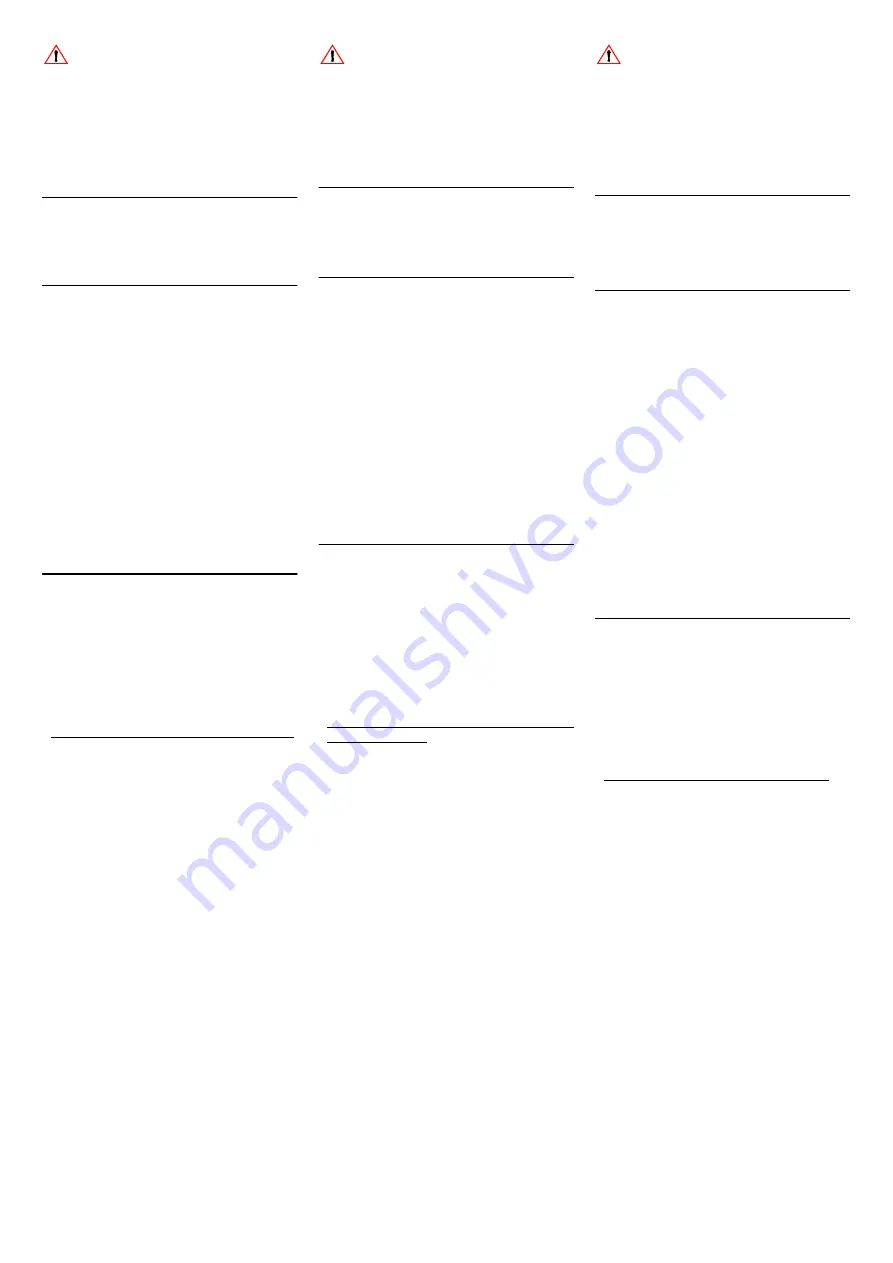
19
VOR MONTAGE DER HAUBE IST ES
NOTWENDIG, DEN BEILIEGENDEN
MOTORSCHUTZ (1)(A), AN DER HAL-
TERUNG
(2)(A)
ZU
MONTIEREN,
WOZU DIE ZUGEHÖRIGEN SCHRAU-
BEN (3)(A) MIT MUTTER UND UNTER-
LEGSCHEIBE VERWENDET WERDEN.
