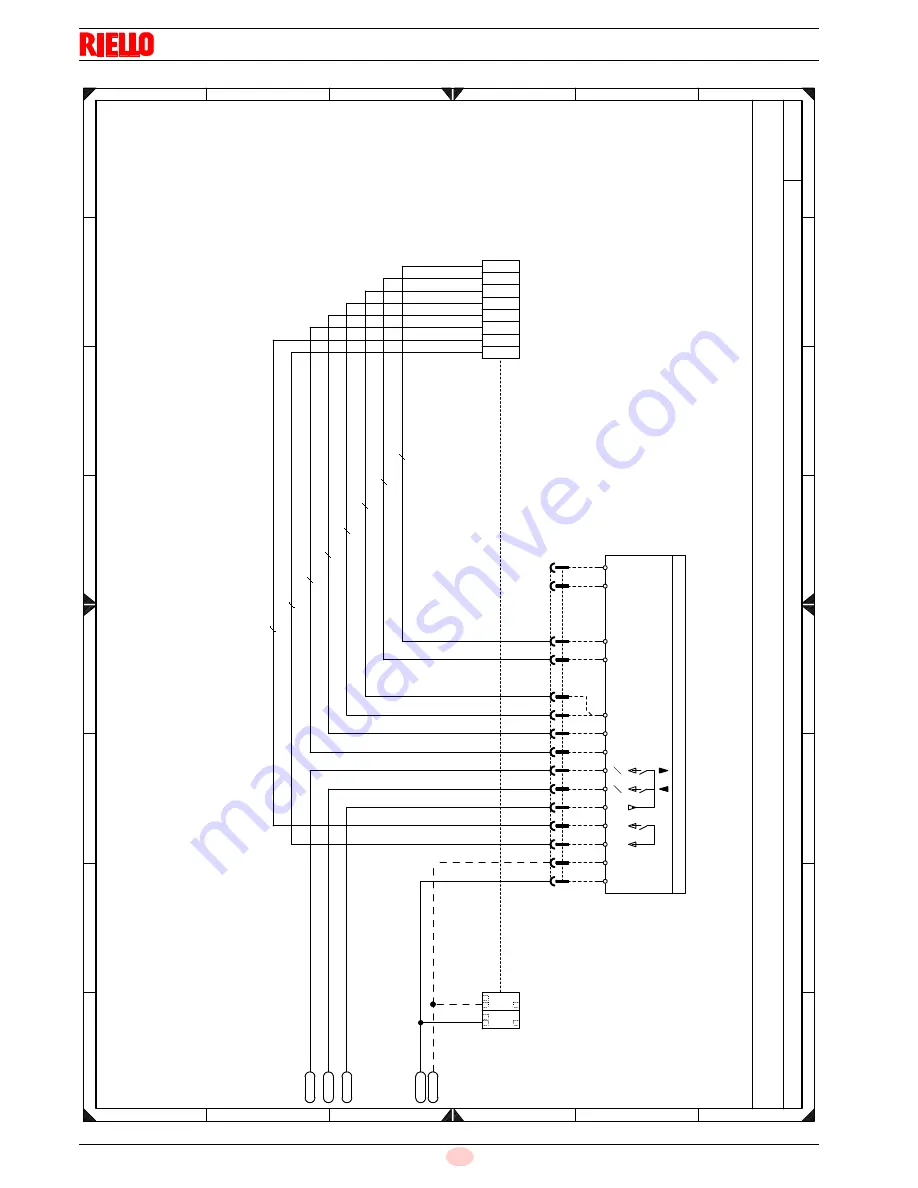
20081753
72
GB
Appendix - Electrical panel layout
!"##$%%&
'()
'(*)
'+)
)
,
-
.
/
0
1
)
,
-
.
/
0
1
2
+
3
4
5
6
2
+
3
4
5
6
789%:5;<=29<:5%48%*<95>?2%:@6/AB,
:@6/AB,%<C9*C9%*<@5:%:5;C=29<:%789
789%=58!9C>;!:5;=5:%:@6/AB,
789%:5;C=295C:%45%*C8!!2>35%:@6/AB,
0A-
D0B3
0A,
D0B3
0AA
D0B4
)=
D0B4
>
D0B4
)=
>
)
'E+
:@6%/ABBB
,
-
.
/
0
1
F
)A
))
),
)-
A.
A-
).
A
)/
AF
)A
))
),
)-
G)-
G).
8)
E)
;)H
C)
;H
;'
+C%I%+=C%D%+=C5%D%+=5C%D%+=2C
+7%I%>5:<%D%+=237%D%><8:%D%!3J@2:?
K5%I%;82==<%D%K5==<@%D%L2C>5%D%;5=+
;>%I%M5:45%D%;:55>%D%M5:9%D%;:N>
:4%I%:<!!<%D%:54%D%:<C;5%D%:<9
@J%I%+82>3<%D%@J895%D%+=2>3%D%@58!!
<;I%2:2>38<%D%<:2>;5%D%<:2>;5%D%<:2>;5
M9I%M8<=599<%D%M8<=59%D%M8<=59%D%M8<=599
;KI%;:8;8<%D%;:5K%D%;:8!%D%;:2C
*7I%:<!2%D%*8>7%D%:<!5%D%:<!2
;4I%<:<%D%;<=4%D%<:%D%;<=4
9GI%9C:3J5!5%D%9C:GC<8!5%D%9C:GC<8!5%D%9C:78!+=2C
!:I%2:;5>9<%D%!8=M5:%D%2:;5>9%D%!8=+5:
;>K5I%;82==<DM5:45%D%K5==<@D;:55>%D%
L2C>5DM5:9%D%;5=+D;:C>
+>%I%E2::<>5%D%+:<@>%D%E2::<>%D%+:2C>
=)
>
)>
7G
)*
7,
7-
),
)-
))
;H
;'
4)
4;
2'
2H
Summary of Contents for RS 310/EV BLU FS1
Page 2: ...Translation of the original instructions...
Page 79: ......