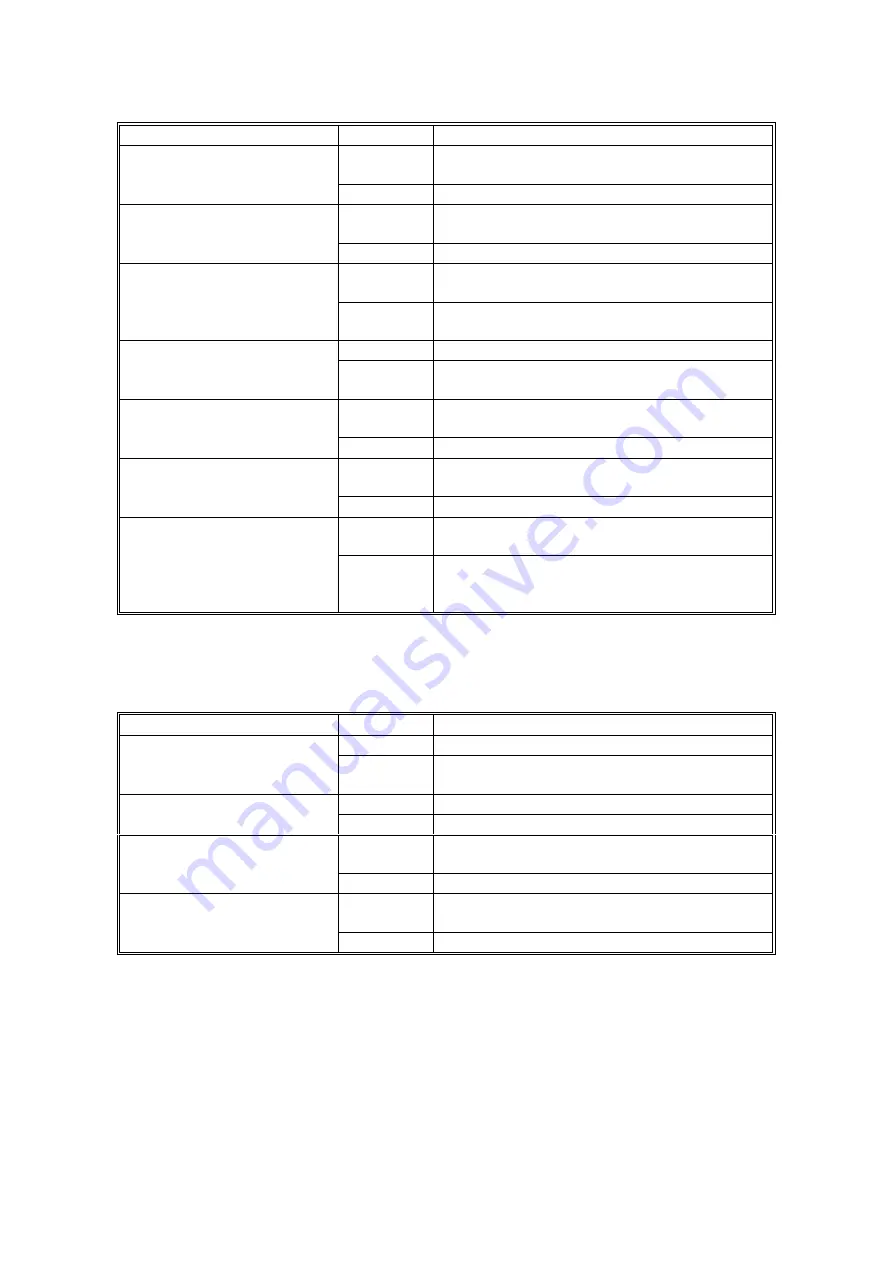
ELECTRICAL COMPONENT DEFECTS
31 October 2001
4-4
Component
Condition
Symptom
Master Set Cover Sensor
Open
The “D” jam indicator is lit or E-01 is displayed
whenever the cover isn’t placed correctly.
Shorted
The “the open cover” and “D” indicators are lit.
Master End Sensor
White
Master making can start even if there is no
master roll, but the “D” jam indicator will be lit.
Black
The “load new master roll” indicator is lit.
Paper Height Sensor
Open
The “A” jam indicator is lit whenever a copy is
made.
Shorted
The paper table goes up over the sensor, and
E-02 is displayed
Registration Sensor
Open
The “A” jam indicator is lit.
Shorted
The “A” jam indicator is lit whenever a copy is
made.
Paper End Sensor
Open
Printing can begin even if there is no paper,
but the “A” jam indicator will be lit.
Shorted
The “load more paper” indicator is lit.
Cutter HP Sensor
Open
The cutter cuts the master only half way, and
the “D” jam indicator is lit.
Shorted
E-01 is displayed.
Paper Length Sensor
Open
The press roller becomes dirty whenever the
paper is shorter than the image.
Shorted
Long images will be cut because the machine
does not detect the presence of long paper
sizes on the table.
4.2.2 SWITCHES
Component
Condition
Symptom
Door Safety Switch
Open
The “the open cover” indicator is lit.
Shorted
The “the open cover” indicator is not lit even if
the door is opened.
Main Switch
Open
The machine does not turn on.
Shorted
The machine does not turn off.
Master Making Unit Set
Switch
Open
E-09 is displayed whenever the master
making unit is not installed.
Shorted
The “the open cover” and “E” indicators are lit.
Eject Box Set Switch
Open
The master is fed to the eject box, even if
there is no eject box.
Shorted
The “the open cover” and “E” indicators are lit.
Summary of Contents for Gestetner 5428C
Page 1: ...SERVICE MANUAL Machine code C238...
Page 140: ...POINT TO POINT DIAGRAM 31 October 2001 7 2 Location Map C238S500 WMF...
Page 141: ...31 October 2001 POINT TO POINT DIAGRAM 7 3 P to P Section A C238S501 WMF...
Page 142: ...POINT TO POINT DIAGRAM 31 October 2001 7 4 Section B C238S502 WMF...
Page 143: ...31 October 2001 POINT TO POINT DIAGRAM 7 5 P to P Section C C238S503 WMF...
Page 144: ...POINT TO POINT DIAGRAM 31 October 2001 7 6 Section D C238S504 WMF...
Page 145: ...31 October 2001 POINT TO POINT DIAGRAM 7 7 P to P Section E C238S505 WMF...
Page 146: ...POINT TO POINT DIAGRAM 31 October 2001 7 8 Section F C238S506 WMF...
Page 147: ...31 October 2001 POINT TO POINT DIAGRAM 7 9 P to P Section G C238S507 WMF...
Page 148: ...POINT TO POINT DIAGRAM 31 October 2001 7 10 Section H C238S508 WMF...