DIE
HALTERUNG
MIT
DER
SCHRAUBE (4)(A) AM VORDEREN
BRENNERSCHILD BEFESTIGEN.
KESSELPLATTE (B)
Die Abdeckplatte der Brennkammer wie in (B)
gezeigt vorbohren. Die Position der Gewinde-
bohrungen kann mit dem zur Grundausstattung
gehörenden Wärmeschild ermittelt werden.
FLAMMROHRLÄNGE (C)
Die Länge des Flammrohrs muß größer als die
Stärke der Kesseltür einschließlich feuerfestes
Material sein. Die Längen, (mm), sind:
Flammrohr 10):
• kurz
250
• lang
385
Für Heizkessel mit vorderem Abgasumlauf 15)
oder
Flammenumkehrkammer
muß
eine
Schutzschicht aus feuerfestem Material 11),
zwischen feuerfestem Material 12) und Flamm-
rohr 10) ausgefüht werden.
Diese Schutzschicht muß so angelegt sein, daß
das Flammrohr ausbaubar ist.
Für die Kessel mit wassergekühlter Frontseite
ist die Verkleidung mit feuerfestem Material 11)-
12) nicht notwendig, sofern nicht ausdrücklich
vom Kesselhersteller erfordert.
BEFESTIGUNG DES BRENNERS AM
HEIZKESSEL (D)
Vor der Befestigung des Brenners am Heizkes-
sel ist von der Öffnung des Flammrohrs aus zu
überprüfen, ob der Fühler und die Elektrode
gemäß (D) in der richtigen Stellung sind.
Dann den Flammkopf vom übrigen Brenner
abtrennen, Abb (C):
- Schraube 13) abnehmen und die Verkleidung
14) herausziehen.
- Das Gelenk 4) vom Skalensegmen 5) ausrasten.
- Die Schrauben 2) von den zwei Gleitschienen
3) abnehmen.
- Die Schraube 1) abnehmen und den Brenner
auf den Gleitschienen 3) ca. 100 mm. nach
hinten schieben.
- Die Fühler- und Elektrodenkabel abtrennen
und dann den Brenner komplett aus den Gleit-
schienen ziehen, nach Entnahme des Splints
aus der Führung 3).
Den Flansch 9)(C) an der Kesselplatte befesti-
gen und den beigestellten Wärmeschild 6)(C)
dazwischenlegen. Die 4 ebenfalls beigepackten
Schrauben nach Auftragung von Freßschutzmit-
teln verwenden.
Es muß die Dichtheit von Brenner-Kessel
gewährleistet sein.
Falls bei der vorhergehenden Prüfung die Posi-
tionierung des Fühlers oder der Elektrode sich
als nicht richtig erweist, die Schraube 1)(E)
abnehmen, das Innenteil 2)(E) des Kopfs heraus-
ziehen und eine neue Einstellung vornehmen.
Den Fühler nicht drehen, sondern wie in (D) las-
sen; seine Positionierung in der Nähe der Zün-
delektrode
könnte
den
Geräteverstärker
beschädigen.
BEFORE ASSEMBLING THE CASING,
IT IS NECESSARY TO FIX THE ENGINE
PROTECTION SUPPLIED (1)(A), ONTO
THE BRACKET (2)(A), USING THE AP-
PROPRIATE SCREWS (3)(A) WITH A
NUT AND A WASHER.
FIX THE BRACKET TO THE FRONT
SHIELD OF THE BURNER, USING THE
SCREWS (4)(A).
BOILER PLATE (B)
Drill the combustion chamber locking plate as
shown in (B). The position of the threaded holes
can be marked using the thermal screen sup-
plied with the burner.
BLAST TUBE LENGTH (C)
The length of the blast tube must be greater
than the thickness of the boiler door complete
with its fettling. The lengths, L (mm), are:
Blast tube 10):
• short
250
• long
385
For boilers with front flue passes 15) or flame
inversion chambers, protective fettling in refrac-
tory material 11), must be inserted between the
boiler fettling 12) and the blast tube 10).
This protective fettling must not compromise the
extraction of the blast tube.
For boilers having a water-cooled front the refrac-
tory fettling 11)-12) is not required unless it is
expressly requested by the boiler manufacturer.
