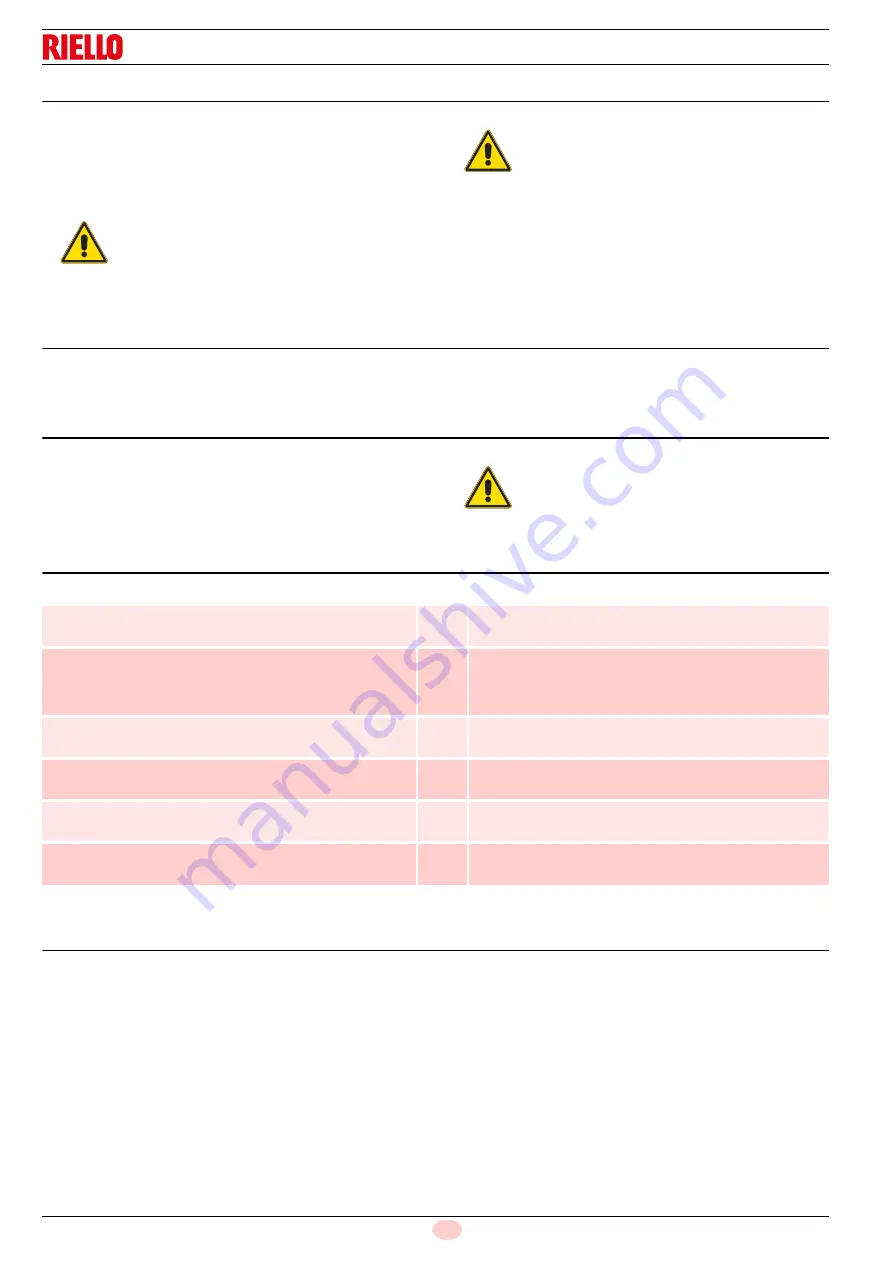
20182250
40
GB
Start-up, calibration and operation of the burner
6.12
Ignition failure
If the burner does not switch on, there is a lockout within 3s of the
electrical supply reaching the fuel valve.
It may be that the fuel does not arrive at the combustion head
within the safety time of 3s.
In this case increase fuel ignition flow rate.
6.13
Burner flame goes out during operation
If the flame accidentally goes out while running, the burner goes
into lockout within 1 second.
6.14
Stopping of the burner
The burner can be stopped by:
intervening on the disconnecting switch of the electrical sup-
ply line, located on the boiler panel;
using the “
0-AUTO
” switch of Fig. 32 on page 34.
6.15
Final checks
With the burner running
Tab. P
6.16
Pump motor lock-out
If the motor does not start, it could be because of a thermal relay
intervention due to its incorrect calibration or problems with the
motor or the main power supply, to release press the button of the
thermal relay, see “Calibration of the thermal relay” on page 20.
WARNING
In the event the burner stops, in order to prevent
any damage to the installation, do not unblock the
burner more than twice in a row.
If the burner locks out for a third time, contact the
customer service.
DANGER
In the event there are further lockouts or faults
with the burner, the maintenance interventions
must only be carried out by qualified, authorised
personnel, in accordance with the contents of this
manual and in compliance with the standards and
regulations of current laws.
WARNING
Make sure that the mechanical locking systems
on the various adjustment devices are fully tight-
ened.
Open the thermostat/pressure switch TL
Open the thermostat/pressure switch TS
the burner must stop
Turn the gas maximum pressure switch knob to the mini-
mum end of scale position
Turn the air pressure switch knob to the maximum end of
scale position
the burner must stop in lockout
Disconnect the minimum gas pressure switch connector
the burner must stop in lockout
Disconnect the maximum oil pressure switch connector
the burner must stop in lockout
Disconnect the minimum oil pressure switch connector
the burner must stop in lockout
Obscure the flame sensor
the burner must stop in lockout due to flame loss
Summary of Contents for RLS 310/EV O2 MX
Page 2: ...Translation of the original instructions ...
Page 52: ...20182250 50 GB Appendix Electrical panel layout 0 0 0 0 0 0 0 0 ...
Page 55: ...53 20182250 GB Appendix Electrical panel layout 0 ...
Page 56: ...20182250 54 GB Appendix Electrical panel layout ...
Page 57: ...55 20182250 GB Appendix Electrical panel layout 0 0 1 2 0 0 0 1 0 ...
Page 58: ...20182250 56 GB Appendix Electrical panel layout 0 0 0 1 0 2 0 0 0 0 0 0 0 30 3 3 0 0 1 0 ...
Page 66: ......
Page 67: ......