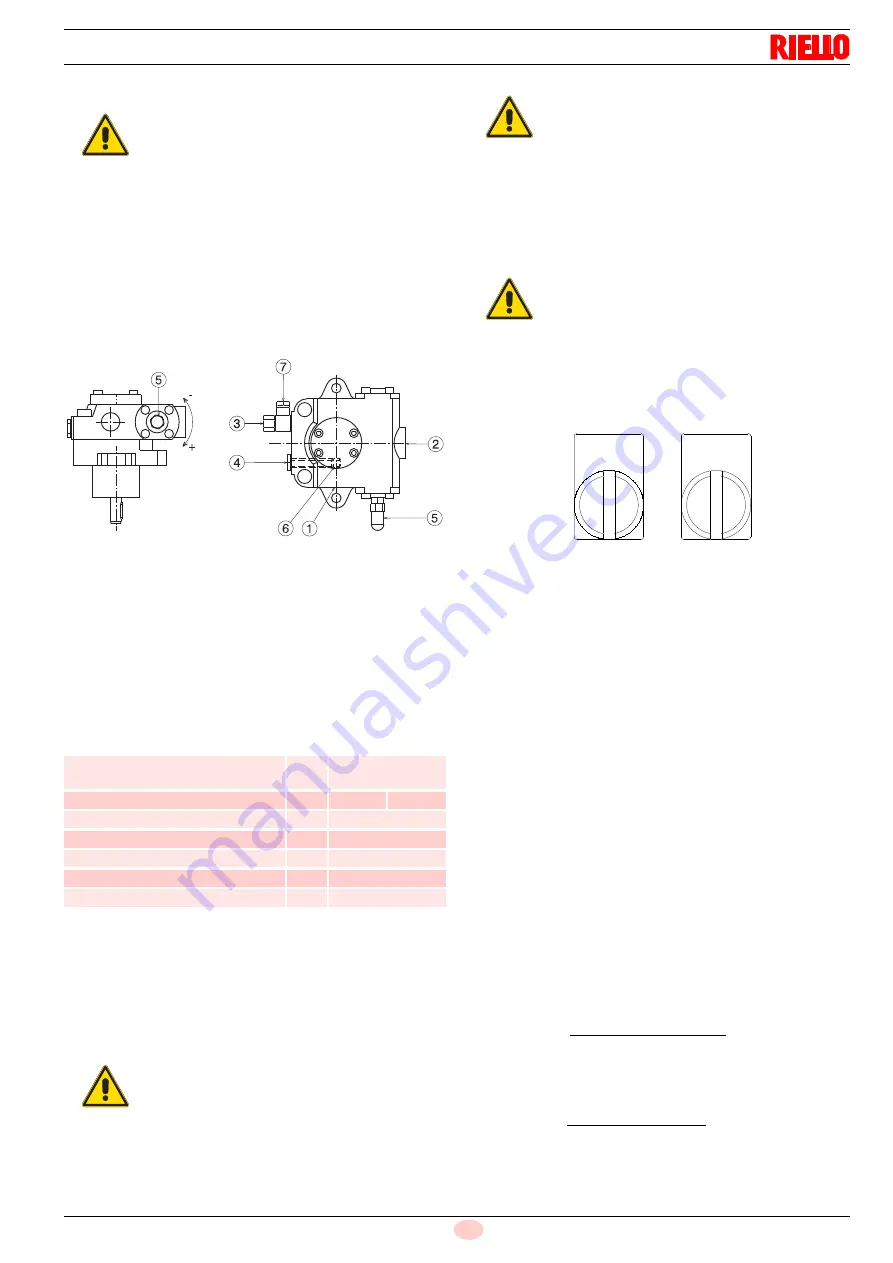
25
20009654
GB
Installation
5.12.6 Pump priming
In order for self-priming to take place, one of the screw 4)
(Fig. 23) of the pump must be loosened in order to bleed off
the air contained in the suction line.
Start the burner by closing the remote controls.
Check the fan wheel rotation direction as soon as the burner
starts.
