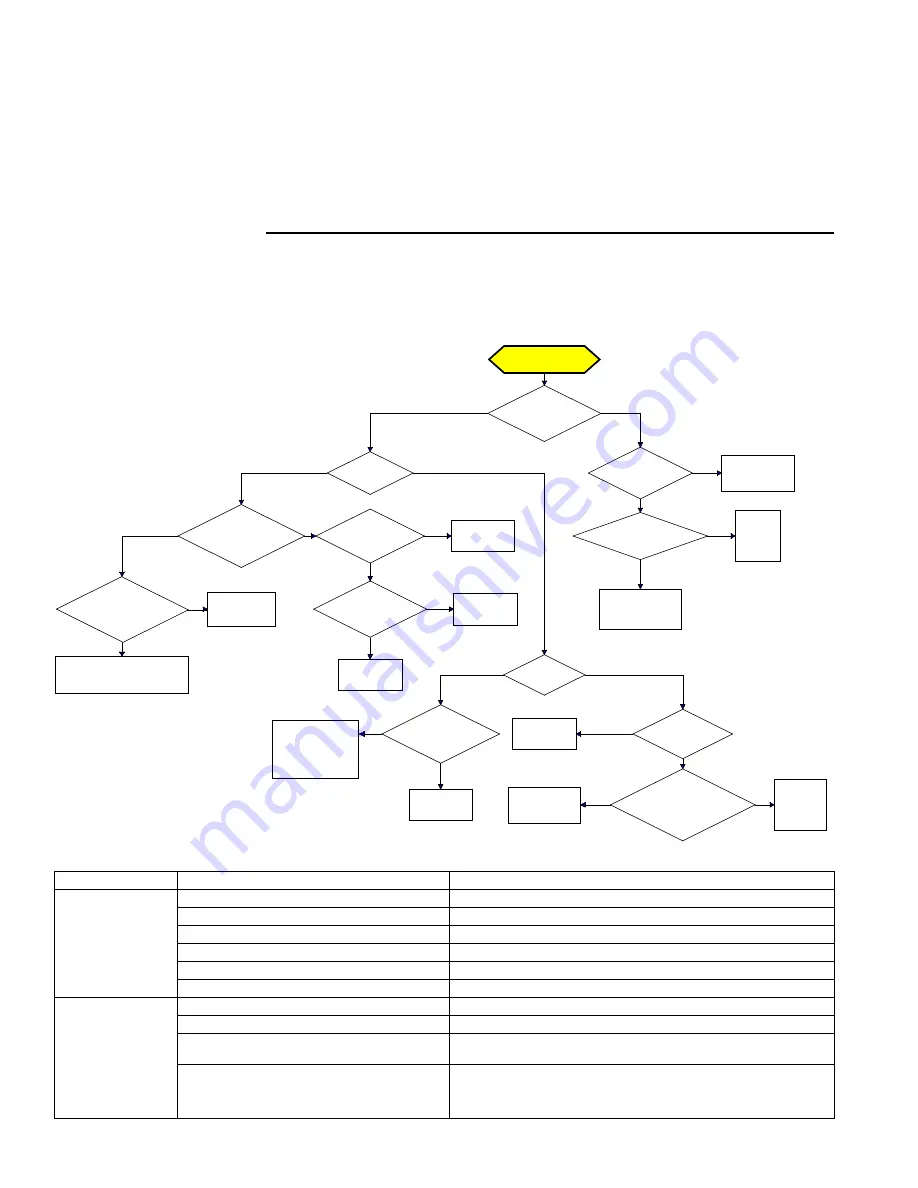
Form I-UDA, P/N 195673 Rev 13, Page 36
General Troubleshooting
Control Status - Green LED Codes
Steady ON
Normal Operation, No call for heat
Fast Flash .
Normal Operation, Call for heat
1 Flash ......
System Lockout, Failed to detect or sustain flame
2 Flashes ..
Pressure Switch Did Not Close within 30 Seconds of Venter Motor
3 Flashes ..
High Limit or Flame Rollout Switch Open
4 Flashes ....
Pressure Switch is Closed Before Venter Motor is Energized
Steady OFF
Blown fuse, No Power, or Defective Board
Flame Status - Yellow LED Codes
Steady ON
..Flame is sensed
Slow Flash ..
Weak flame (current below 1.0 microamps ± 50%)
Fast Flash ...
Undesired Flame (valve open and no call for heat)
IMPORTANT:
When using
a multimeter to troubleshoot
the 24 volt circuit, place the
meter’s test leads into the 5
or 9 pin connectors located
on the ignition control. Do
not remove connectors or
terminals from the electri
-
cal components. Doing so
can result in misinterpreted
readings due to the ignition
control board’s fault mode
monitoring circuits.
10.3 Troubleshooting (cont’d)
DSI Integrated Control Module (Circuit
Board) Trial Troubleshooting Flowchart
Trial for Ignition
Call for Heat
Is there a
spark across gap at
ignitor?
Does gas
ignite?
Is there minimum
flame current at the
flame sensor?
Is there
minimum flame current
at the control
module?
Replace control
module.
Check connections to flame
sensor and/or moisture in the
burner assembly.
Is the flame
sensor corroded?
Clean flame
sensor.
Is the sensor
located in flame
correctly?
Replace flame
sesnsor.
Reposition
flame sensor.
Is gas
flowing?
Is the ignitor
position correct in the
gas flow?
Check gas pressure
and supply voltage.
If either are low,
correct and repeat
startup.
Reposition
spark ignitor.
Is there
24VAC at the gas
valve?
Is there 24VAC
from gas valve output on
control module to
chassis?
Check wiring and
connections to
gas valve.
Replace
ignition
control
module.
Replace gas
valve.
Is there
spark voltage at
control?
Check high
voltage wire
continuity.
Is there 24V P1-2
to power control?
Replace
control
module.
Check wiring
and/or 24VAC
transformer output.
YES
NO
YES
NO
YES
NO
YES
NO
YES
NO
YES
NO
YES
NO
YES
NO
NO
YES
YES
NO
YES
NO
YES
NO
PROBLEM
PROBABLE CAUSE
REMEDY
Venter motor will not
start
1.
No power to unit.
1.
Turn on power, check supply fuses or circuit breaker.
.
No 24 volt power to integrated circuit board.
.
Turn up thermostat; check control transformer output.
3.
Integrated circuit board fuse blown.
3.
Correct cause. Replace fuse (type ATC or ATO, 32VDC, 3A).
4
. No power to venter motor.
4.
Tighten connections at circuit board and/or motor terminals.
5
. Integrated circuit board defective.
5.
Replace integrated circuit board.
6.
Defective venter motor.
6.
Replace venter motor. See Paragraph 29.
Burner will not light
1.
Manual valve not open.
1.
Open manual valve.
.
Air in the gas line.
.
Bleed gas line (initial startup only).
3.
Gas pressure too high or too low.
3.
Supply pressure should be 5" - 14" w.c. for natural gas or 11" - 14" w.c.
for propane gas.
4.
No Spark:
4.
a) Loose wire connections.
a) Be certain all wire connections are solid.
b) Transformer failure.
b) Be sure 24 volts is available.