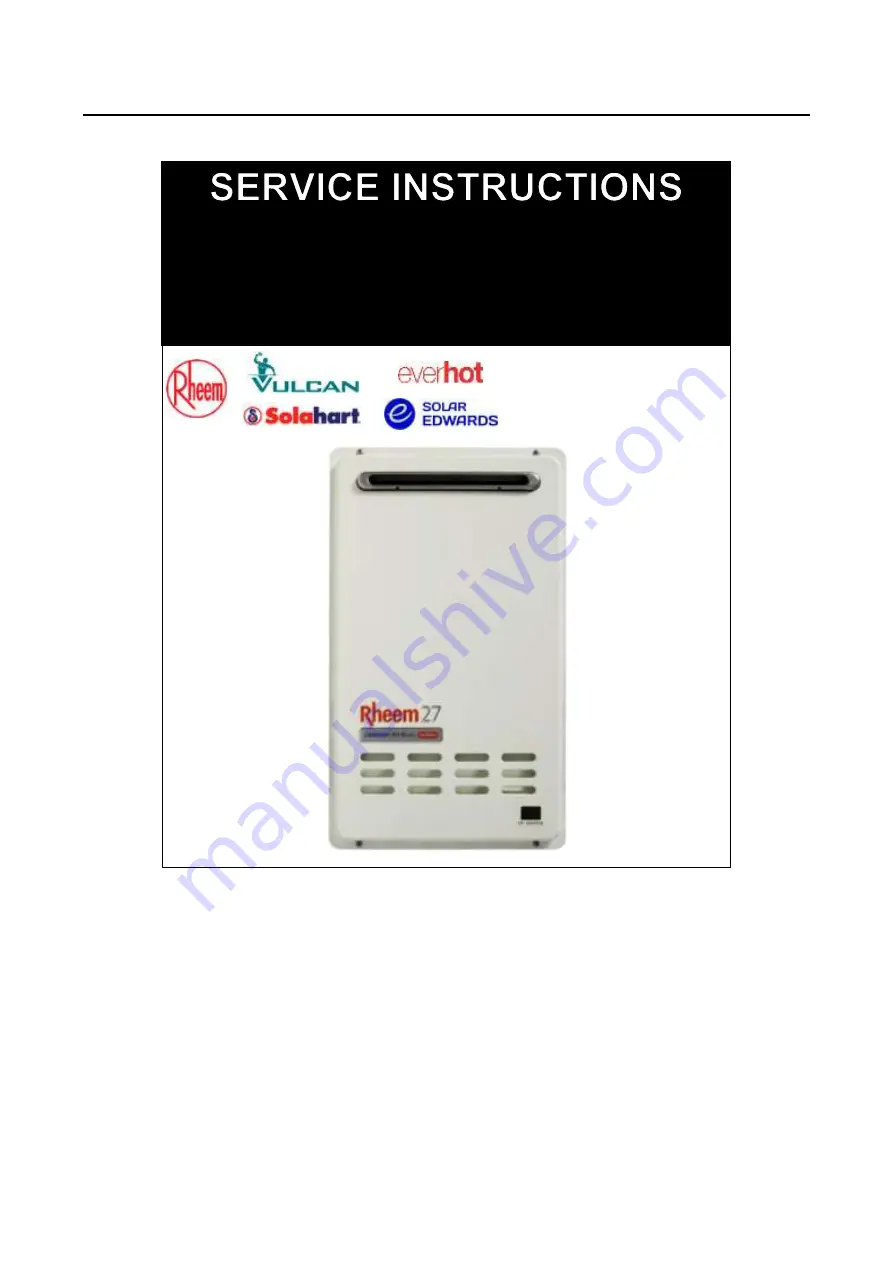
This document is stored and maintained electronically by Rheem Technical Support.
All printed copies are deemed “uncontrolled”.
Rheem Australia Pty Ltd
ABN 21 098 823 511
27 Litre External/Internal
Electronic Gas Continuous Flow Water Heater
TM049
First Issued: Dec 09
Revision: AL
Issued: April 2019
Solahart
Edwards Everhot
Vulcan
Rheem
10143272
362027
274X27 244X27
862X27
10143273
372027
276X27
864X27
10143274
374X27
866X27
10143275
872X27
874X27
876X27