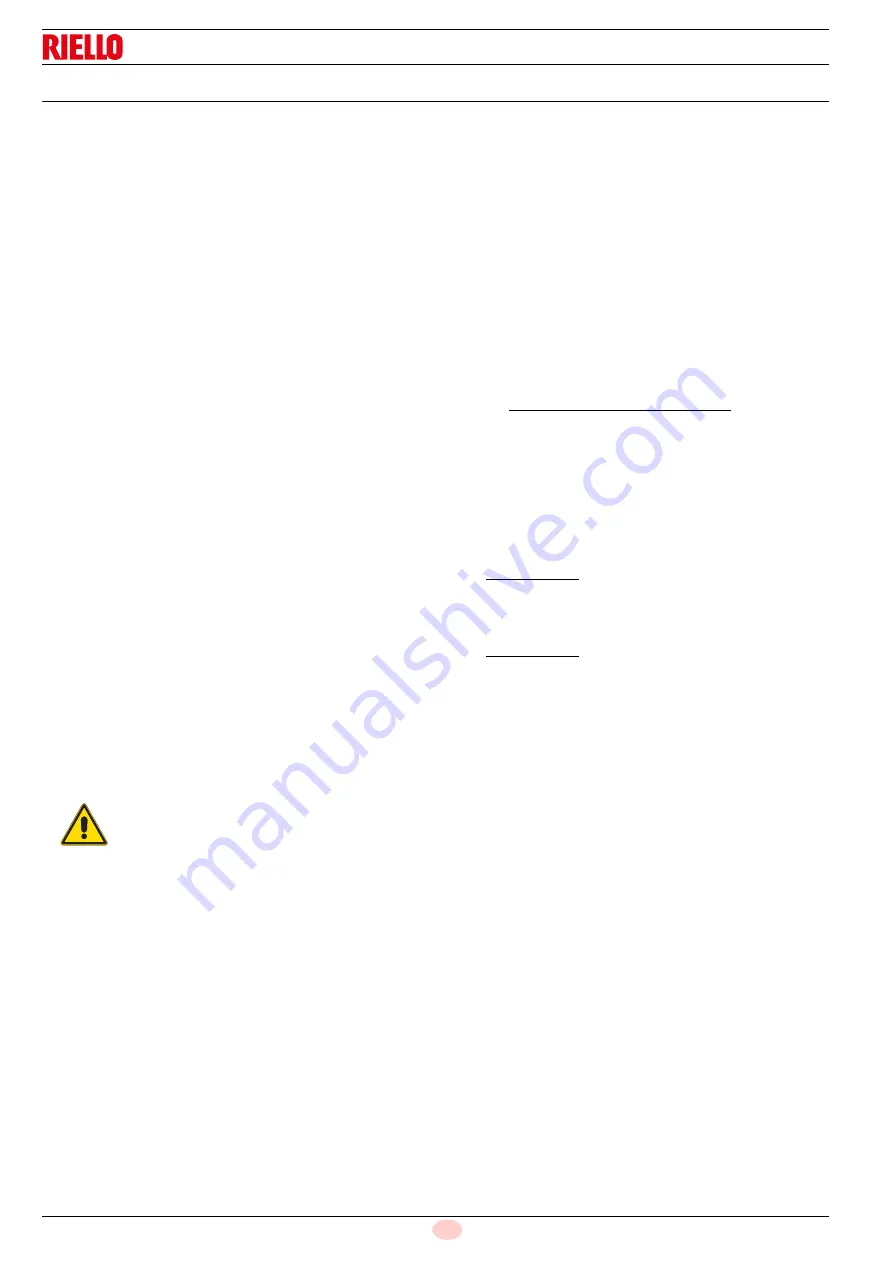
20182250
36
GB
Start-up, calibration and operation of the burner
6.8
Air / fuel adjustment
Air/fuel synchronisation is carried out with the relevant air, gas
and light oil servomotors by logging a calibration curve using the
electronic cam.
It is advisable, to reduce the loss and for a wide calibration field,
to adjust the servomotors to the maximum of the output used, the
nearest possible to the maximum opening (90°).
The choking of the air, taking into account the maximum combus-
tion output, takes place by varying the adjustment of the combus-
tion head (see “Combustion head adjustment” on page 24).
On the gas butterfly valve, the fuel step according to the burner
output required, with servomotor completely open, is carried out
by the pressure stabiliser on the gas train.
