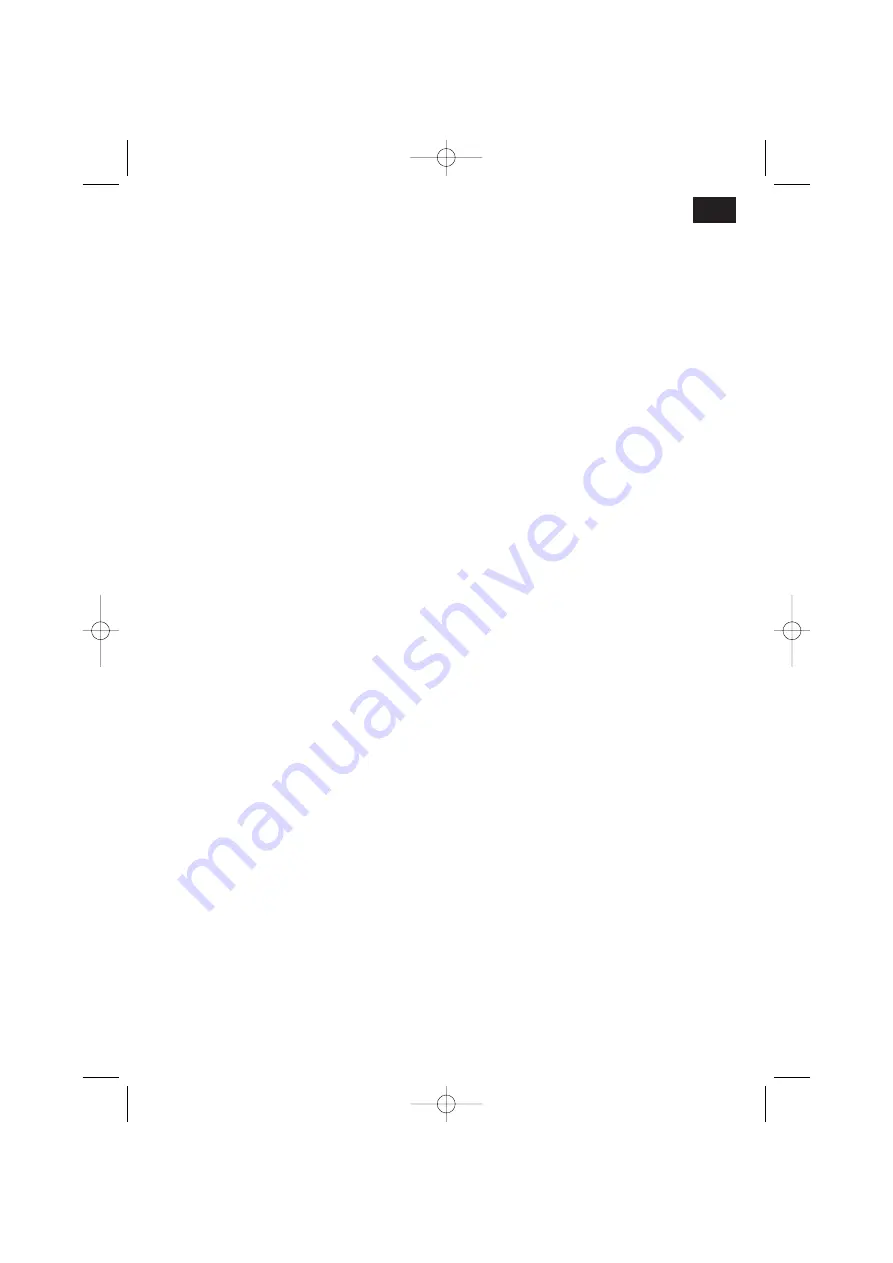
If the cable is damaged, it has to be replaced by the
manufacturer or by its Service Center or in any case by
a qualified person , in order to avoid any risk.
6.1 A The tool has to be placed in a suitable way to
allow an easily reaching of the plug.