The pump can be considered primed when the light oil starts
coming out of the screw 4). Stop the burner and screw screw
4) in.
Key to layout
(Fig. 23)
1
Suction
G 1/2"
2
Return
G 1/2"
3
Pressure switch attachmentG 1/4"
4
Vacuum meter connectionG 1/4"
5
Pressure governor
6
Screw for by-pass
7
Pressure gauge c
onnectionG 1/4"
The time required for this operation depends upon the diameter
and length of the suction tubing.
If the pump fails to prime at the first starting of the burner and the
burner locks out, wait approx. 15 seconds, reset the burner,
as often as required. After 5 or 6 starting operations allow 2 or 3
minutes for the transformer to cool.
Do not illuminate the QRI cell or the burner will lock out; the burn-
er should lock out anyway about 10 seconds after it starts.
5.12.7 Burner calibration
Note
It is advisable to first set the burner for operating on oil and then
for gas.
FIRING
Set switch 1) (Fig. 24) to "MAN".
During the first firing, during the passage from the 1st to the 2nd
stage, there is a momentary lowering of the fuel pressure caused
by the filling of the 2nd stage nozzle tubing. This lowering of the
fuel pressure can cause the burner to lock-out and can some-
times give rise to pulsations.
Once the following adjustments have been made, the firing of the
burner must generate a noise similar to the noise generated dur-
ing operation.
OPERATION
The optimum calibration of the burner requires an analysis of the
flue gases at the boiler outlet and interventions on the following
points:
•
Nozzles
See the information listed on pag. 20.
•
Combustion head
The adjustment of the combustion head already carried out
(pag. 21) need not be altered unless the 2nd stage delivery
of the burner is changed.
•
Pump pressure
It is calibrated in factory and generally it goes well:
RLS 300/E MX = 22 bar
RLS 400/E MX = 20 bar
RLS 500/E MX = 25 bar
–
In order to adjust pump pressure, use the relevant screw 5) (
Fig. 23)
–
It is possible to reduce the fuel delivery only if the tempera-
ture is higher than 0 °C:
RLS 300/E MX = 20 bar
RLS 400/E MX = 18 bar
RLS 500/E MX = 25 bar
–
It is possible to increase fuel delivery or to ensure firings even
at temperatures less than 0 °C.
RLS 300/E MX = 24 bar
RLS 400/E MX = 22 bar
RLS 500/E MX = 26 bar
WARNING
Before starting the burner, make sure that the tank
return line is not clogged.
Obstructions in the line could cause the sealing
organ located on the pump shaft to break.
PUMP SUNTEC
TA4
TA5
Min. delivery rate at 16,5 bar pres-
sure
kg/h
560
- Delivery pressure range
bar
7-40
6-30
- Max. suction depression
bar
0.45
- Viscosity range
cSt
4 - 800
- Light oil max. temperature
°C
140
Max. suction and return pressure
bar
5
- Pressure calibration in the factory
bar
22-20
WARNING
The a.m. operation is possible because the pump
is already full of fuel when it leaves the factory. If
the pump has been drained, fill it with fuel through
the opening on the vacuum meter 4) (Fig. 23) prior
to starting; otherwise, the pump will seize.
Fig. 23
D9249
WARNING
Whenever the length of the suction piping ex-
ceeds 20-30 meters, the supply line must be filled
using a separate pump.
WARNING
Execute the fuel exchange when the burner is
off.
Fig. 24
D3108
1
2
0 AUTO MAN
- +
Summary of Contents for RLS 300/E MX
Page 2: ......
Page 47: ...45 20009654 GB Appendix Electrical panel layout ...
Page 48: ...20009654 46 GB Appendix Electrical panel layout ...
Page 50: ...20009654 48 GB Appendix Electrical panel layout ...
Page 51: ...49 20009654 GB Appendix Electrical panel layout 0 1 1 1 ...
Page 52: ...20009654 50 GB Appendix Electrical panel layout 0 1 0 ...
Page 53: ...51 20009654 GB Appendix Electrical panel layout 0 0 0 1 0 2 0 0 0 0 0 0 0 30 3 3 0 0 1 0 ...