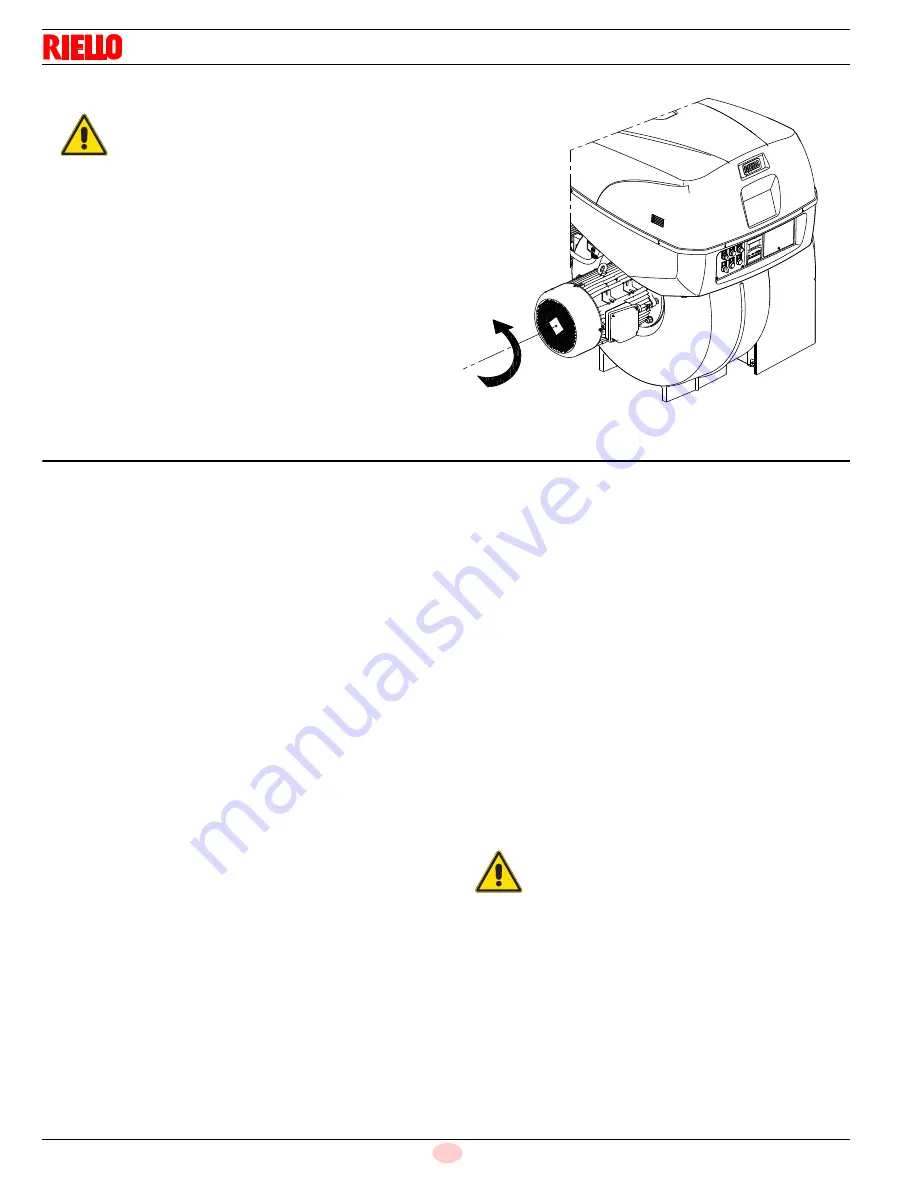
20146383
40
GB
Start-up, calibration and operation of the burner
5.6.1
Direction of motor rotation
5.7
Burner ignition
Once the above steps are complete, the burner should light.
If the motor starts up, but the flame does not appear and the control
box goes into lockout, reset it and wait for a new ignition attempt.
If ignition is still not achieved, it may be that gas is not reaching the
combustion head within the safety time period of 3 seconds. In this
case increase gas ignition delivery.
The arrival of gas at the pipe coupling is indicated by the U-type
pressure gauge (Fig. 47).
If further burner lockouts occur, refer to the “Release procedure”
given in the equipment manual supplied.
Once the burner has ignited, proceed with the global adjustment of
the burner.
5.7.1
Air / gas adjustment and output modulation
The air/gas regulator and output modulation system equipping
RS
series burners performs a number of integrated functions to opti-
mise burner function, in both individual installations and in combi-
nation with other units (e.g. double furnace boiler or multiple heat
generators in parallel).
The basic system functions control:
1
The dosage of the air and fuel through positioning using direct
servocommands of the relevant valves eliminating the possi-
ble play in the calibration systems with mechanical cam lever
mechanisms, used on traditional modulating burners.
2
The modulation of the burner output in accordance with the
load required by the system, with maintenance of the pres-
sure or temperature of the boiler at the operating values set.
3
The sequence (cascade adjustment) of more than one boiler
through the suitable connection of the various units and the
activation of the internal software of the individual systems
(option).
Further interfaces and communication functions with computers,
for remote control or integration in central supervision systems are
available on the basis of the configuration of the system.
The first start-up and curve synchronisation manual is supplied with
the burner.
At request, the complete manual for the control and setting of all
parameters is available.
WARNING
When the burner starts, check the direction of the
motor rotation, as indicated in Fig. 47.
If the burner is not equipped with a device to check
the phases sequence, the motor could rotate incor-
rectly. As soon as the burner starts up, look at the
cooling fan of the fan motor and check it is rotating
anticlockwise.
If this is not the case:
place the switch of Fig. 47 in position
“OFF”
and wait for the control box to carry out the
switch-off phase;
disconnect the electrical supply from the
burner;
invert the phases on the inverter output.
Fig. 47
20151052
WARNING
The first start up and every further internal setting
operation of the adjustment system or the expan-
sion of the base functions require access by means
of password and are to be carried out by service
personnel who are especially trained for the internal
programming of the instrument and the specific ap-
plication created with this burner.
Summary of Contents for RLAS 1000 EV
Page 2: ...Original instructions ...
Page 50: ...20146383 48 GB Appendix Spare parts A Appendix Spare parts ...
Page 54: ......
Page 55: ......