6.3 Functioning check
Before installing the motor pump make an idling check
of the motor. Make sure that all the electrical contacts
are well sealed, start the motor pump observing the
cooling vane on the back of the motor (Fig. 2). Control
that the sense of rotation is the one indicated by the
arrow on the body of the pump.
CHAP. 7 INSTALLATION
The motor pump is an electrical device and should
therefore not be exposed to the inclemency of the
weather (sun, rain, snow, etc). It should also not be
exposed to water jets and be placed in a correctly
ventilated place.
7.1 Fixed positioning
The pump should be placed on a perfectly flat and
solid surface. Carefully respect the minimum distances
foreseen for the walls (Fig. 3) to make possible
maintainance operations easier. The motor pump
should be placed as near as possible to the diesel oil
source (max. 6 m distance).
7.2 Installation
A) Use metallic tubes or plastic tubes with a high
degree of resistance.
B) If you use flexible delivery and intake tubes avoid
folding them in order not to cause throttlings.
C) The tubes should have a diameter suitable to the
openings of the motor pump, equipped with thread
muffs sealed with proper sealants.
D) If the intake tube is longer than 4 m., it should have
a diameter wider than that of the intake opening. It
is also advised to mount a suction valve with filter.
E) It is advised to mount a ball valve on the outlet of the
delivery tube.
F) Fix the inlet tubes so that weight and vibrations are
not loaded on the motor pump.
CHAP. 8 USE AND START
8.1 Start
A) Control once more that the electrical contacts are
well closed and sealed and that the feeding cable
has not been damaged during the installation and
then close the delivery gate.
B) Fill in the motor pump through the suitable filling
hole and remove the plug (Fig. 4). Once the body of
the pump and the inlet tube have been completely
filled in, close the filling hole (Fig. 4).
C) Insert the plug into the socket or operate the start
switch. Before carrying out this operation carefully
read Chap. 3 par. 3.1.
D) The motor pump will now start its work.
8.2 Important cautions
A) Avoid letting the motor pump work dry (without
water inside the body of the pump).
B) The prolonged working with the delivery gate closed
could provoke serious damages.
C) In case of lack of electric power supply, disconnect
the plug from the socket or disconncet the switch.
8.3 Stop
A) Close the delivery gate before putting off the motor
pump. This will avoid possible noisy ram blows.
Then put off the switch.
B) If the motor pump is not used for a more or less long
period, it is better to empty the body of the pump.
CHAP. 9 MOUNTING AND DISMOUNTING
The motor pump does not have separated accessory
parts and is therefore not to be mounted. The possible
dismounting of the motor pump should be carried out
only in Service Centers and by qualified technicians.
CHAP. 10 MAINTAINANCE AND REPAIR
10.1 Maintainance
Unplug the mains before carrying out any
maintainance. The motor pump doesn’t need particular
maintainance in the inside. Therefore avoid
dismounting it. It is all the same very important that the
inlet and the delivery part is kept perfectly clean and
free from possible obstructive bodies.
CHAP. 11 MECHANICAL RISKS
11.1 Mechanical parts which can wear out
A)The mechanical seal (Pict. 5 pos. 17) can wear out
even after a relatively short time mostly if slightly
abrasive liquids have been pumped. This part has to be
replaced even if it has been simply dismounted for
whichever inspection.
B) Bearings (Pict. 5 pos.8)
C) Impeller (Pict. 5 pos.16)
Attention : Above mentioned parts have to be replaced
only by qualified technicians or in Service
Centers. Only use original spare parts.
CHAP. 12 DIAGRAM OF TECHNICAL DATA OF THE
MACHINE
Manufacturing features of the motor
Closed electrical motor selfventilated with two poles,
with protection IP55, insulation class F. Monophase
version with incorporated thermal motoprotector and
constantly inserted condensator.
Manufacturing features of the pump
Body: CAST IRON G 25
Motor support: CAST IRON G 25
Impeller: PRESSED BRASS
Motor shaft: INOX STEAL
Mechanical seal: CERAMIC COAL
GB
8
WEC KG130 4-02-2008 11:09 Pagina 8
Summary of Contents for KG130
Page 10: ......