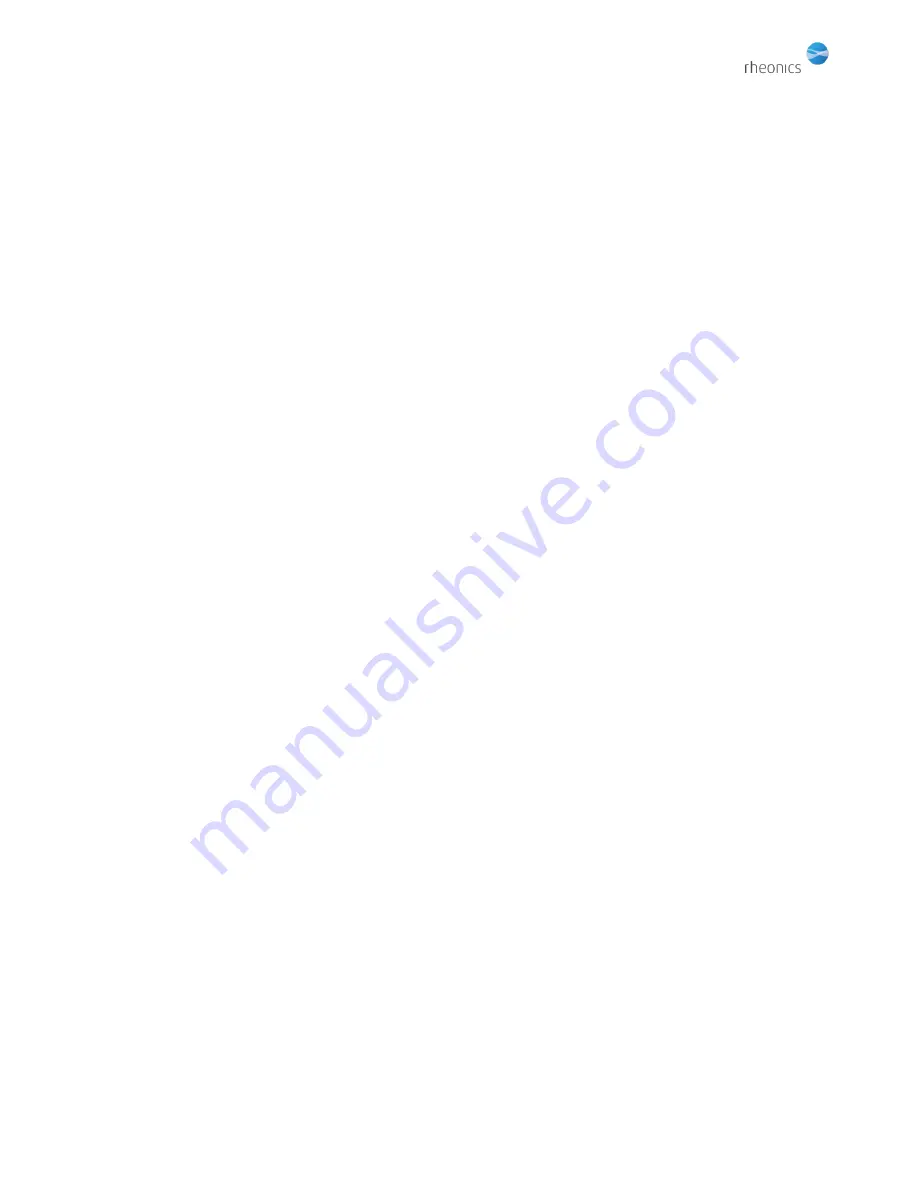
Rheonics | Switzerland | U.S.A.
SRV, SRD, SRV-FPC, SRD-FPC Installation and Intrinsic Safety Manual
P. 25
Version 2.0, Updated: October 29, 2020
Rheonics GmbH, Klosterstrasse 19, 8406 Winterthur, Switzerland
©Rheonics. Rheonics confidential and proprietary information.
5.4.
Equipotential bonding
5.4.1.
Bonding/grounding conductor
In order to eliminate the risk of gas ignition by sparks and/or local heating caused by ground
loops, the sensors and their associated Zener barriers must be connected by suitable
conductors, as specified in the following sections.
There are four different options for equipotential bonding. Three depend on independent
bonding conductors that connect each sensor to the common ground potential. The fourth
makes use of the cable shield braid to perform the potential equalization function, providing the
shield meets certain basic requirements.
There are several options available for the equipotential bonding wiring:
1.
Sensor cable shields for equipotential bonding
1.1.
The cable must have a braided shield with a total cross-sectional copper area of at least
2.5mm
2
.
1.2.
If it is desired to use the cable shield for equipotential bonding, it is recommended to use
Helu Kabel type OB-BL-PAAR-CY 4x2x0.5mm
2
for the sensor connection
1.3.
The cable shield must be firmly bonded to the shell of the M12 connector used for the
sensor connection.
Follow connector manufacturer’s installation instructions.
1.4.
The cable shield must be securely connected to the grounding terminal of its associated
Zener diode barrier.
2.
If a cable other than the recommended type is used, the installer must ensure that its shield
cross sectional area is at least 2.5mm
2
. If this cannot be verified, then one of the following
equipotential bonding methods must be used.
Each of the following methods requires using a
sensor with an installed bonding tab. The optional bonding tab is included with each sensor
delivered.
Proper installation of the bonding tab is shown in Fig. 12 below.
2.1.
In the case of multiple sensors installed in a specific location that are then connected to
Zener barriers in a
remote electrical system, a “star” topology can be used
(Fig. 13 below)
2.2.
If it is more convenient because of the layout of an array of sensors in the system, a
hybrid or “multi
-
drop” configuration can be used (Fig.1
4 below).
2.3.
Individual bonding wires between sensors and Zener diode barriers. This requires
installing the bonding tab delivered with the sensor. Each sensor is connected to its
respective barrier by means of a wire of at least 4mm
2
cross section. On the sensor side,
the wire is connected to the bonding tab on the back of the sensor; on the Zener diode
barrier side it is connected to the grounding terminal of the barrier (Fig. 15 below)