6.8.1
Air adjustment for maximum output
Adjust the servomotor to maximum opening (nearly 90°) so
that the air butterfly valves are entirely open.
6.8.2
Air/fuel adjustment and output modulation
system
The air/gas regulator and output modulation system equipping
the
RLS/E MX
range of burners performs a number of integrated
functions for the burner's total energy and operational optimisa-
tion, in both individual installations and in combination with other
units (e.g. double furnace boiler or multiple heat generators in
parallel).
The basic system functions control:
1
the dosage of the air and fuel through positioning using
direct servo commands of the relevant valves eliminating
the possible play in the calibration systems with mechanical
cam lever mechanisms, used on traditional modulating
burners;
2
the modulation of the burner output in accordance with the
load required by the system, with maintenance of the pres-
sure or temperature of the boiler at the operating values set;
3
the sequence (cascade adjustment) of more than one boiler
through the suitable connection of the various units and the
activation of the internal software of the individual systems
(option).
Further interfaces and communication functions with computers,
for remote control or integration in central supervision systems
are available on the basis of the configuration of the system.
6.8.3
Burner adjustment (gas)
The optimum adjustment of the burner requires an analysis of
flue gases at the boiler outlet.
Adjust in sequence:
1 - Output upon ignition
2 - MAX output
3 - MIN output
4 - Intermediate outputs between Min. and Max.
5 - Air pressure switch
6 - Maximum gas pressure switch
7 - Minimum gas pressure switch
6.8.4
Output upon ignition
Ignition must occur at a lower output than the max. operation out-
put. Regulations provide that the ignition output of this burner
must be equal to or less than 1/3 of the MAX operation output.
Example:
MAX operation output of 600 kW.
The ignition output must be equal to or less than 200 kW with ts
= 3s
In order to measure the ignition output:
obscure the flame sensor (the burner starts and goes into
lockout after the safety time);
perform 10 consecutive ignitions with lockouts;
on the meter, read the quantity of gas burned:
This quantity must be equal to, or lower than, the quantity
given by the formula, for ts = 3s:
Vg
volume supplied in ignitions carried out (Sm
3
)
Qa
ignition delivery (Sm
3
/h)
n
number of ignitions (10)
ts
safety time (sec)
Example for gas G20 (9.45 kWh/Sm
3
):
ignition output 200 kW corresponding to
After 10 ignitions with their lockouts, the delivery indicated on the
meter must be equal to or less than:
Air adjustment
The adjustment of the air is carried out by changing the angle of
the air damper 17)(Fig. 5 on page 12) changing the degrees of
the air servomotor inside the electronic cam programme.
6.8.5
Maximum output
The MAX output must be set within the firing rate (Fig. 3 on
page 10).
Adjustment of gas delivery
Measure the gas delivery on the gas meter.
As an indicative guide it can be taken from Tab. O on page 31,
just read the gas pressure on the pressure gauge (shown in
Fig. 24 on page 27) and follow the instructions given on page 27.
–
If it is necessary to reduce it, lower the output gas pressure
via the pressure adjuster located beneath the gas valve.
–
If delivery needs to be increased, increase the adjuster outlet
gas pressure.
Air adjustment
If necessary vary the degrees of the air servomotor.
6.8.6
Minimum output
The MIN output must be set within the firing rate (Fig. 3 on
page 10).
WARNING
The first start up and every further internal setting
operation of the adjustment system or the expan-
sion of the base functions require access by
means of password and are to be carried out by
service personnel who are especially trained for
the internal programming of the instrument and
the specific application created with this burner.
Vg =
3600
Qa
(max. burner delivery)
x n x ts
9.45
200
= 21.16 Sm
3
/h
Vg =
3600
21.16 x 10 x 3
= 0.176 Sm
3
Summary of Contents for RLS 310/EV O2 MX
Page 2: ...Translation of the original instructions ...
Page 52: ...20182250 50 GB Appendix Electrical panel layout 0 0 0 0 0 0 0 0 ...
Page 55: ...53 20182250 GB Appendix Electrical panel layout 0 ...
Page 56: ...20182250 54 GB Appendix Electrical panel layout ...
Page 57: ...55 20182250 GB Appendix Electrical panel layout 0 0 1 2 0 0 0 1 0 ...
Page 58: ...20182250 56 GB Appendix Electrical panel layout 0 0 0 1 0 2 0 0 0 0 0 0 0 30 3 3 0 0 1 0 ...
Page 66: ......
Page 67: ......