SECURING THE BURNER TO THE
BOILER (D)
Before securing the burner to the boiler, check
through the blast tube opening to make sure
that the flame sensor probe and the ignition
electrode are correctly set in position, as shown
in (D).
Now detach the combustion head from the
burner, fig. (C):
- Remove screw 13) and withdraw the cover
14).
- Disengage the articulated coupling 4) from the
graduated sector 5).
- Remove the screws 2) from the slide bars 3).
- Remove screw 1) and pull the burner back on
slide bars 3) by about 100 mm.
- Disconnect the wires from the probe and the
electrode and then pull the burner completely
off the slide bars, after removing the split pin
from the slide bar 3).
Secure the flange 9)(C) to the boiler plate, inter-
posing the thermal insulating screen 6)(C) sup-
plied with the burner. Use the 4 screws, also
supplied with the unit, after first protecting the
thread with an anti-locking product.
The seal between burner and boiler must be air-
tight.
If you noticed any irregularities in the positions
of the probe or ignition electrode during the
check mentioned above, remove screw 1)(E),
extract the internal part 2)(E) of the head and
proceed to set up the two components correctly.
Do not attempt to turn the probe. Leave it in the
position shown in (D) since if it is located too
close to the ignition electrode the control box
amplifier may be damaged.
PAVANT DE MONTER LE COFFRE IL
EST NECESSAIRE DE FIXER LA PRO-
TECTION DU MOTEUR, FOURNIE
AVEC L'EQUIPEMENT (1)(A), SUR LA
BRIDE (2)(A), EN UTILISANT LES VIS
APPROPRIEES (3)(A) AVEC ECROU
ET RONDELLE. IXER LA BRIDE A
L'ENVELOPPE SUR LE DEVANT DU
BRULEUR AVEC LA VIS (4)(A).
PLAQUE CHAUDIERE (B)
Percer la plaque de fermeture de la chambre de
combustion comme sur la fig. (B). La position
des trous filetés peut être tracée en utilisant
l'écran thermique fourni avec le brûleur.
LONGUEUR BUSE (C)
La longueur de la buse doit être supérieure à
l'épaisseur de la porte de la chaudière, matériau
réfractaire compris. Les longueurs, L (mm),
sont:
Buse 10):
• courte
250
• longue
385
Pour les chaudières avec circulation des
fumées sur l'avant 15), ou avec chambre à
inversion de flamme, réaliser une protection en
matériau réfractaire 11), entre réfractaire chau-
dière 12) et buse 10).
La protection doit permettre l'extraction de la
buse.
Pour les chaudières dont la partie frontale est
refroidie par eau, le revêtement réfractaire 11)-
12) n'est pas nécessaire, sauf indication precise
du constructeur de la chaudière.
FIXATION DU BRULEUR A LA CHAU-
DIERE (D)
Avant de fixer le brûleur à la chaudière, vérifier
par l'ouverture de la buse si la sonde et l'élec-
trode sont positionnées correctement comme
indiqué en (D).
Séparer ensuite la tête de combustion du reste
du brûleur, fig. (C):
- Retirer la vis 13) et extraire le coffret 14).
- Décrocher la rotule 4) du secteur gradué 5).
- Retirer les vis 2) des deux guides 3).
- Retirer la vis 1) et faire reculer le brûleur sur
les guides 3) d'environ 100 mm.
- Détacher les câbles de la sonde et de l'élec-
trode, enlever ensuite complètement le brûleur
des guides, après avoir ôté la goupille du
guide 3).
Fixer la bride 9)(C) à la plaque de la chaudière
en interposant l'écran isolant 6)(C) fourni de
série. Utiliser les 4 vis également de série après
en avoir protégé le filetage par du produit anti-
grippant.
L'étanchéité brûleur-chaudière doit être parfaite.
Si, lors du contrôle précédent, si le positionne-
ment de la sonde ou de l'électrode n'était pas
correct, retirer la vis 1)(E), extraire la partie
interne 2)(E) de la tête et tarer celles-ci. Ne pas
faire pivoter la sonde mais la laisser en place
comme indiqué en (D); son positionnement dans
le voisinage de l'électrode d'allumage pourrait
endommager l'amplificateur de l'appareil.